One of the disadvantages of making ship models for about 40 years is running out of space to house them. To keep on with the hobby I have started to build smaller vessels and give them to friends and family. In looking to start a new modeling project, I went to my favorite source for plans, Howard Chapelle's, “The Search for Speed Under Sail”. Almost all of the vessels he discusses are lovely to my eye and I have made at least 5 models from plans in this book. Berbice, an American built schooner dating from about 1780 with an overall length of 78'8”, met my size criteria. The lines plans are shown below and a rigging plan is also provided in the book:
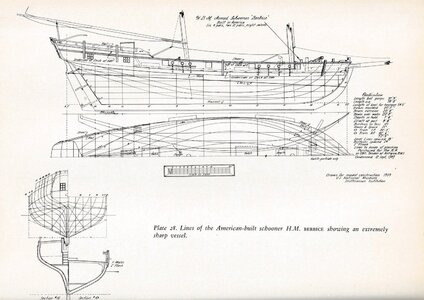
By enlarging the drawings to 1/85 scale, the plan would fit on a single sheet of 8.5” x 11.5” paper and could be reproduced on my home copier.
In previous logs in this forum I have discussed in detail my plank on bulkhead building methods so this log for Berbice will be abbreviated and just point out a few of the building details for this particular vessel.
Skeleton Construction
The keel piece and bulkheads were made from 1/8” plywood. After the bulkheads were inserted into the keel piece, sections of 1/4” dowel were glued between the bulkheads to stiffen the skeleton and prevent warping. Filler blocks were also added at the bow and stern.
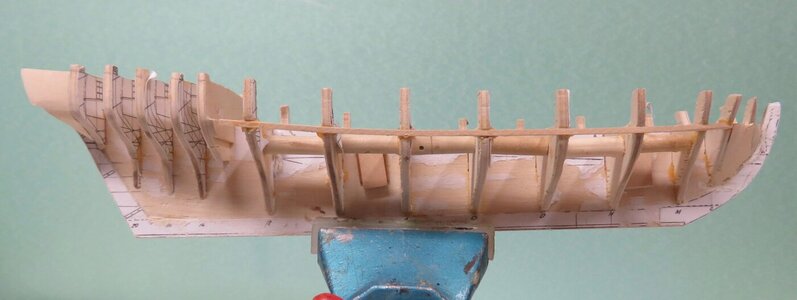
Next was to add the decks. A cardstock template was cut for the main deck and slots were added to fit around the bulkhead extensions.

A similar template was made for the quarter deck. These were then used as patterns for the 1/32” plywood sub-decks which were glued and nailed in place.
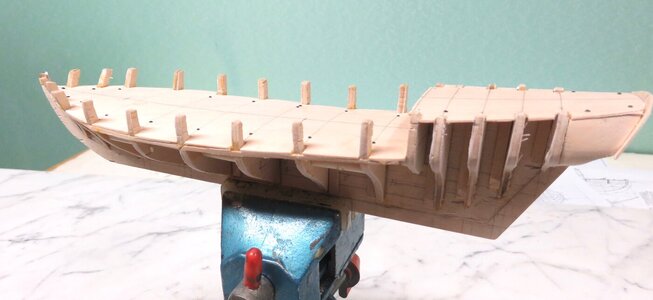
For the transom, two pieces of 1/32” plywood were overlaid and cut to the shape. The first piece was glued and nailed to the stern.
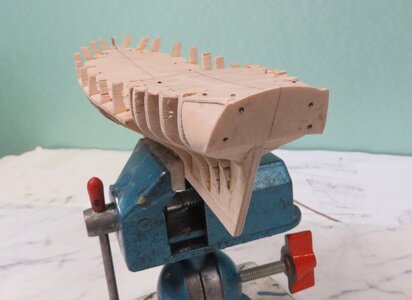
Lights and moldings will be added to the second piece, and it will later be attached to the first piece on the model.
First Planking
With the framing complete, battens were used to lay out a planking pattern. In view of the small size of this model I used leftover 1/32” hardwood for the first planking instead of the usual 1/16” basswood. It was a bit more difficult to work with but presented no real problems. Plank width in scale was 4mm. The model with first planking complete is shown below:
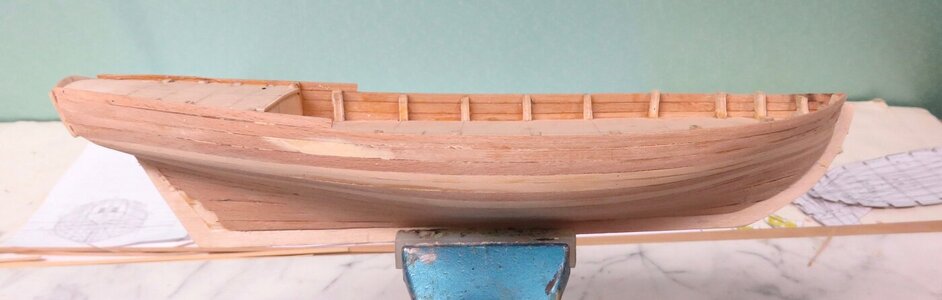
Note the planks at the stern in the deadwood area do not extend to the rabbet line cut 1/32" deep into the keel piece. This was done so that the second planking will give a flush fit when added.
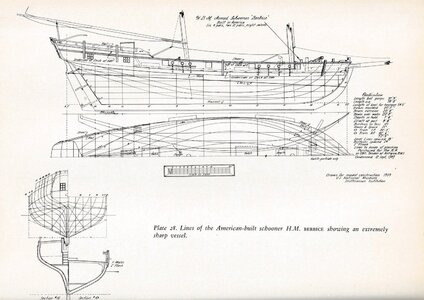
By enlarging the drawings to 1/85 scale, the plan would fit on a single sheet of 8.5” x 11.5” paper and could be reproduced on my home copier.
In previous logs in this forum I have discussed in detail my plank on bulkhead building methods so this log for Berbice will be abbreviated and just point out a few of the building details for this particular vessel.
Skeleton Construction
The keel piece and bulkheads were made from 1/8” plywood. After the bulkheads were inserted into the keel piece, sections of 1/4” dowel were glued between the bulkheads to stiffen the skeleton and prevent warping. Filler blocks were also added at the bow and stern.
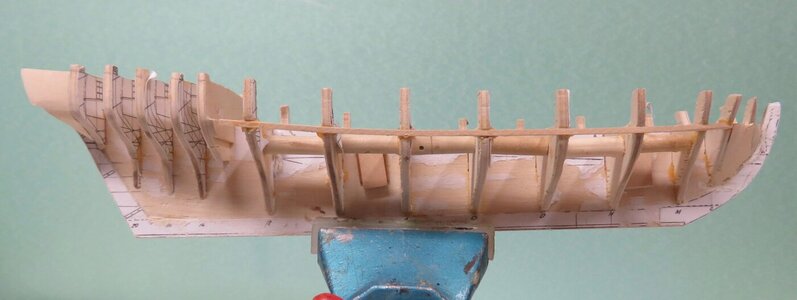
Next was to add the decks. A cardstock template was cut for the main deck and slots were added to fit around the bulkhead extensions.

A similar template was made for the quarter deck. These were then used as patterns for the 1/32” plywood sub-decks which were glued and nailed in place.
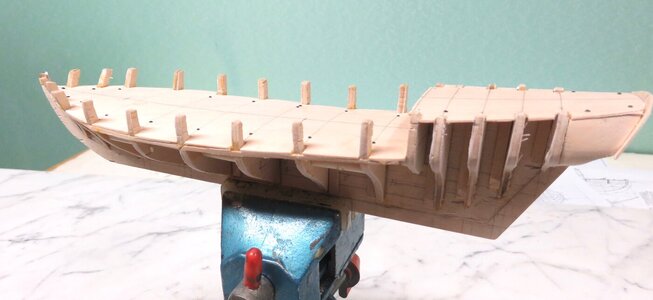
For the transom, two pieces of 1/32” plywood were overlaid and cut to the shape. The first piece was glued and nailed to the stern.
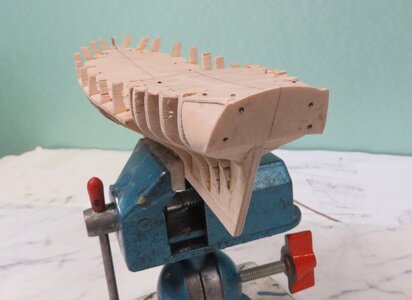
Lights and moldings will be added to the second piece, and it will later be attached to the first piece on the model.
First Planking
With the framing complete, battens were used to lay out a planking pattern. In view of the small size of this model I used leftover 1/32” hardwood for the first planking instead of the usual 1/16” basswood. It was a bit more difficult to work with but presented no real problems. Plank width in scale was 4mm. The model with first planking complete is shown below:
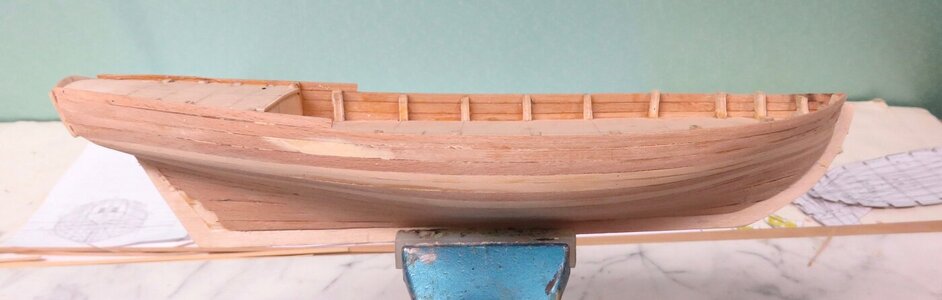
Note the planks at the stern in the deadwood area do not extend to the rabbet line cut 1/32" deep into the keel piece. This was done so that the second planking will give a flush fit when added.