Friends,
Today I start the build.
I had been thinking for a while that a building table with T-tracks would be very helpful for this big project.
I bought a pre-made Melamine T-track board 1" x 40" x 26" from Rockler with a few clamps and accessories to fit on the rails. Rockler has a multiple clamps and devices that slide on the rails.
First order of business was to secure the T-track board on my building table with double stick foam tape and organize the shop for the new build.
Next, I put the keel plan between glass panes to smooth it out. The keel structure will then be assembled followed by the building jig.
The sheets containing the parts forming the keel structure and the parts themselves are very clearly marked. The wood is top quality, and the laser cuts are perfect, cutting completely through the sheet. The plans are very good, with parts' numbers clearly marked; I have the instruction manual on my I-pad right in front of me.
Next I will remove the keel and apron parts from the sheets, and clean up the laser char.
Once detailed and dry-fitted, the keel parts will be glued with a glue stick to the plan and assembled using wood glue.
The keel structure will then be sandwiched between two glass panes. while the building jig is assembled
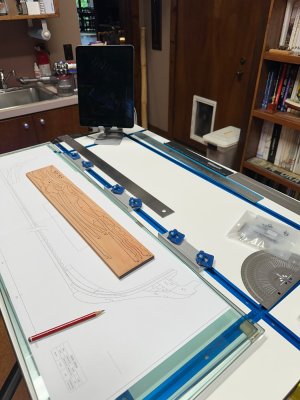
Here is my new building table with T tracks !
Alex R
Today I start the build.
I had been thinking for a while that a building table with T-tracks would be very helpful for this big project.
I bought a pre-made Melamine T-track board 1" x 40" x 26" from Rockler with a few clamps and accessories to fit on the rails. Rockler has a multiple clamps and devices that slide on the rails.
First order of business was to secure the T-track board on my building table with double stick foam tape and organize the shop for the new build.
Next, I put the keel plan between glass panes to smooth it out. The keel structure will then be assembled followed by the building jig.
The sheets containing the parts forming the keel structure and the parts themselves are very clearly marked. The wood is top quality, and the laser cuts are perfect, cutting completely through the sheet. The plans are very good, with parts' numbers clearly marked; I have the instruction manual on my I-pad right in front of me.
Next I will remove the keel and apron parts from the sheets, and clean up the laser char.
Once detailed and dry-fitted, the keel parts will be glued with a glue stick to the plan and assembled using wood glue.
The keel structure will then be sandwiched between two glass panes. while the building jig is assembled
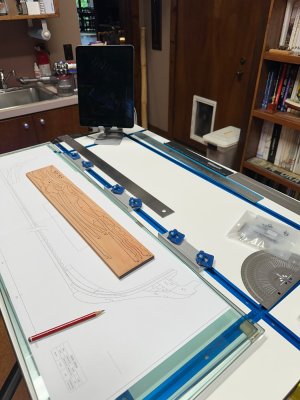
Here is my new building table with T tracks !
Alex R