- Joined
- Feb 18, 2019
- Messages
- 712
- Points
- 353
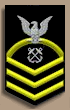
Here we will address:
All matters related to Applying finish.
All matters related to Applying finish.
**VIEW THREAD HERE** |
Your variation in width and color/species of strips really is brought out with the careful and patient finish. PT-2Well the goal is to get a "polished" finish, with no cracks showing without having to go through the process of fiber glassing the model (which of course could be an option). This of course begins with laying the strips as tight as possible, but it is not always the case. I personally spend a lot of time going over the planking throughout the building process for the best results.
It is difficult to show the finish through photos but I will try.
Here are a couple:
View attachment 178391
View attachment 178392
G.
Gilles, I recall that you mentioned earlier that you had tried mahogany but that it was too dark. I will be in the same position in the coming weeks and would like to know how you finished that canoe. My assumption at this point is to use the water based polyurethane as it doesn't darken the finish that much. Thanks for letting me know your recommendation. PT-2Your variation in width and color/species of strips really is brought out with the careful and patient finish. PT-2
Terrible news - hope you could restore some or all data......Hi Richard,
Sorry for the delay and inactivity these past few days, but I am having some computer problems lately: and they must be resolved as I recently lost a lot of files representing weeks of translation work done in the past couple of months.
Thank you for your reply. I may try some experimental pieces before go the whole nine yards. I hope that your computer problems and recovery works out. These devices can be Jeckle and Hyde monsters. PT-2Hi Richard,
Sorry for the delay and inactivity these past few days, but I am having some computer problems lately: and they must be resolved as I recently lost a lot of files representing weeks of translation work done in the past couple of months.
Anyways, I did use oil based varnish for the mahogany built canoes as I gave me the best looking "warm" finish, although it was very dark.
G.
This is the highest mirror gloss sheen that I have seen on any of your previous canoes. It is almost hard to see the canoe in this perspective. Dedicated work as always on your part. PT-2The outside of the canoe's hull may be finished using "spar varnish".
As you have read, these days I tend to use a number of thin coats of water based varnish.
This is the latest canoe, #5, which is a 17-inch pear wood. It is in the final stages of construction.
The outside is obviously painted green. Two coats of gloss spar varnish was applied with light sanding (600 grit paper) between coats. As this canoes still needs to be handled a bit for some detailing in the inside, a third coat, final coat, will be applied when everything is done and the canoe is ready for display. Two coat would probably be enough but I really want the finish to be "glass like": plus it gives the impression that "fiberglassing" is part of the finish.
In the end, whether 9 coats of water based varnish or 3 coats of oil based (or spar varnish) is used, the time needed to do this work is about the same: 3 to 4 days in order for the finish to properly "dry" and start the varnish curing process.
Here is a close-up view:
View attachment 185610
G.
That would be because the outside of this last one is finished with gloss spar varnish.This is the highest mirror gloss sheen that I have seen on any of your previous canoes. It is almost hard to see the canoe in this perspective. Dedicated work as always on your part. PT-2
So here is another view of the high gloss finished achieved with oil (spar) varnish.
View attachment 186020
I wonder if
It is mostly a reflection of my thumb but some of the hand can also be seen.I wonder if I am seeing your face mirrored on the bow. This view gives me a better impression of that finished canoe. . . although it is artistic license and not an actual replication of a canvas/panel stripper I think. An amazing finish. PT-2
You have strip planking joinery to a high level of excellence that I have not seen in any of the other builds with their layers of filler/paste to sand off for their painted finishes. I knew there was no canvas involved in your finish but was thinking about a finish on a full size canvas canoe if it would be similar to your mirror finish. PT-2It is mostly a reflection of my thumb but some of the hand can also be seen.
No canvas between wood / paint and the varnishing process. The joint between strips must very tight throughout as no filler was applied before painting the surface.
- 2 two coats of paint
- 3 coats of varnish.
G.