- Joined
- Oct 1, 2023
- Messages
- 1,557
- Points
- 488
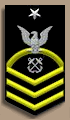
On a double planked hull is it customary to install the second layer of planking on areas that get copper plating?
**VIEW THREAD HERE** |
On a double planked hull is it customary to install the second layer of planking on areas that get copper plating?
is it customary to install the second layer of planking on areas that get copper plating?
LOL... My bad. I meant "yes" and, thinking "Don't do it!" Wrote "no." Edited the original post to correct the error. Sorry about that!Hi Bob.
The question was
Not sure how direct reply to this question can be “no” when you actually confirm that the answer is “yes” in remainder of your answer
That's what I was thinking. My copper plates are the same thickness as the second layer planks.While I'm not a fan of "double planking" on POB hulls, the direct answer to the question is "yes." If the second layer of planking is omitted beneath the waterline where the copper sheathing will be installed, the hull will be one planking thickness too small where the copper covers.
ThanksYes, it is.
Whoa! Wait a minute. What Roger said above is spot on. I had no idea your copper plating was as thick as the second layer of planking!That's what I was thinking. My copper plates are the same thickness as the second layer planks.
A quick 2 cents - scale viewing distance aside, we are, in some part making art here given the impossibility of pure historical accuracy for most builds. The copper sheathing can look very nifty and, depending on your kit's copper (hopefully rolls of tape with good adhesive) you should go for it. It will never be a Kandinsky (one hopes), but the Platonic ideal of a ship is also a beautiful thing to behold. BTW Blue Jacket Shipcraters carries lovely copper tape - super thin. Below it is applied on top and, IMHO, the is no visual "step" between the painted hull and the sheathing even at actual viewing distance. If your scale is small - omit the rivets, makes it too busy, again IMHO.
You speak the truth. There is as much gratification in finding how things were actually done on a ship as there is in applying those methods in the build itself.doing the research" is as much, if not more, satisfying than the building of the model itself.
It looks like I need to make two mockups to compareIt’s a question of scale. First of all this is copper sheathing not plating. It was quite thin the heaviest copper used by the RN was 32 oz per sq ft; about .05in thick if your scale is 1:50 the scale thickness of your copper sheathing should be .001in. This is so thin that the naked eye would have trouble seeing the “step” between the planking and the sheathing.
So, how thick is your veneer? If as you say the copper that you are using is as thick as the veneer, I see no reason to plank the area being sheathed. Adding this thick copper over the second layer of planking would look overscale.
Roger
Your correct it will be out of scale. I still want to do it just for fun. Even my best work would be considered impressionistic by most.Whoa! Wait a minute. What Roger said above is spot on. I had no idea your copper plating was as thick as the second layer of planking!
You've either got extremely thin second layer planks or extremely thick copper plates! Therefore, as Roger explained, if you attached your copper sheathing on the first layer of planking, it would seem that it would result in a very close to scale appearance. If you laid hung your second layer of planking to the keel rabbet and then applied your thick copper sheathing, the sheathing would be way out of scale.
As a matter of fact, at most scale viewing distances, the detail appearance of copper sheathing is nearly invisible and it's only the color that is perceived. Assuming a fully planked hull, copper sheathing material should be a very thin copper foil. According to Roger's math, in real life it would be .05". That makes it .001" thick at 1:50 or 1:48 scale (quarter inch to the foot.) It would be .0005" at 1:96 scale (eighth inch to the foot.)
In terms of 1:48 scale, the .001" scale thickness of copper sheathing, is about one thirtieth the thickness of a credit card. Coincidentally, the industry standard for the thickness of a single coat of paint is going to be between .001" and .002". So, why not paint the sheathing instead of spending hours and hours trying to get bits of copper leaf to stick in the right place? This is what a real copper sheathed hull looks like at something like "scale viewing distance:"
View attachment 503723
USS Constitution copper plate:
View attachment 503726
View attachment 503725
HMS Victory copper sheathing plate.
View attachment 503724
With some colors applied over a base coat with a sponge, airbrush, or combination thereof, a very realistic appearing faux copper bottom is easily achieved.
Despite the incredible amount of obvious work and craftsmanship no ship ever looked like this:
View attachment 503727
View attachment 503728
All of the opinions expressed here assume that the reader is seeking to create a compellingly accurate portrayal of a ship in miniature. If the reader has no interest in historical accuracy or compelling realism and perhaps is more of an impressionist than a realist, they are always free to let their creativity run wild. I have a framed print of Wassily Kandinsky's' Inmprovisation 31 (Sea Battle) on my wall:
View attachment 503730
I enjoy it as much as I do the same sea battle subject by Willem van de Velde, the Younger, An English Ship in Action with Barbary Vessels:
View attachment 503729
It's all a matter of style.
I certainly respect your approach. I'm still new to ship modeling and learning the skills and techniques necessary to replicate the details available in the kit.No question that a neatly done coppering job can look nifty on a model entirely separate and apart from what the real prototype vessel looked like, as your picture attests. As you note, the correct copper foil is a prerequisite. (I've always found Bluejacket Shipcrafters' products to be of the highest quality.) If the modeler finds the result satisfying, it's worth the effort. The exercise is, first and foremost, essentially the sole and somewhat private pursuit of personal satisfaction. That said, the question becomes: Against what standard does one judge their work?
My modeling experience parallels my experience working on traditionally built prototype vessels, so my benchmark has always been the exact historically accurate prototype. This isn't to say I've always attained that goal and certainly not in my early years. Nor have I expected others to do so. Frequently in the case of period models, there simply isn't any historical record upon which to rely and where there is, gaps almost always exist in one detail or another which must be filled with data extrapolated from elsewhere. However, this is quite a different matter than the case of subjects of which no historical record exists whatsoever. In this latter instance, a Santa Maria, Mayflower, Golden Hind, or just about anything built prior to the Eighteenth Century cannot be properly called a model of a named vessel at all. At best, it's only a three-dimensional expression of someone's fantasy which, were it to be identified as a generic type of vessel, would be potentially of greater historical value, all else considered.
I suppose the easiest way to express my own personal standard is to describe it as coming as close as I possibly can to creating a representation that creates in miniature my own experience of what that vessel looked like were I to be able to walk her decks and sail her myself in real life. That's just me. Other's mileage varies, I know. Being a lifelong mariner in one form or another, there is little left to my imagination in such details, and I've always tried to bring that experience to the models I build. For me, it's inescapable, really. My modeling has always been an exercise in continually trying to better my "personal best." I find inaccurate details distracting because I instinctively know none were ever to be found on a prototype vessel. Among these and currently in vogue are improperly placed and contrasting trunnels and fastening plugs (which make a deck as distracting as pretty woman with too many tattoos,) out of scale copper sheathing (the sort with "rivets" that never existed instead of the copper tacks that are invisible at common scale viewing distances,) and light-colored deadeyes and lanyards (where this currently popular affectation came from, I have no idea.) That isn't to say that they are not "nifty" or visually attractive to many modelers and kit manufacturers and if someone enjoys them there's always value in that. Indeed, some of the finest entirely accurate builder's yard "board room" models are done only in bright woods and polished metals solely for artistic effect.
View attachment 503736
View attachment 503737
View attachment 503740
(Builder's model of a cargo ship. Sold for ~$82,000.)
Also, in the "I know, it's just me" category, I find obvious errors of historical accuracy beyond simply distracting. Among these are anachronistic details, such as the wrong anchor design, which is one common example resulting from kit manufacturers cutting corners by using the same fittings on a number of models. These faux pas can be avoided by diligent research, but if one is averse to doing the research necessary and instead expects a kit manufacturer to do it for them, they are the price one pays, which, I know, for some, if not many, is a fair exchange. That notwithstanding, I still cringe when I hear someone say that they build kits because they don't want to be bothered doing the research necessary to build a model from scratch. For some of us, "doing the research" is as much, if not more, satisfying than the building of the model itself.
Very nice model. Here's the plating I have to work with. Probably on the low end of the scale when considering historical accuracyA quick 2 cents - scale viewing distance aside, we are, in some part making art here given the impossibility of pure historical accuracy for most builds. The copper sheathing can look very nifty and, depending on your kit's copper (hopefully rolls of tape with good adhesive) you should go for it. It will never be a Kandinsky (one hopes), but the Platonic ideal of a ship is also a beautiful thing to behold. BTW Blue Jacket Shipcraters carries lovely copper tape - super thin. Below it is applied on top and, IMHO, the is no visual "step" between the painted hull and the sheathing even at actual viewing distance. If your scale is small - omit the rivets, makes it too busy, again IMHO.
Blessings. Peace. Gratitude.
Chuck
View attachment 503734View attachment 503735
Ted! Thank you for the compliment. Also, thank you for sharing this pic. I don't recall whether you shared the scale of your model, but, if it was me, I'd skip the simulated nail heads. I've yet to see a build where that added to the ship. Just a personal opinion. Even in the very precisely executed coppering in Bob Cleeks example, the copper plates look very meaty and overstated.Very nice model. Here's the plating I have to work with. Probably on the low end of the scale when considering historical accuracyView attachment 503753
Thanks for the advice. I'll check Bluejacket todayTed! Thank you for the compliment. Also, thank you for sharing this pic. I don't recall whether you shared the scale of your model, but, if it was me, I'd skip the simulated nail heads. I've yet to see a build where that added to the ship. Just a personal opinion. Even in the very precisely executed coppering in Bob Cleeks example, the copper plates look very meaty and overstated.
As far as how you judge the outcome of your effort, remember it's your kit, your time and it should look how you want it to look in the end even if you have to tear things off and do-over, do-over, do-over. I agree with the proposition that independent research is part of the fun, interesting and rewarding in its own right. My model is of Harriet Lane. She's actually one of the famous ships of the Civil War. I didn't know it at the time, but the kit design is absolutely wrong in certain important aspects when compared to the original plans. Over the course of the build, one of our helpful shipmates on this forum put me on to the existence of the original William Webb plans. Google allowed me to locate the plans which I had enlarged at Kinkos. She's a much finer model now, IMHO, because of the research even though I was late finding some of it. In the end, part of my standard for the outcome is whether I achieved a better model than my last one - including all of the additional detail, historically accurate detail mind you, that I had the time, skill, dollars and interest to show in the final project. I won't pretend to model at the level of some of our shipmates on the forum. They set wonderful examples and inspire me to go for it. So, go for it, shipmate!
BTW, last piece of unsolicited advice, get the Blue Jacket tape - they sell several widths - and cut the plates by hand. It takes a while, but the process is lovely and if you hate it or make a mistake, the plates can be easily scraped off without damage to the underlying hull.
Good luck!
Blessings. Peace. Gratitude.
Chuck
Thanks for the advice. I'll check Bluejacket today
Ted! How do those measurements match with the standard copper panel of 18" x 48"? (That's right isn't it? Not 12" x 48"?) I was lucky that Blue Jacket had 3/16" wide tape for my 1:96 scale ship. so I had my 18 inches in width and only needed half-inch long "plates" to have the proper length.This model is 1:64 scale.
I got two copper plates out and measured them at 0.23 x 5.63 x 18.46 mm.
The previous one measured at 0.5mm thickness was an anomaly. That answers the question of copper as a third level after the two planking levels.
I'm questioning whether or not to even install it. On one hand it looks like it could be fun. On the other it looks like it could be a nightmare and possibly detract from the model. For some reason I just an not attached to this build and find myself looking forward to my next model. The one I have in mind doesn't have copper plates. I seriously have my doubts I will be in any condition to build another at that point. Who knows, God bless us all