- Joined
- Jun 30, 2012
- Messages
- 1,378
- Points
- 433
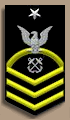
Scratchbuilding a small sailing ship.
Not much was needed in the way of material, just a couple of sheets of obechewood (a medium hard wood obtained from Ebay).
Balsa wood will work just as well, and can be cut with a scalpel.
I formed the sheer (curve of the deck) very simply. The gaps were filled in with wood filler. -
Next, I pasted a profile to the side of the block using a glue stick, and adeck plan on top, correctly lined up.
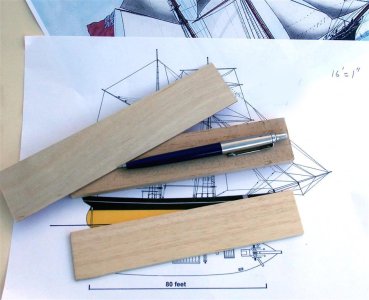

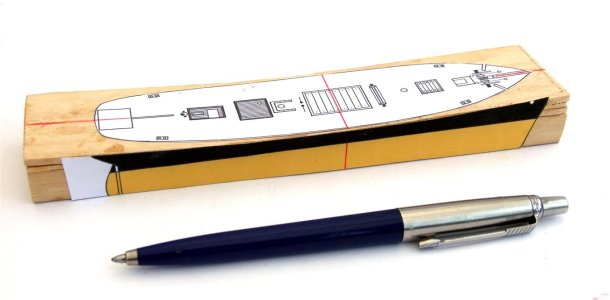
Not much was needed in the way of material, just a couple of sheets of obechewood (a medium hard wood obtained from Ebay).
Balsa wood will work just as well, and can be cut with a scalpel.
I formed the sheer (curve of the deck) very simply. The gaps were filled in with wood filler. -
Next, I pasted a profile to the side of the block using a glue stick, and adeck plan on top, correctly lined up.
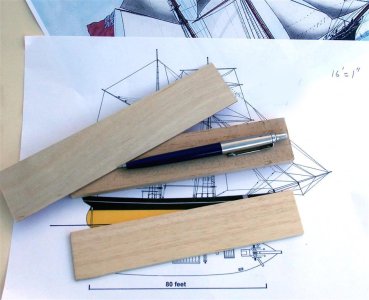

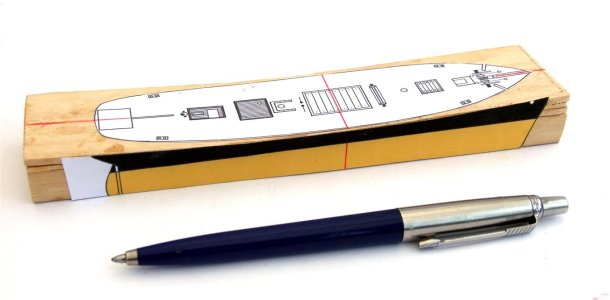