Thought Id share this method of tapering thin strips for hull planks.
I have concentrated on making ships boats for the past few years and have found that cutting thin tapered strip on my mini table saw is problematic. To overcome this I cut parallel strips, typically about 1.5mm thick and then taper them manually using sharp cabinet scrapers. The example shown has been tapered from 1.5mm thick down to 0.5mm using the large scrapper. The advantage is that it’s relatively quick and removes the saw blade marks with ease reducing or eliminating the need to sand. I would recommend you obtain quality scrapers and a burnishing rod from a to a reputable tool supplier as opposed to cheap internet versions and wet stones to keep them sharp.
Hope this is of use, happy modelling.
Cheers Rick
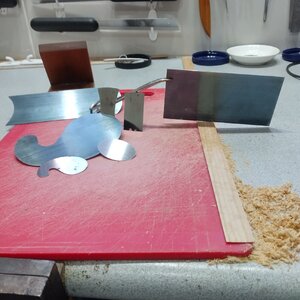
I have concentrated on making ships boats for the past few years and have found that cutting thin tapered strip on my mini table saw is problematic. To overcome this I cut parallel strips, typically about 1.5mm thick and then taper them manually using sharp cabinet scrapers. The example shown has been tapered from 1.5mm thick down to 0.5mm using the large scrapper. The advantage is that it’s relatively quick and removes the saw blade marks with ease reducing or eliminating the need to sand. I would recommend you obtain quality scrapers and a burnishing rod from a to a reputable tool supplier as opposed to cheap internet versions and wet stones to keep them sharp.
Hope this is of use, happy modelling.
Cheers Rick
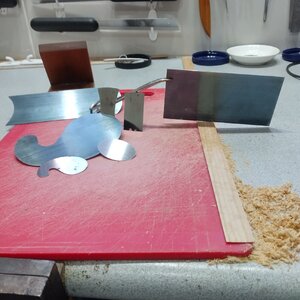