Recently I finished the Mini CNC Mill which about which I posted some photos of the progress..
At the time I was just starting the standing rigging on the Mamoli Constitiution, and not happy with my first build efforts. Mainly with the seizing. I was making my own ropes and they were going quite acceptably, but the seizing was another matter.
Incidentally, I plan to use the mini mill to make the spars. I will post results soon.
Then I had a thought. I know that some modellers use a hand cranked apparatus to do the serving, and I wondered if I could make a CNC machine to achieve better results than I could manage using simpler traditional methods.
The electronics and MPG from the mill could be easily swapped over to operate the CNC serving machine.
So, after playing around with designs, and getting some useful advice from this site, I came up with a plan. Ordered various components, and waited for them to arrive before finalising the plans.
Some components were 3D printed, and some were machined. Many were purchased from China.
The mechanical parts of the machine are shown in the following photos. 800mm between centres. Nema 17 steppers. Electronics-Control box not shown here. See CNC Mini Mill thread.
When I have tested it, and made any adjustments I will show a video.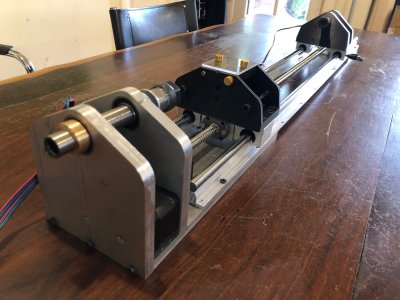
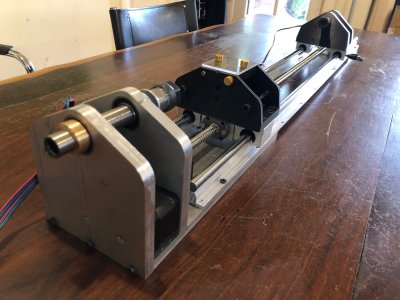
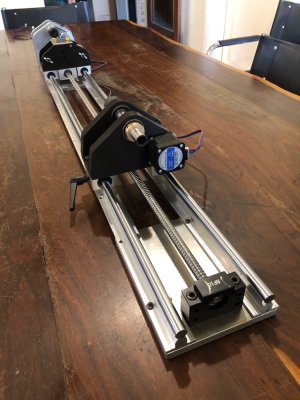
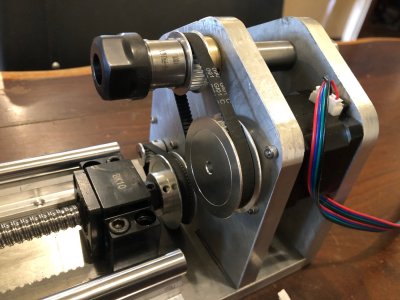
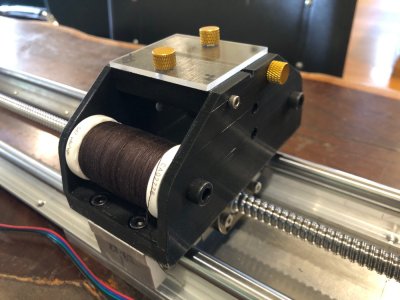
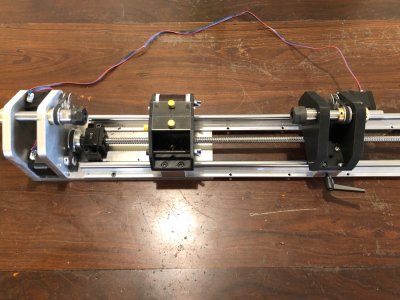
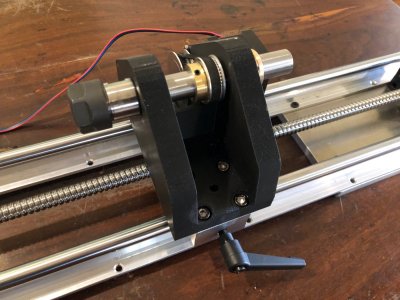
At the time I was just starting the standing rigging on the Mamoli Constitiution, and not happy with my first build efforts. Mainly with the seizing. I was making my own ropes and they were going quite acceptably, but the seizing was another matter.
Incidentally, I plan to use the mini mill to make the spars. I will post results soon.
Then I had a thought. I know that some modellers use a hand cranked apparatus to do the serving, and I wondered if I could make a CNC machine to achieve better results than I could manage using simpler traditional methods.
The electronics and MPG from the mill could be easily swapped over to operate the CNC serving machine.
So, after playing around with designs, and getting some useful advice from this site, I came up with a plan. Ordered various components, and waited for them to arrive before finalising the plans.
Some components were 3D printed, and some were machined. Many were purchased from China.
The mechanical parts of the machine are shown in the following photos. 800mm between centres. Nema 17 steppers. Electronics-Control box not shown here. See CNC Mini Mill thread.
When I have tested it, and made any adjustments I will show a video.
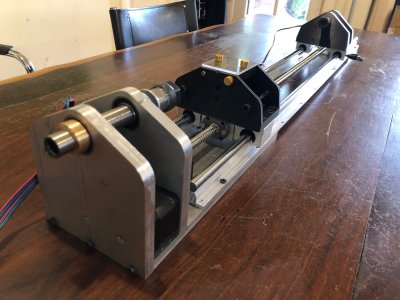
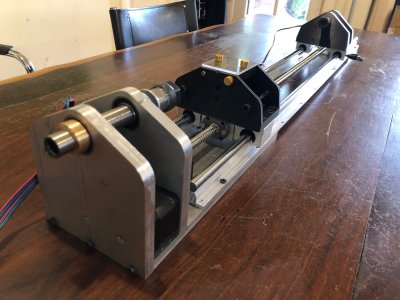
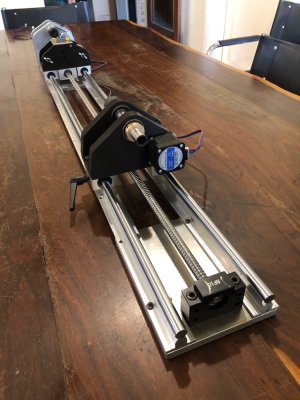
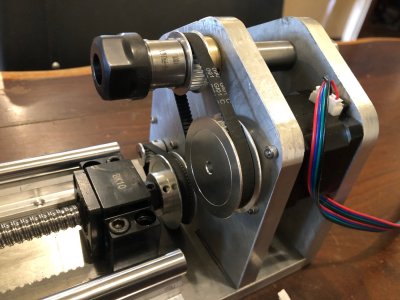
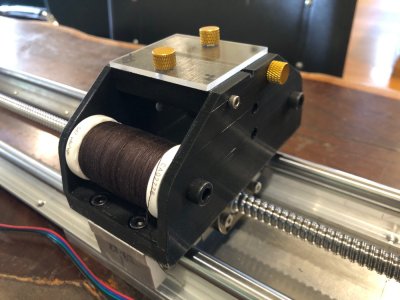
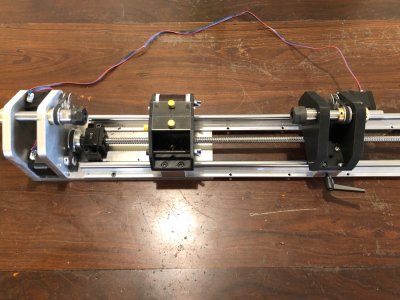
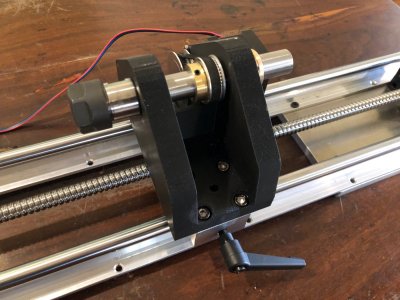