I’ve got a stern piece that requires a groove as indicated by the yellow marker. What’s the best way of going about carving/cutting a smooth even groove, (semicircular?) between the lines as shown by the yellow highlighter?
I have tried once and used a carving chisel but got a very uneven surface, irregular outline and sanding did not seem to help?
Possibly using a scalpel first along the outline?, using a drill bit with a rounded end? Suggestions would be grateful.
I am a complete novice when it comes to carving.
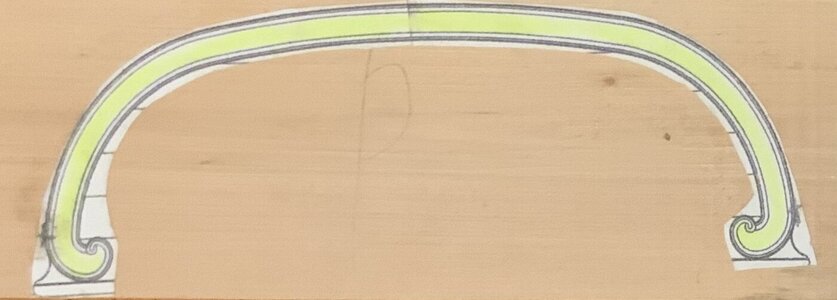
I have tried once and used a carving chisel but got a very uneven surface, irregular outline and sanding did not seem to help?
Possibly using a scalpel first along the outline?, using a drill bit with a rounded end? Suggestions would be grateful.
I am a complete novice when it comes to carving.
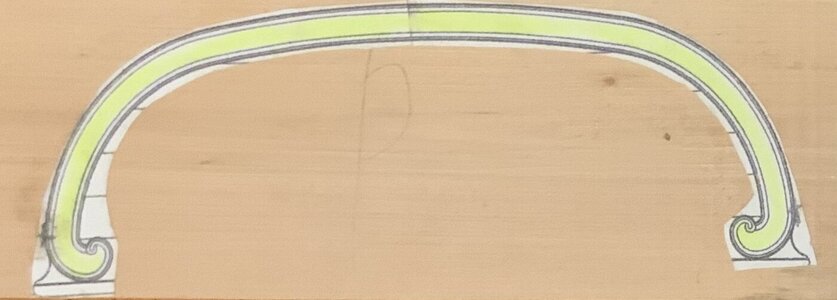