This a retro build log of the Boothbay 65, designed by naval architect Matthew Smith for Bristol Marine. It was to be set up to carry guests, including those in wheel chairs, on day sail trips. I was asked to build a model from the plans, some of which follow, but to my knowledge she has not yet been built. I recently contacted them to ask if it was still in the works but have not yet heard back. The model showed some changes were needed which was one of the purposes of the model project and was extremely interesting from start to finish.
Allan
The schooner
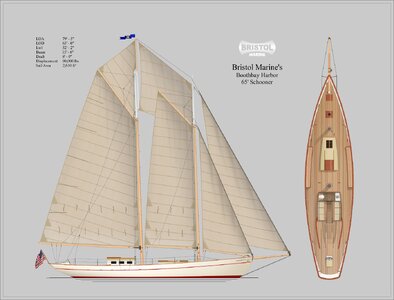
Lines and details were provided including the body plan from which I drew up and made the bulkheads. As time was of importance and the model was to be totally planked I chose POB rather than POF.
Body plan
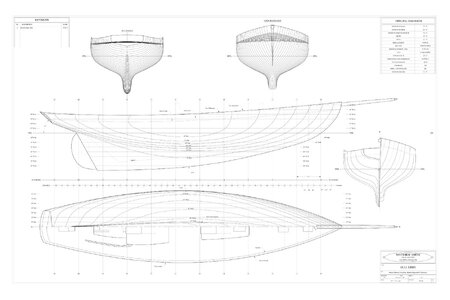
From this plan I redrew at scale and started with the bulkheads. Once the bulkheads, or frames when appropriate, are drawn I print them on label paper rather than on plain paper which then has to be glued to the wood. The label paper peels off the cutout part quite easily and leaves very little residue, if any.
Forward frames
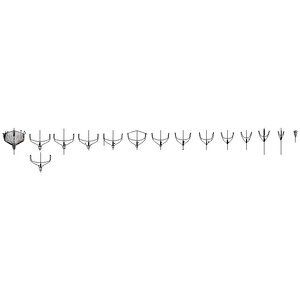
Assortment of cut out frames
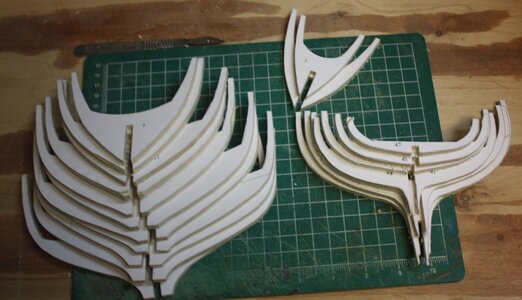
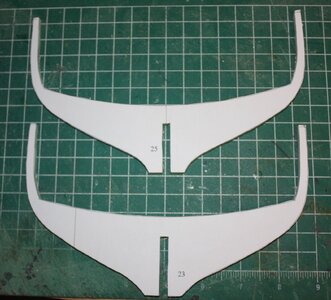
Allan
The schooner
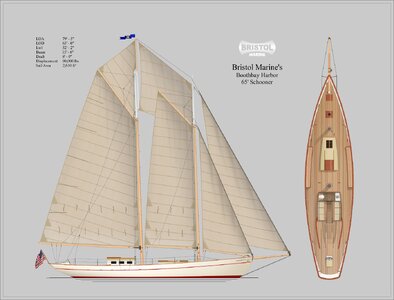
Lines and details were provided including the body plan from which I drew up and made the bulkheads. As time was of importance and the model was to be totally planked I chose POB rather than POF.
Body plan
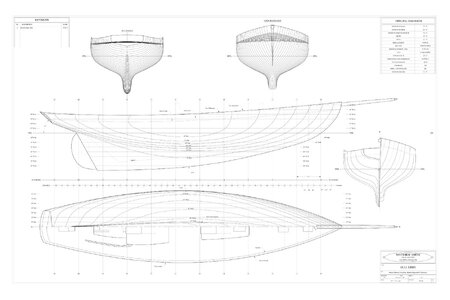
From this plan I redrew at scale and started with the bulkheads. Once the bulkheads, or frames when appropriate, are drawn I print them on label paper rather than on plain paper which then has to be glued to the wood. The label paper peels off the cutout part quite easily and leaves very little residue, if any.
Forward frames
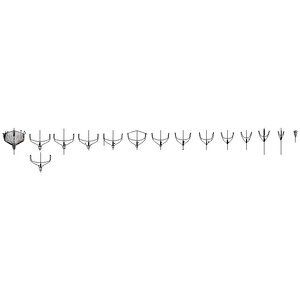
Assortment of cut out frames
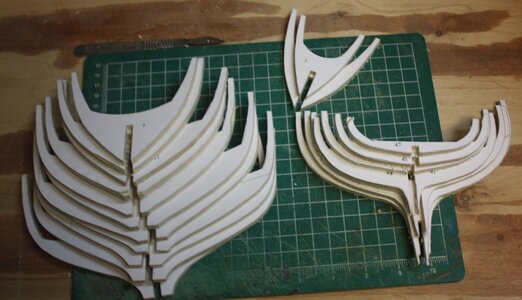
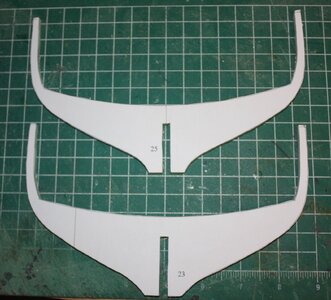
Last edited: