The motor mount
The mount for the motor is very simple. I used a piece of the 5mm ply left over from the laser-cut sheets, cut to the size of the mounting plate and long enough to go across the gap between frame 6 & 7, with appropriate bevels to the ends and underneath to match both the angle to the frame and the alignment for the shaft. There is also a small wedge under the platform, on top of the keel, and later I added a couple of wedges underneath at right angles to the keel. It will all be epoxy glued together.
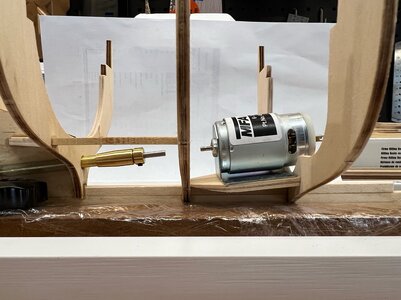
Looking good, until I realised (before gluing) that the outer hull planking is going to clash with the lower corner of the timber platform and probably any bolts I put in the aft set of holes of the metal mount (red highlight below). My solution was to hacksaw off the rear corners of the motor mount (orange dotted line below) and shape the timber platform to match.
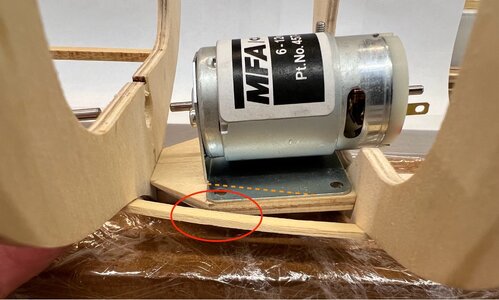
Like this…
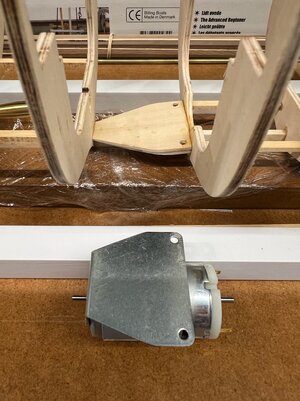
The motor doesn’t produce a lot of torque, so I think it would be fine with just two bolts…but, to be sure, to be sure, I’ll add (using epoxy) a small angle bracket to the rear nose of the mount so that it can be screwed centrally into the keel.
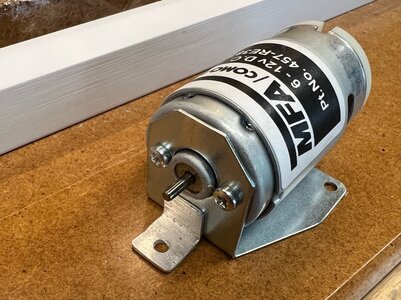
Next time, a bit of bracing.
The mount for the motor is very simple. I used a piece of the 5mm ply left over from the laser-cut sheets, cut to the size of the mounting plate and long enough to go across the gap between frame 6 & 7, with appropriate bevels to the ends and underneath to match both the angle to the frame and the alignment for the shaft. There is also a small wedge under the platform, on top of the keel, and later I added a couple of wedges underneath at right angles to the keel. It will all be epoxy glued together.
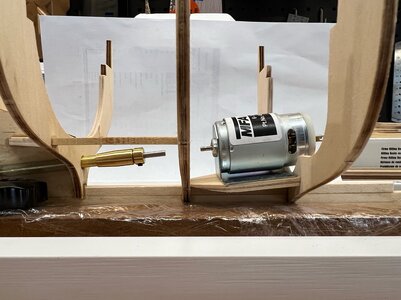
Looking good, until I realised (before gluing) that the outer hull planking is going to clash with the lower corner of the timber platform and probably any bolts I put in the aft set of holes of the metal mount (red highlight below). My solution was to hacksaw off the rear corners of the motor mount (orange dotted line below) and shape the timber platform to match.
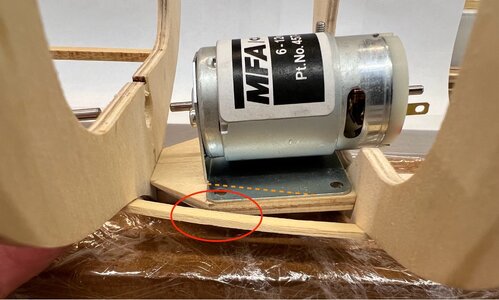
Like this…
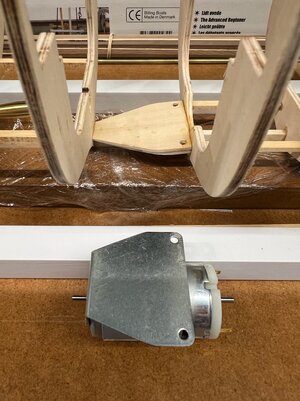
The motor doesn’t produce a lot of torque, so I think it would be fine with just two bolts…but, to be sure, to be sure, I’ll add (using epoxy) a small angle bracket to the rear nose of the mount so that it can be screwed centrally into the keel.
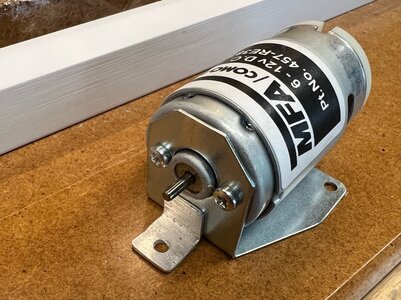
Next time, a bit of bracing.