The showcase is dry.
For those who haven't done the showcase, I'll let myself share the steps.
There is nothing complicated.
I use glass - usually float glass with no anti-glare like anti-reflex etc.
I don't like plexiglass because it's easy to scratch, turn yellow over time and is more expensive.
This showcase measures 46x18x38 cm and costs around 6$v. The glass is 3mm thick. Thicker glass is of course used for larger showcases.
You must say to the glass worker by cutting it NOT to smooth the edges, because then it is difficult to stick - it remains a joint.
After the show case is dry, you can gently sand them down to prevent them from cutting.
The rule is - the front and rear windows are front. They stick to the edge of the two sides.
The showcase ceiling covers the front and back + both sides.
Here are the steps;
1. Put the top glass on the table - on a newspaper at least 3 layers.
2. Glue the first side glass - backing it up with something that does not fall while gluing one of the large pieces - front or back.
3. Glue one of the two large pieces - either front or back at right angles with the side glued.
So you already have 3 glued - the top, side and front glass. You can remove the support - silicone holds them, but still be careful
3. Glue the second side glass.
4. Glue the other large piece glass to the front or back.
5. Clamp with carpentry clamps carefully, if you do not have clamps, You can use tape
I stick with plain transparent silicone. Allows corrections about 20 minutes after application.
Full tightening - 24 hours.
The silicone can cleaned with a scalpel.
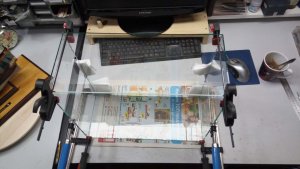
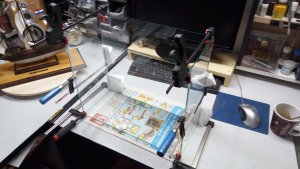