- Joined
- Dec 1, 2016
- Messages
- 6,049
- Points
- 728
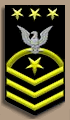
PART 24
installing the knees
Ships built on the lakes in North America from the study of various ship wrecks show hanging knees were not used when building a deck. Lodging knees were used in most cases but not in every case. a system was used where the ends of the deck beams were set in a shallow notch in the deck clamp and a heavy waterway timber was place on top of the beam.
For the Caustic i did use lodging knees because the guns were so big and heavy for the size of the hull every bit of support would be needed to prevent the guns from ripping apart the structure.
The knees provided are over size and this was done on purpose because when a builder sets up the beams they may or may not be exactly in the right place. The knees is a fussy job of fitting them between the beams. So relax and take your time.
installing the knees
Ships built on the lakes in North America from the study of various ship wrecks show hanging knees were not used when building a deck. Lodging knees were used in most cases but not in every case. a system was used where the ends of the deck beams were set in a shallow notch in the deck clamp and a heavy waterway timber was place on top of the beam.
For the Caustic i did use lodging knees because the guns were so big and heavy for the size of the hull every bit of support would be needed to prevent the guns from ripping apart the structure.
The knees provided are over size and this was done on purpose because when a builder sets up the beams they may or may not be exactly in the right place. The knees is a fussy job of fitting them between the beams. So relax and take your time.