Shell plating: I am currently building a 1:96 scale model of the Great Lakes freighter Benjamin Noble. She was a steel hulled vessel built in 1909. Of course, the technology used to build her was exactly the same as that for Titanic; riveted steel plating. The scale is also very close to the 1:100 scale of your model. Unlike your model mine features a carved wooden hull with soldered brass upper works.
The first thing that a naval architecture student learned in the past was that a steel plate 1ft square x 1in thick weighs 40.8 lbs. This is used to specify plating thickness on shipbuilding drawings. A drawing specifying 20.4 pound plate is specifying material of 1/2 in thickness. Sometimes the fraction was skipped, so it was instead it was 10pound plate, 15 pound plate, 20 pound plate, etc. Depending on the source of your drawings you may encounter this nomenclature.
The plating was secured by riveting. Rivets were driven hot, so when cool provided a watertight joint. There were numerous types of rivets engineered for different applications but only two types that you need to be concerned with:
Pan Head rivets- These were heavy duty rivets intended for applications requiring high structural strength. ( photo). For most shell plating, the heavy Pan Head was on the inside of the hull and the “point” on the outside. The point was the part of the rivet that was “closed up”, (hammered into the hole). The hole was slightly conical so the shrinking rivet exerted enormous compressive force on the joint. If properly driven, these rivets are almost invisible to someone looking at the ship at scale distance.
Some high stressed areas of Titanic’s hull such as the sheer strake were riveted using a hydraulic riveting machine. The rest of the joints were riveted by hand. This was a huge machine shaped like a C, that was suspended by a shipyard crane. These rivets DO appear to be visible in photos.
Snap rivets- These were used in light duty applications where appearance was important. These are seen on deckhouses, smokestacks, etc. When closing the joint, a die was used to shape the rivet’s point.
Roger
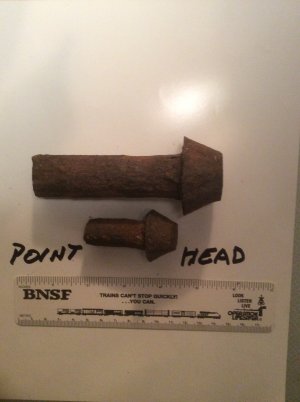