I have some molds used to create the carvings on a ship model (SOS), these were called craft mats and were made in the early 1930"s. They intended on people using a plastic wood to mold the carvings.
I am restoring my grandfather's model, the carvings were never added. The molds create a rounded casting, so I wanted to create a copy of the mold, use a rotary tool to square up the rounded edges in the new mold.
It's not clear to me how to make the copy of the mold, the casting examples I see are copying parts already made. Does anyone have suggestions on which casting materials to use ?
Regards,
Bob.
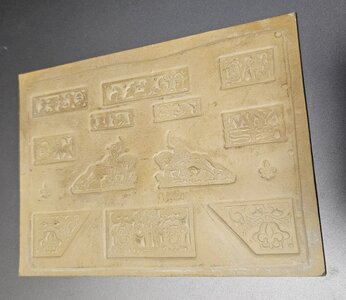
I am restoring my grandfather's model, the carvings were never added. The molds create a rounded casting, so I wanted to create a copy of the mold, use a rotary tool to square up the rounded edges in the new mold.
It's not clear to me how to make the copy of the mold, the casting examples I see are copying parts already made. Does anyone have suggestions on which casting materials to use ?
Regards,
Bob.
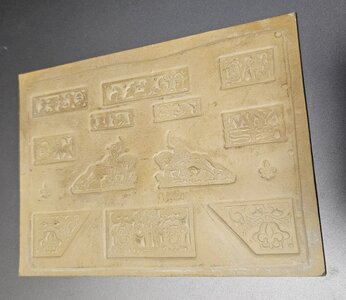