- Joined
- Dec 1, 2016
- Messages
- 5,445
- Points
- 728
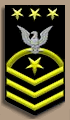
talking about removing the char from a laser cut in joinery.
this is a specialized kind of tool I use for removing the laser char and for relief carving. Yes you can carve with an airbrush something I learned from a glass sculpture back in my early days of graphic arts school. all you need is a drawing.
anyhow
here are a few links to videos showing micro sand blasting.
www.everythingairbrush.com
starting out I had mixed results until I got the air pressure just right and the flow of the grit but once I got the feel for it I could remove the char with just a couple passes.
I do have several air brushes and mini sand blasters you can do it with canned air if you don't want to invest in an air compressor.
I do have some experience using an air brush so it came easy for me. I use to air brush motorcycles and cars. I had this old GEO jeep that had at least 10 different paint jobs I use to practice on.
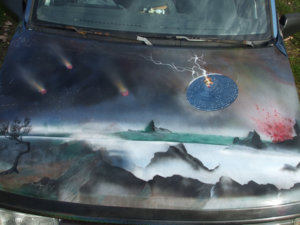
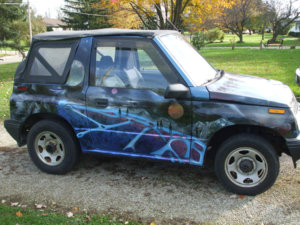
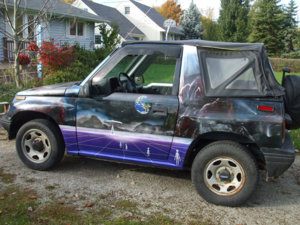
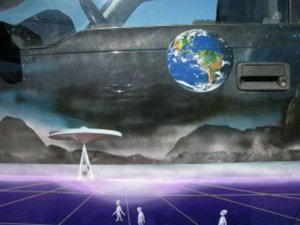
this is a specialized kind of tool I use for removing the laser char and for relief carving. Yes you can carve with an airbrush something I learned from a glass sculpture back in my early days of graphic arts school. all you need is a drawing.
anyhow
here are a few links to videos showing micro sand blasting.
Sandblasting Archives - Everything Airbrush
Ideal tools for de-rusting, engraving, etching, matt finishing, cleaning surfaces and hard to reach areas. Mini Sandblasters can create an endless variety of effects in glass etching and can also be used to prep wood, plastic and metal surfaces prior to spraying. Realistic weathering effects are...

starting out I had mixed results until I got the air pressure just right and the flow of the grit but once I got the feel for it I could remove the char with just a couple passes.
I do have several air brushes and mini sand blasters you can do it with canned air if you don't want to invest in an air compressor.
I do have some experience using an air brush so it came easy for me. I use to air brush motorcycles and cars. I had this old GEO jeep that had at least 10 different paint jobs I use to practice on.
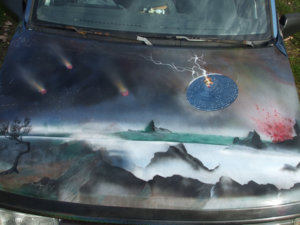
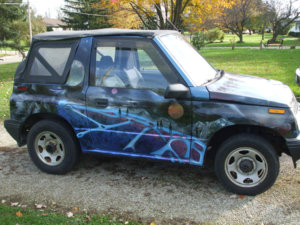
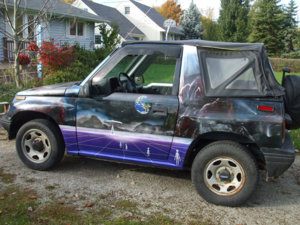
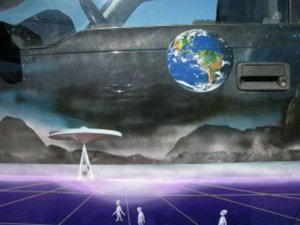