Better late than never... Finally I could come to the point that I can show something about the tools which I am using. I believe rotary carving is the best method for ship model decorations, but obviously other methods like knives, chisels have their own place there too. I am also using them occasionally, but I am using the rotary tools the most. At least for my way of working they are better and easier to control and also more productive. And they are not that far away from the knife blade anyhow, at least the milling bits, which can be interpreted as a series of blades on a cylindrical or spherical surface. As opposed to this the diamond bits are practically grinding stones and they work exactly like that.
I started carving small ship decorations quite a while ago, even not having any acceptable tool, and started just a few years ago making it a bit more seriously. At this stage I am making ship decorations (figure head, gingerbread, taffarel, etc) and stand-alone, somewhat bigger carvings, mostly figure heads or figure head compositions. Currently as I am working Sovereign of the Seas, there will be lots of carved decorations on her, mostly gingerbread-like decos, probably just the figure head is different, which I already started doing. As the hull will be planked, I will be able to start on them. There is no point doing them now as I don't know the exact sizes yet.
After trying a few other machines I settled with the Proxxon engraver for a while. Lightweight, reliable, easy to handle, but does not have too much torque. So as I started studying Bill Short's carving book (excellent stuff!) I had a look around and found the Micromotor. (I also tried flexible shafts also in-between- Proxxon as well as Dremel - but none of the was really comfortable.) Micromotor is not expensive (cheaper than Dremel) and knows everything what we want to have. Light-weight hand piece, connected to the base only with a flexible electric cord, so I can work with it for hours. Bits are easy to change. It slows down virtually to standstill, so the most important rev range of a few hundred rpms is there, and with tons of torque. Revs in both directions, controllable with a foot pedal (highly recommended) or with a fixed rev which can be set up on the power supply. This latter is part of the package of course. There are 2 different pedals, on-off only, or with a built-in speed control - I swear for the latter. But, strangely enough, I realize recently more and more recently that I am using the pre-set constant speed instead of the foot pedal. Laziness of course.
The Micromotor is readily available from eBay, I am using the South Korean Marathon type. (The bulk of them are used by nail artists). There are much more expensive types of course but I am fully satisfied with mine. As technology progresses so increases the rpm of the unit (I've got 35000 and 45000 ones, the newest ones spin at max 50-55000). This makes them more expensive of course, but luckily we don't need them, as we use the lowest revs anyhow. So the N2 or N3 units are good enough for our purposes. Mine is an N3. I have been using it for more than 5 years now, quite extensively, and did not have any problem with it ever.
Both Proxxon and Micromotor uses the same bits with shank sizes 3/32" or 2.35 mm. There are other shank sizes for different hand pieces but 3/32" is the most common size. I source mines from an English company, HSWELSH, but there are also others (ie. Busch) - look for Freizers on their site. The diamond ones are cheap, again can be bought on eBay, just make sure that the shaft size is correct. I am using 2 different sorts, 200 and 600 grit respectively.
It really depends on the individual to find out, which bit-shape is the most useful. Sphere bites very well, sometimes too well. It goes down to 0.3 mm diameter, which is very good for details. I preferred the flame shape first but now I tend to use the bud shape rather. And there are all sorts of cylindrical, conical etc. shapes which are good for different purposes. From the broken bits I create my own ones - just grinding it to a point and then hand-grind a few flats onto it on an oil stone. With these self made bits I can pre-'draw' on the wood and can use them for really fine details for which even the 0.3 mm bit is too big, such like face details.
Using diamond bits is again like grinding - can't go too bad (does not 'bite' as aggressively as the mill bits) but leaves rougher surface which then has to be smoothened. About finishing I will write a bit sometimes later.
I hope this short introduction give an idea what the hell is it about here. And the end result? I used to say to visitors proudly that I am just making some dust...
If any question, I am happy to mislead you guys... ))-
Janos
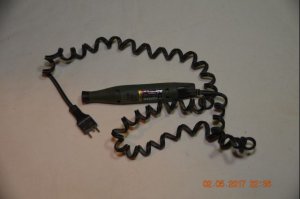
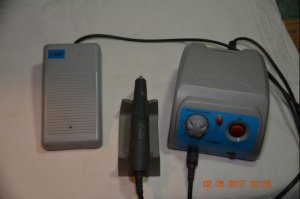
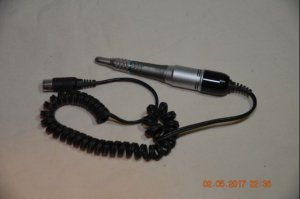
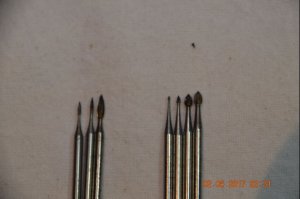
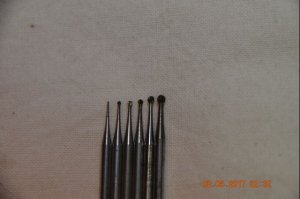
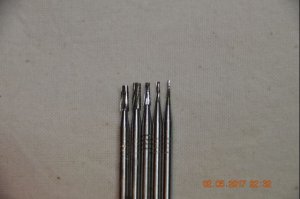

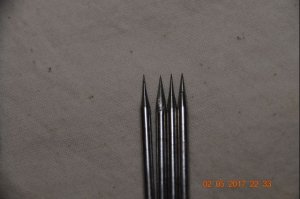
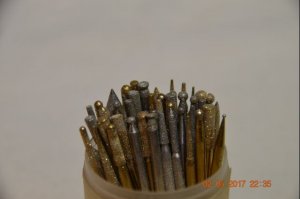
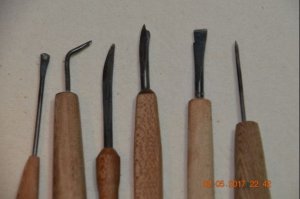
I started carving small ship decorations quite a while ago, even not having any acceptable tool, and started just a few years ago making it a bit more seriously. At this stage I am making ship decorations (figure head, gingerbread, taffarel, etc) and stand-alone, somewhat bigger carvings, mostly figure heads or figure head compositions. Currently as I am working Sovereign of the Seas, there will be lots of carved decorations on her, mostly gingerbread-like decos, probably just the figure head is different, which I already started doing. As the hull will be planked, I will be able to start on them. There is no point doing them now as I don't know the exact sizes yet.
After trying a few other machines I settled with the Proxxon engraver for a while. Lightweight, reliable, easy to handle, but does not have too much torque. So as I started studying Bill Short's carving book (excellent stuff!) I had a look around and found the Micromotor. (I also tried flexible shafts also in-between- Proxxon as well as Dremel - but none of the was really comfortable.) Micromotor is not expensive (cheaper than Dremel) and knows everything what we want to have. Light-weight hand piece, connected to the base only with a flexible electric cord, so I can work with it for hours. Bits are easy to change. It slows down virtually to standstill, so the most important rev range of a few hundred rpms is there, and with tons of torque. Revs in both directions, controllable with a foot pedal (highly recommended) or with a fixed rev which can be set up on the power supply. This latter is part of the package of course. There are 2 different pedals, on-off only, or with a built-in speed control - I swear for the latter. But, strangely enough, I realize recently more and more recently that I am using the pre-set constant speed instead of the foot pedal. Laziness of course.
The Micromotor is readily available from eBay, I am using the South Korean Marathon type. (The bulk of them are used by nail artists). There are much more expensive types of course but I am fully satisfied with mine. As technology progresses so increases the rpm of the unit (I've got 35000 and 45000 ones, the newest ones spin at max 50-55000). This makes them more expensive of course, but luckily we don't need them, as we use the lowest revs anyhow. So the N2 or N3 units are good enough for our purposes. Mine is an N3. I have been using it for more than 5 years now, quite extensively, and did not have any problem with it ever.
Both Proxxon and Micromotor uses the same bits with shank sizes 3/32" or 2.35 mm. There are other shank sizes for different hand pieces but 3/32" is the most common size. I source mines from an English company, HSWELSH, but there are also others (ie. Busch) - look for Freizers on their site. The diamond ones are cheap, again can be bought on eBay, just make sure that the shaft size is correct. I am using 2 different sorts, 200 and 600 grit respectively.
It really depends on the individual to find out, which bit-shape is the most useful. Sphere bites very well, sometimes too well. It goes down to 0.3 mm diameter, which is very good for details. I preferred the flame shape first but now I tend to use the bud shape rather. And there are all sorts of cylindrical, conical etc. shapes which are good for different purposes. From the broken bits I create my own ones - just grinding it to a point and then hand-grind a few flats onto it on an oil stone. With these self made bits I can pre-'draw' on the wood and can use them for really fine details for which even the 0.3 mm bit is too big, such like face details.
Using diamond bits is again like grinding - can't go too bad (does not 'bite' as aggressively as the mill bits) but leaves rougher surface which then has to be smoothened. About finishing I will write a bit sometimes later.
I hope this short introduction give an idea what the hell is it about here. And the end result? I used to say to visitors proudly that I am just making some dust...
If any question, I am happy to mislead you guys... ))-
Janos
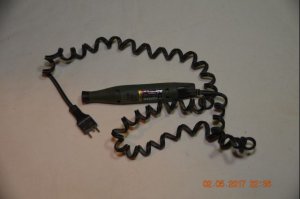
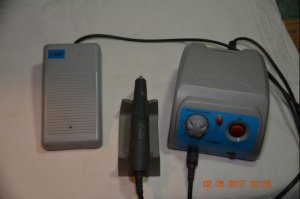
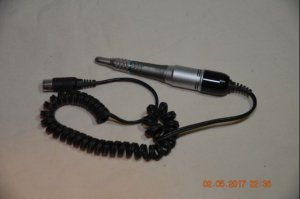
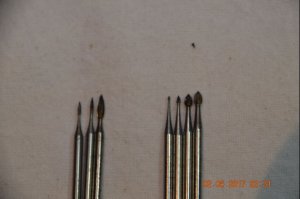
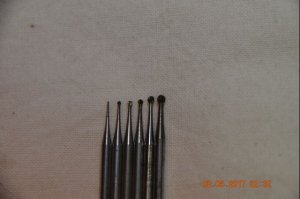
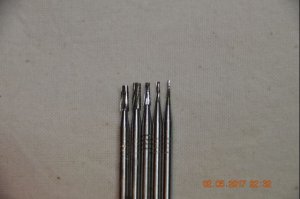

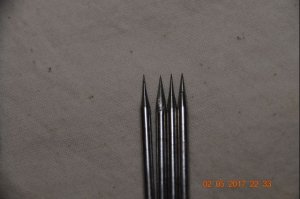
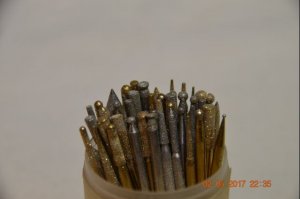
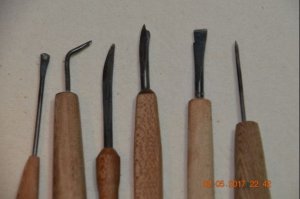