Looking for opinions and arguments.
Is it wise to remove the nails from the first planking after the glue has dried?
Or is it a no go?
I have performed this action on two ships so far. The first ship, Shackleton's Endurance, is still in shipshape condition three months after completion. But should I worry about the future?
I must add I pre-bent the (limewood) planks, and thus did not mount them under excessive strain. I also glued the sides of the planks, so not only the points of contact with the bulkheads
I have searched SOS in vain on this topic. Elsewhere opinions seem to be split.
The two pictures below are of HM Bark Endeavour, with and without nails.
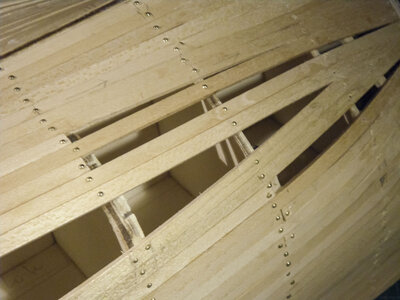
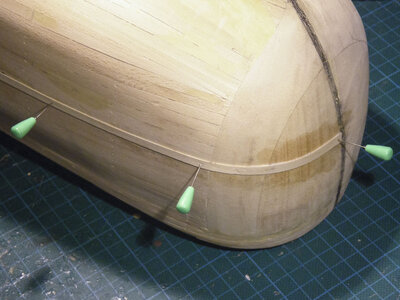
Is it wise to remove the nails from the first planking after the glue has dried?
Or is it a no go?
I have performed this action on two ships so far. The first ship, Shackleton's Endurance, is still in shipshape condition three months after completion. But should I worry about the future?
I must add I pre-bent the (limewood) planks, and thus did not mount them under excessive strain. I also glued the sides of the planks, so not only the points of contact with the bulkheads
I have searched SOS in vain on this topic. Elsewhere opinions seem to be split.
The two pictures below are of HM Bark Endeavour, with and without nails.
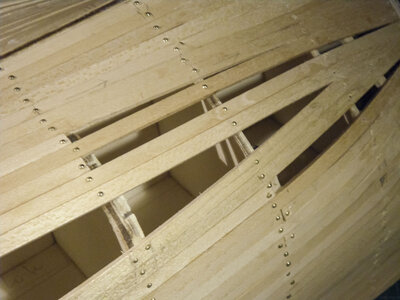
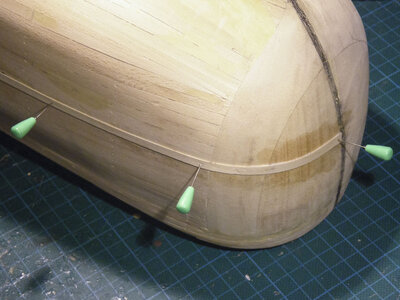
Last edited: