- Joined
- Jul 18, 2024
- Messages
- 396
- Points
- 278
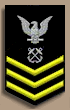
OK, so I got around how to ensure rails and profiles are connected by using the intersect thingy. And I can position canvasses.
But what is the best approach to create a hull? Loft from waterline to waterline, so top down, and use the profile lines (the ribs) as rails? Or loft front to back and use the horizontals as rails? I think the latter doesn’t work, but I’m curious how others solve their lofts.
Feel free to elaborate or digress.
But what is the best approach to create a hull? Loft from waterline to waterline, so top down, and use the profile lines (the ribs) as rails? Or loft front to back and use the horizontals as rails? I think the latter doesn’t work, but I’m curious how others solve their lofts.
Feel free to elaborate or digress.