Hi, I’m building Billing Boats Mary Ann (kit no. 472). This kit is rated as ‘Advanced Beginner’ by Billing and I think that’s probably a reasonable description of my skills as this is my first boat build, but I’ve been building planes from balsa, and other kits, on an occasional basis for more than 50 years. I haven’t seen too many build logs of Mary Ann, particularly with the additions I’m planning to make, so I thought that this might be useful to others setting out on a similar path. I’m planning on putting up plenty of photos and describing what worked for me and what I’ve found needed changing from the kit. (Please let me know if it gets to be too much)
I like ‘working boats’, preferably from the first half of the 20th century, so this trawler with its nicely rounded stern and its generally solid proportions has much appeal. As a first build, I was also looking for something that wasn’t too big (550mm long, 430mm high, 1/33 scale) and needed to be planked (a skill I’d like to develop). To add to the challenge, I plan to turn this static model into a working RC model and add some lighting.
I had to look around for some time just to get my hands on the kit in Australia, and I ended up buying it online from NZ and shipped it over.
So, here is what the kit looks like in the box…
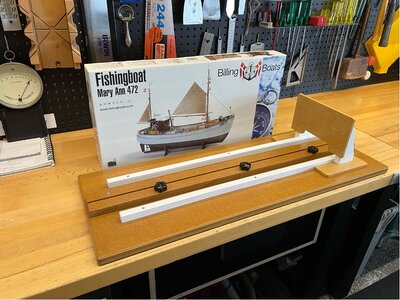
While waiting for the kit, I built a building jig as shown above, out of some leftover MDF I had in the workshop.
I like ‘working boats’, preferably from the first half of the 20th century, so this trawler with its nicely rounded stern and its generally solid proportions has much appeal. As a first build, I was also looking for something that wasn’t too big (550mm long, 430mm high, 1/33 scale) and needed to be planked (a skill I’d like to develop). To add to the challenge, I plan to turn this static model into a working RC model and add some lighting.
I had to look around for some time just to get my hands on the kit in Australia, and I ended up buying it online from NZ and shipped it over.
So, here is what the kit looks like in the box…
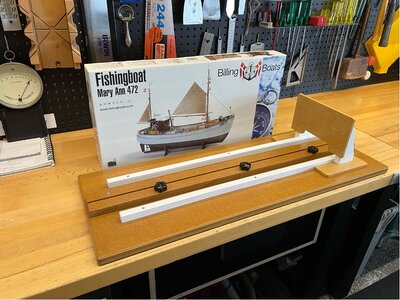
While waiting for the kit, I built a building jig as shown above, out of some leftover MDF I had in the workshop.