The box.
Standard ingredients: laser cut plywood sheets, planks, dowels, strips, rigging thread, plans and lots of shiny fittings. For reasons unknown the bulkheads are distributed over two plywood sheets of different colour and slightly differing thicknesses. The plans have a hand drawn appearance and are a bit approximate.. I took a lot of bulkhead measurements off a sheet purportedly representing the plywood sheets 1:1 only to find later that the actual bulkheads were different so I had to do it again. The keel and bulkheads fitted together very well. Some sample photos appended
First stage planking.
I hope at the second stage to bring all planks to the stem with a reasonable width (no points) rather than have the lower level planks curling up to meet the upper levels at an angle part way along the hull. This will involve tapering and, probably, a few drop planks.
By way of a rehearsal I chose to adopt the same approach to the first stage planking although a less formal approach would normally be used.
I was almost successful in this but was slightly derailed by the instructions. A line is specified on the plans for a starting plank. I followed this but the plank needed a bit of sideways force to comply. Instructions indicate five more planks below the starter with no tapering. The perimeter of the first few bulkheads is, as usuual, a lot less than that of the midship bulkheads. This instruction would plank over a lot of the precious space on the forward bulkheads so I tapered them a bit. I should have tapered them more and possibly included a drop plank. So I did end up with a few lower planks curling up to meet hight planks at an angle. A useful lesson to be applied at the second stage. I included a few formally shaped drop planks at the first stage as an exercise rather than the normal practice of leaving lune shaped gaps to be filled with pointy ended inserts. After dilligent application of my new scrapers I have ended up with a reasonably satisfactory result. There are a few small gaps and a bit of a mess low down at the stern deadwood but nothing that cannot be bridged with the second stage planking.
I used bow blocks shaped to continue the line of the first stage planking ready to receive the second stage
There is a small hole in the port bilge! I forgot to leave access to a screw that was holding the inverted assembly to a temporary support.
During the planking I pinned the planks to the bulkhead through 4mm wide strips of thin plywood. This made it easy to extract the pins without having to dig them out of the plank surface.
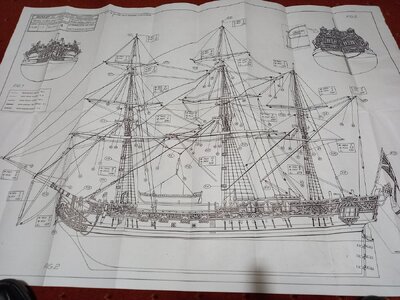
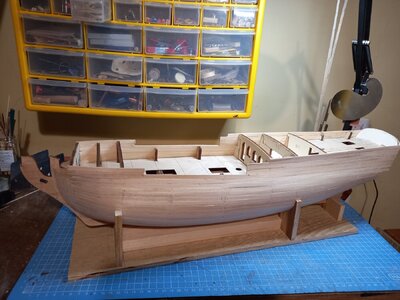
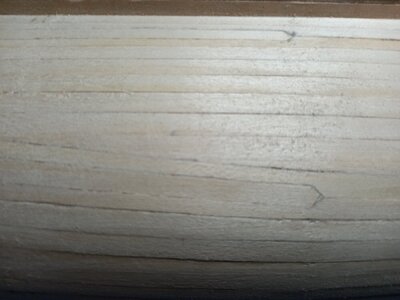
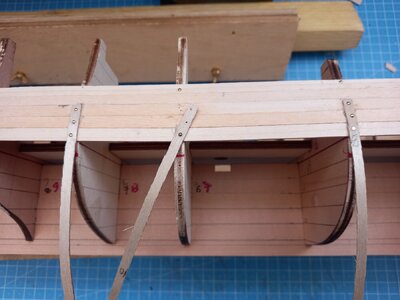
Standard ingredients: laser cut plywood sheets, planks, dowels, strips, rigging thread, plans and lots of shiny fittings. For reasons unknown the bulkheads are distributed over two plywood sheets of different colour and slightly differing thicknesses. The plans have a hand drawn appearance and are a bit approximate.. I took a lot of bulkhead measurements off a sheet purportedly representing the plywood sheets 1:1 only to find later that the actual bulkheads were different so I had to do it again. The keel and bulkheads fitted together very well. Some sample photos appended
First stage planking.
I hope at the second stage to bring all planks to the stem with a reasonable width (no points) rather than have the lower level planks curling up to meet the upper levels at an angle part way along the hull. This will involve tapering and, probably, a few drop planks.
By way of a rehearsal I chose to adopt the same approach to the first stage planking although a less formal approach would normally be used.
I was almost successful in this but was slightly derailed by the instructions. A line is specified on the plans for a starting plank. I followed this but the plank needed a bit of sideways force to comply. Instructions indicate five more planks below the starter with no tapering. The perimeter of the first few bulkheads is, as usuual, a lot less than that of the midship bulkheads. This instruction would plank over a lot of the precious space on the forward bulkheads so I tapered them a bit. I should have tapered them more and possibly included a drop plank. So I did end up with a few lower planks curling up to meet hight planks at an angle. A useful lesson to be applied at the second stage. I included a few formally shaped drop planks at the first stage as an exercise rather than the normal practice of leaving lune shaped gaps to be filled with pointy ended inserts. After dilligent application of my new scrapers I have ended up with a reasonably satisfactory result. There are a few small gaps and a bit of a mess low down at the stern deadwood but nothing that cannot be bridged with the second stage planking.
I used bow blocks shaped to continue the line of the first stage planking ready to receive the second stage
There is a small hole in the port bilge! I forgot to leave access to a screw that was holding the inverted assembly to a temporary support.
During the planking I pinned the planks to the bulkhead through 4mm wide strips of thin plywood. This made it easy to extract the pins without having to dig them out of the plank surface.
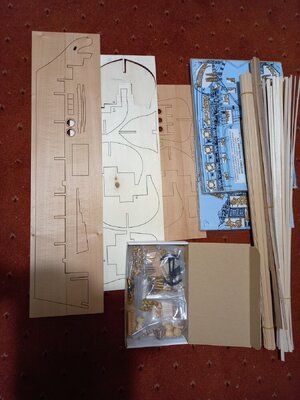
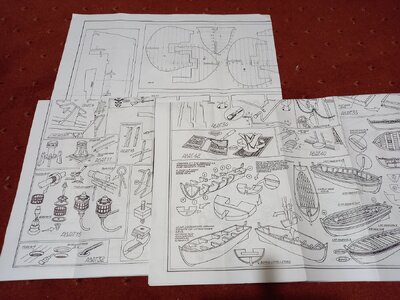
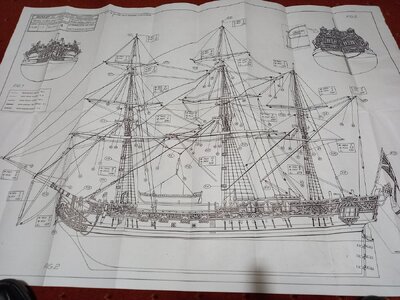
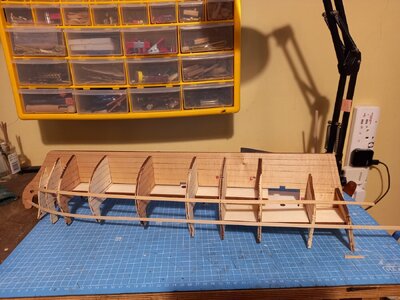
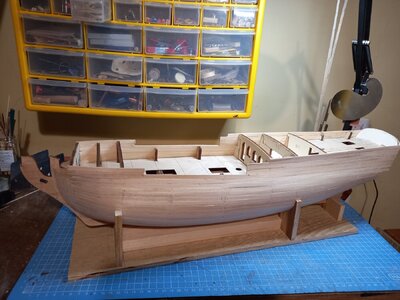
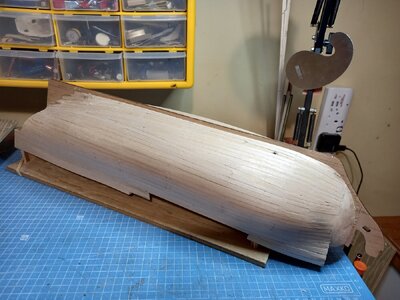
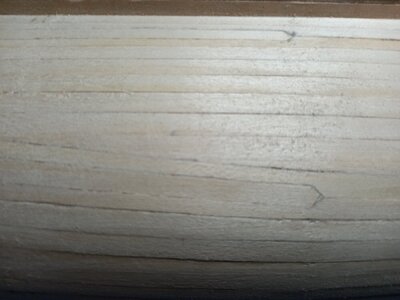
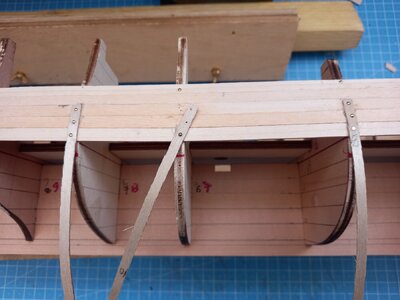