- Joined
- Dec 1, 2016
- Messages
- 5,445
- Points
- 728
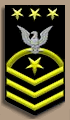
Take the cut out patterns and rubber cement them to cardboard, the type found as cereal boxes, or other food packaging boxed. The futtock patterns are glued to a backing
because these patterns may be used over and over when building a ship with 60 to 100 frames and you want to insure a clean straight line when tracing the angle to the wood. Cut strips of cardboard then glue on the patterns. Then with a razor blade cut the pieces apart to the angle on the pattern.
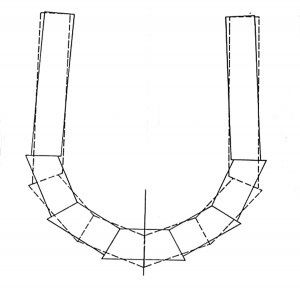
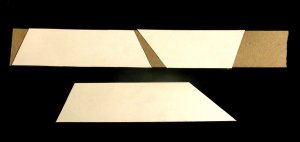
Finally trace the patterns on to the wood. The patterns are actually nested into one another to limit the amount of cutting needed and to conserve on material.
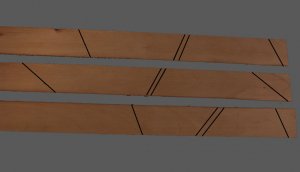
because these patterns may be used over and over when building a ship with 60 to 100 frames and you want to insure a clean straight line when tracing the angle to the wood. Cut strips of cardboard then glue on the patterns. Then with a razor blade cut the pieces apart to the angle on the pattern.
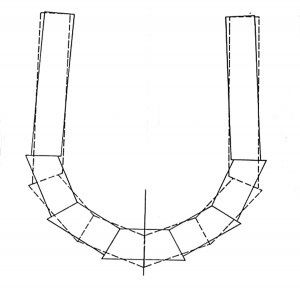
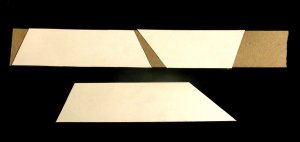
Finally trace the patterns on to the wood. The patterns are actually nested into one another to limit the amount of cutting needed and to conserve on material.
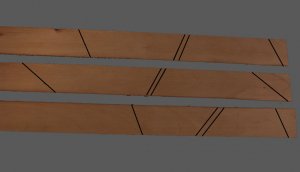