I am working on a redesign of one of my frame sets and thought you might all get a kick out of a new approach I am taking.
In this design, the shape is created in a dedicated software that works well with organic shapes and then that part is inserted in one of the "usual suspects" for CAD for manufacturing.
But that is not important. What is fun is the resulting details that I have been able to introduce to contemporary kit design.
In this case, I have done the following:
- doubled the number of frames that were in the original drawing. Remember, since I am working off of a 3D hull shape, I can add bulkheads wherever I want, and in any orientation.
- opened up the cockpit area in preparation for including seats, fixed and 3D-printed, as part of the kit
- added stringers to give the model builder a more accurate, and enjoyable, build.
This is an ongoing project. I will add a few more pictures later, as I get closer to cutting the parts.
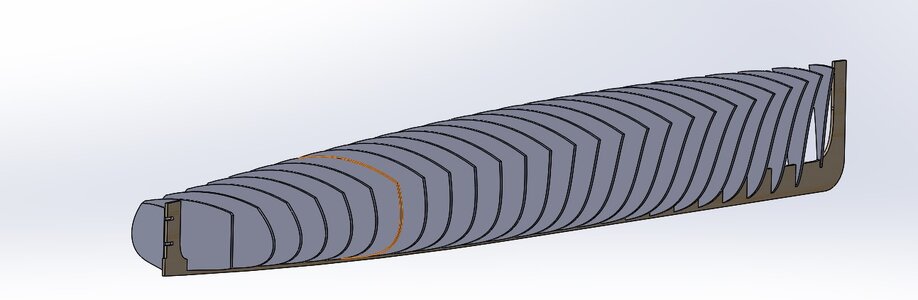
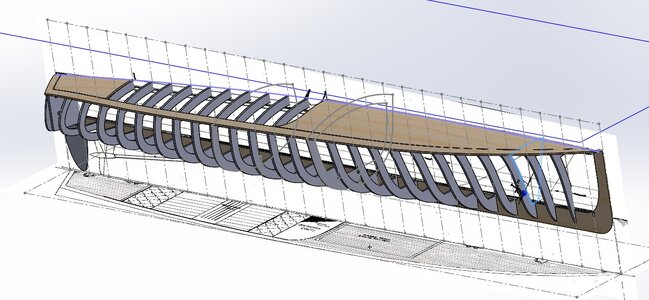
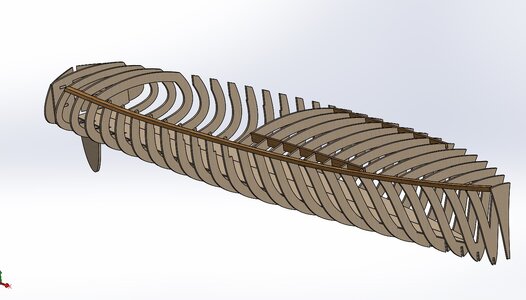
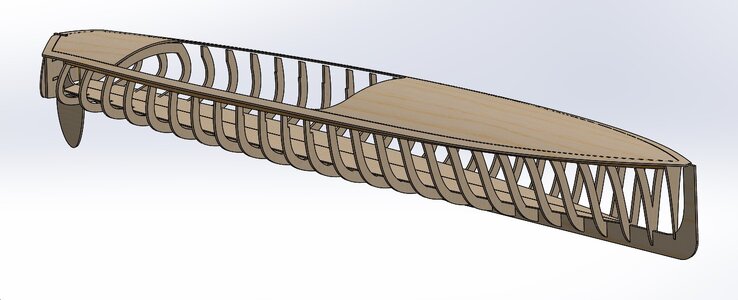
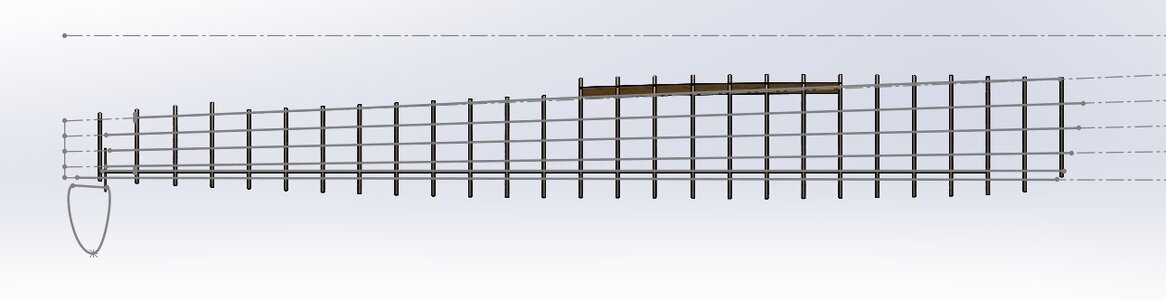
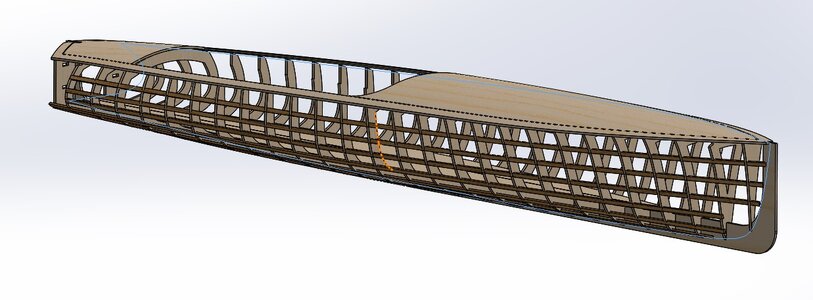
In this design, the shape is created in a dedicated software that works well with organic shapes and then that part is inserted in one of the "usual suspects" for CAD for manufacturing.
But that is not important. What is fun is the resulting details that I have been able to introduce to contemporary kit design.
In this case, I have done the following:
- doubled the number of frames that were in the original drawing. Remember, since I am working off of a 3D hull shape, I can add bulkheads wherever I want, and in any orientation.
- opened up the cockpit area in preparation for including seats, fixed and 3D-printed, as part of the kit
- added stringers to give the model builder a more accurate, and enjoyable, build.
This is an ongoing project. I will add a few more pictures later, as I get closer to cutting the parts.
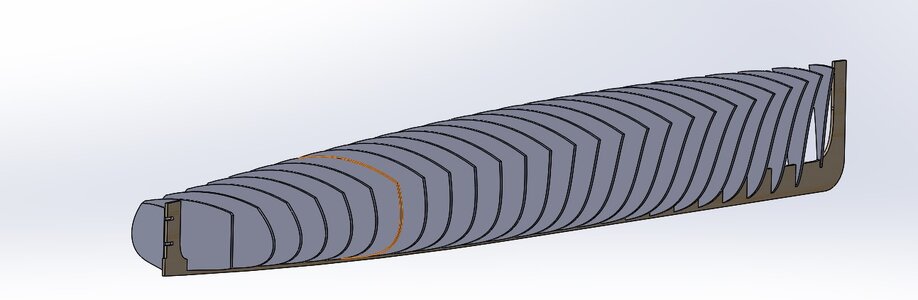
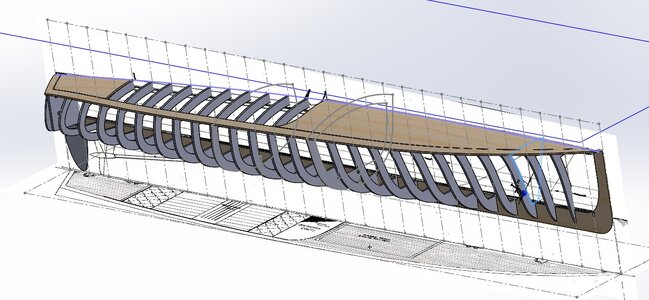
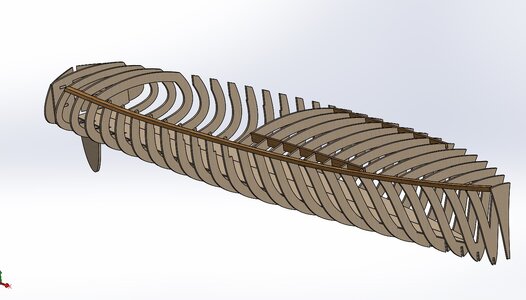
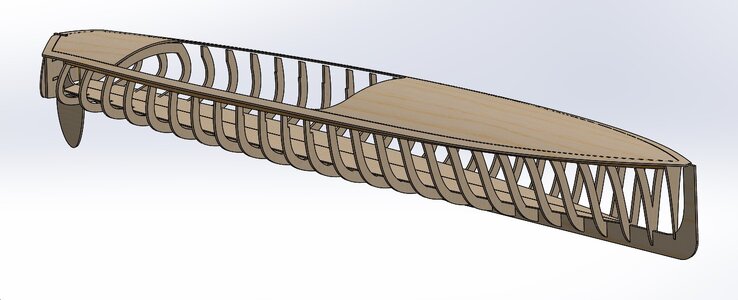
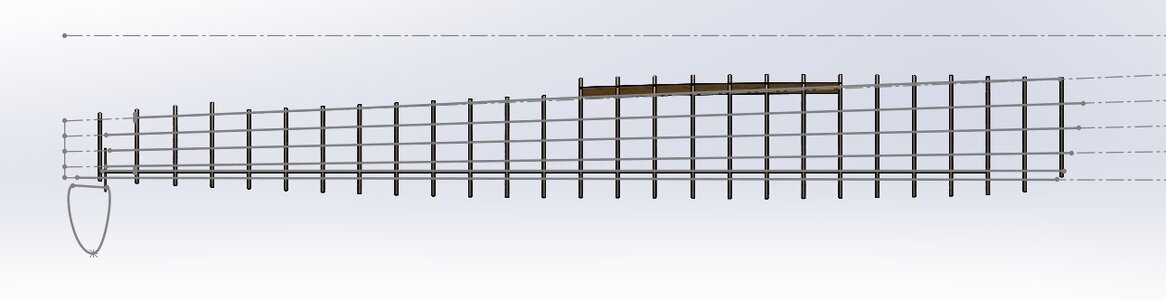
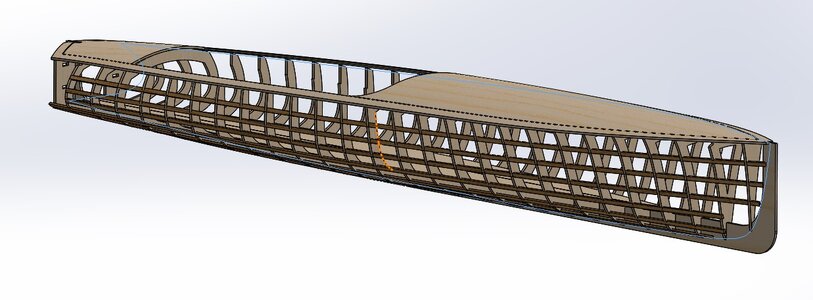