- Joined
- Feb 1, 2025
- Messages
- 7
- Points
- 43

Building “La Pinta” from Artesania kit
Early in 2024 I bought the kit for La Pinta, one of Columbus’ ships which sailed to America in 1492. I was in need of a hobby after selling our beach-house which had become too much of a burden with a big garden and always repairs to be done, so I returned to making models of old sailing ships.
Overall the kit was pretty good but as usual the instructions were in broken English and used some terms which had been lost in translation. One criticism would be that some of the sheaves appear to be too big for the model, especially the rectangular blocks which are tethered close to the deck.
Setting up the frames was straightforward and I used sanding blocks to adjust them to receive the first layer of planking. The two layers of decking fitted well and kept the frames perpendicular to the keel. Frames and decking were glued with PVA. I glued the decking also with PVA glue, using wooden clothes pegs where needed. Mostly the thin planking stuck within a few minutes with only a bit of finger pressure. Note that I am a bit lazy and have not gone to the trouble of blackening the edge of the planks to imitate caulking nor have I marked the planks as if they were only a couple of metres long.
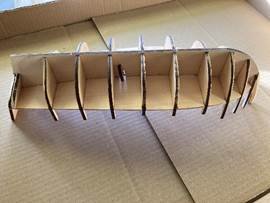
The first layer of planking went on pretty well again using PVA glue. I used pegs and steel alligator clips and rubber bands where needed, but also nails which were driven part way in and bent over for later removal. Planks were soaked in water prior to fitting, and temporarily attached and allowed to dry before final gluing. Shaping of planks was done with both sanding blocks and scalpel blade.
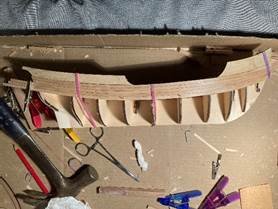
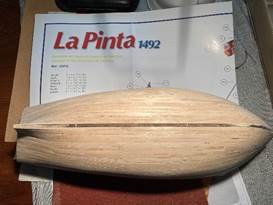
A pre-mixed wood filler was used to spread over the hull and correct for most of the irregularities. I made sure this was easy to sand away before I used it – some wood fillers dry very hard and make it difficult to pierce with nails when fitting the second layer.
When I was happy with the finish, I began to apply the second layer of planks which were about 0.5mm thick so very pliable and tended to stick well to the first layer with a thin layer of PVA applied to each plank. Although I tapered the planks as I went, I still had to insert some narrow pieces to complete the hull near the keel. However, not many people look too closely!!
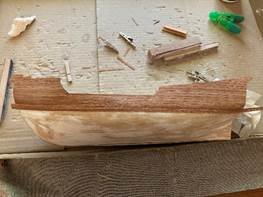
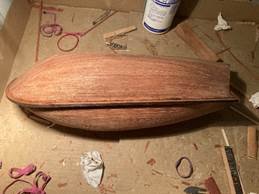
The next job was to attach the two “rub-rails” for want of a better term. I used 5 minute epoxy for this as there was some tension even after wetting the timber and attaching it temporarily.
I decided then that after sanding the hull and decks I would give it a coat of polyurethane varnish which I had left over from a pirogue I built – I used gloss but satin would have been better.
Next I followed the various instructions to make the deck fittings and ladders. Under the hatch covers I painted a black square as suggested by Artesania to resemble the hold. The pictures below show most of these details.
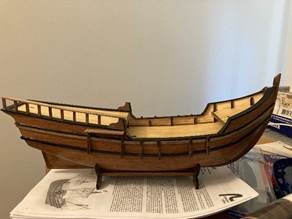
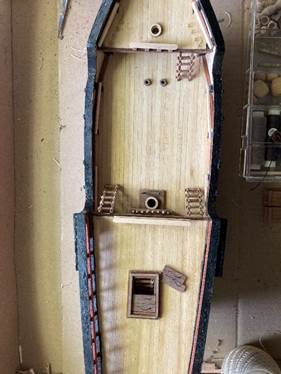
At this stage I fitted the rudder. The hinges provided were of rather poor quality and although I used them, I wasn’t particularly happy with the result.
Next came the standing rigging. The masts and other spars needed to be tapered and most of that was done on my wood-turning lathe using a 3-jaw chuck and sandpaper. A couple of the smaller spars were done by hand. Stepping the masts was simple enough, and in this older ship there were fairly clumsy pulleys at the top of the masts (not found in later ships) for raising the sails. Then I fitted the dead-eyes to the hull as instructed and began to make up the ratlines. First I knotted the dead-eyes to some thicker thread than provided (actually bamboo thread which I dyed black with acrylic paint diluted with water) and then whipped the threads to look authentic. I bunched the shrouds together and attached them directly to the masts using thick thread. This is not the best way but it looks OK for a small job like this. In future I will make up the shrouds and rat-lines by attaching pairs of threads to the mast first port-side then starboard-side, and assembling them in much the same way as they would have been done in the actual ships. Once the shrouds were tensioned on the dead-eyes, I began the rather tedious job of attaching the rat-lines. However, taking time and care with these is well worthwhile. I use undiluted PVA on the knots, and even if some of the glue spreads over the “ropes” it doesn’t matter for the final effect.
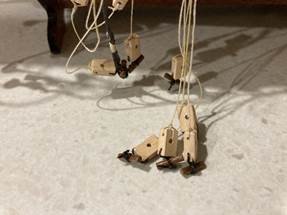
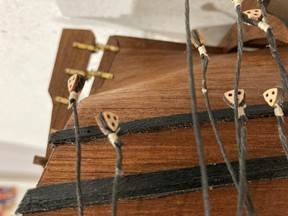
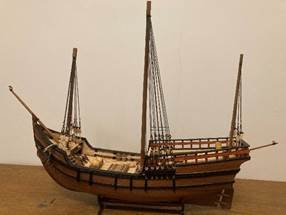
The individual sheaves for the rest of the rigging are attached using knots and whipping of the threads as per the drawings supplied. Some need to be made up from blocks of soft wood in the kit. Several drill bits of 0.5mm and 1 mm are very useful here, and I use an Ozito (copy of Dremel) tool for a lot of the drilling and any shaping is done with dental burrs which are a very useful bit of equipment for any modeller.
The sails as supplied were satisfactory. The kit suggested using weak tea to stain them but I didn’t do this. Instead I soaked them in a weak solution of PVA glue (starch would do the same thing) and then left them to dry over a couple of glass bottles wrapped in polythene sandwich wrap. There were 2 templates supplied to draw the crosses on the sails and I used them to give the outline with red ballpoint pen and then painted on both sides of the sail with red acrylic artists’ paint.
Then the sails were stitched to the appropriate spars and the ropes and pulleys used to finish the model.
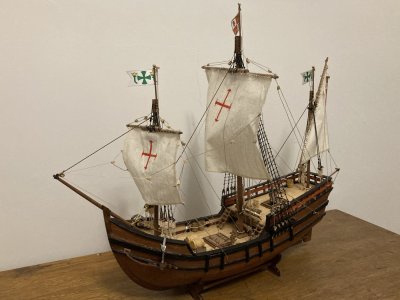
This was a nice little project, took about 3-4 months. The flags and bunting are a bit too “plasticky” for my liking, but overall the quality was all right. As these kits come from Hong Kong now I believe, then there may be some problems with quality in future.
Early in 2024 I bought the kit for La Pinta, one of Columbus’ ships which sailed to America in 1492. I was in need of a hobby after selling our beach-house which had become too much of a burden with a big garden and always repairs to be done, so I returned to making models of old sailing ships.
Overall the kit was pretty good but as usual the instructions were in broken English and used some terms which had been lost in translation. One criticism would be that some of the sheaves appear to be too big for the model, especially the rectangular blocks which are tethered close to the deck.
Setting up the frames was straightforward and I used sanding blocks to adjust them to receive the first layer of planking. The two layers of decking fitted well and kept the frames perpendicular to the keel. Frames and decking were glued with PVA. I glued the decking also with PVA glue, using wooden clothes pegs where needed. Mostly the thin planking stuck within a few minutes with only a bit of finger pressure. Note that I am a bit lazy and have not gone to the trouble of blackening the edge of the planks to imitate caulking nor have I marked the planks as if they were only a couple of metres long.
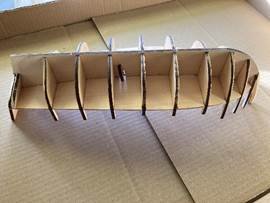
The first layer of planking went on pretty well again using PVA glue. I used pegs and steel alligator clips and rubber bands where needed, but also nails which were driven part way in and bent over for later removal. Planks were soaked in water prior to fitting, and temporarily attached and allowed to dry before final gluing. Shaping of planks was done with both sanding blocks and scalpel blade.
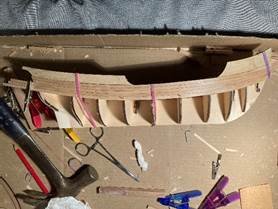
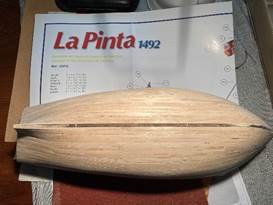
A pre-mixed wood filler was used to spread over the hull and correct for most of the irregularities. I made sure this was easy to sand away before I used it – some wood fillers dry very hard and make it difficult to pierce with nails when fitting the second layer.
When I was happy with the finish, I began to apply the second layer of planks which were about 0.5mm thick so very pliable and tended to stick well to the first layer with a thin layer of PVA applied to each plank. Although I tapered the planks as I went, I still had to insert some narrow pieces to complete the hull near the keel. However, not many people look too closely!!
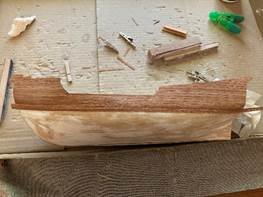
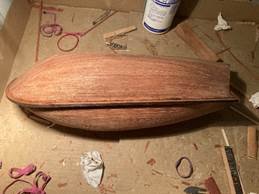
The next job was to attach the two “rub-rails” for want of a better term. I used 5 minute epoxy for this as there was some tension even after wetting the timber and attaching it temporarily.
I decided then that after sanding the hull and decks I would give it a coat of polyurethane varnish which I had left over from a pirogue I built – I used gloss but satin would have been better.
Next I followed the various instructions to make the deck fittings and ladders. Under the hatch covers I painted a black square as suggested by Artesania to resemble the hold. The pictures below show most of these details.
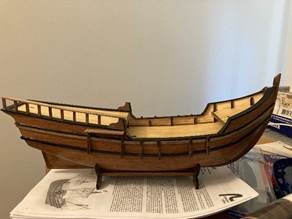
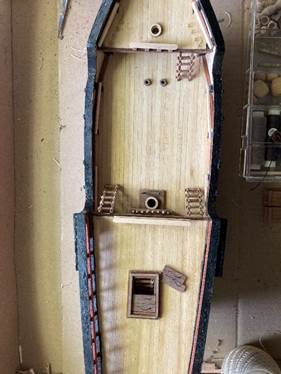
At this stage I fitted the rudder. The hinges provided were of rather poor quality and although I used them, I wasn’t particularly happy with the result.
Next came the standing rigging. The masts and other spars needed to be tapered and most of that was done on my wood-turning lathe using a 3-jaw chuck and sandpaper. A couple of the smaller spars were done by hand. Stepping the masts was simple enough, and in this older ship there were fairly clumsy pulleys at the top of the masts (not found in later ships) for raising the sails. Then I fitted the dead-eyes to the hull as instructed and began to make up the ratlines. First I knotted the dead-eyes to some thicker thread than provided (actually bamboo thread which I dyed black with acrylic paint diluted with water) and then whipped the threads to look authentic. I bunched the shrouds together and attached them directly to the masts using thick thread. This is not the best way but it looks OK for a small job like this. In future I will make up the shrouds and rat-lines by attaching pairs of threads to the mast first port-side then starboard-side, and assembling them in much the same way as they would have been done in the actual ships. Once the shrouds were tensioned on the dead-eyes, I began the rather tedious job of attaching the rat-lines. However, taking time and care with these is well worthwhile. I use undiluted PVA on the knots, and even if some of the glue spreads over the “ropes” it doesn’t matter for the final effect.
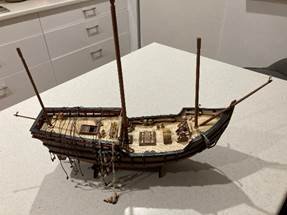
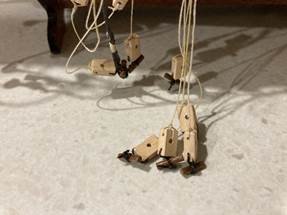
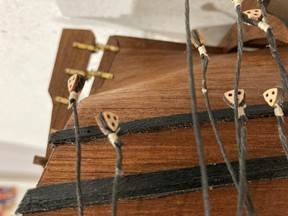
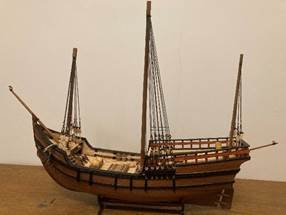
The individual sheaves for the rest of the rigging are attached using knots and whipping of the threads as per the drawings supplied. Some need to be made up from blocks of soft wood in the kit. Several drill bits of 0.5mm and 1 mm are very useful here, and I use an Ozito (copy of Dremel) tool for a lot of the drilling and any shaping is done with dental burrs which are a very useful bit of equipment for any modeller.
The sails as supplied were satisfactory. The kit suggested using weak tea to stain them but I didn’t do this. Instead I soaked them in a weak solution of PVA glue (starch would do the same thing) and then left them to dry over a couple of glass bottles wrapped in polythene sandwich wrap. There were 2 templates supplied to draw the crosses on the sails and I used them to give the outline with red ballpoint pen and then painted on both sides of the sail with red acrylic artists’ paint.
Then the sails were stitched to the appropriate spars and the ropes and pulleys used to finish the model.
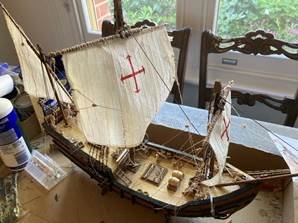
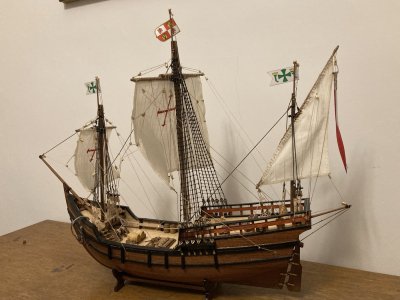
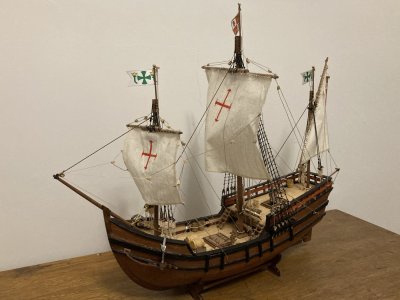
This was a nice little project, took about 3-4 months. The flags and bunting are a bit too “plasticky” for my liking, but overall the quality was all right. As these kits come from Hong Kong now I believe, then there may be some problems with quality in future.