Bolton Part seven
This is where I deviate from normal practice and go my own way using what I have learned from the day job.
The valve chests are traditionally machined on the lathe using an elaborate system of faceplate with angle block attached so the valve rod passages can be drilled through top and bottom faces insuring alignment.
Given there is not a blind hole on this engine at the top of each chest as in most Stuart Engines I plan to do most of the work on the mill and use datum faces. An edge finder and the DRO will be used to drill these important holes.
The first step is to take the valve chests to thickness and square top and bottom faces to the same height as the block. The boss for the Valve rod gland is left untouched for now. This will be turned in the lathe in the 4 Jaw chuck as the last operation with the hole used for reference to centre it.
The intermediate Steam valve chest is tapered so this causes an issue as the is no accurate datum face. I have glued a piece of Aluminium to the side of this chest using JB weld. This chest will then be machined as the previous one but I will end up with a square face on the side to reference the edge finder. This aluminium piece will be machined off when the assembled block has it's taper machined.
As a side note, following John's advice, I have ordered a book on this build, some additional drawings along with Bolton's Original drawings for this engine from E and J Winter in NSW, OZ. Postage was quite reasonable and hopefully should land between 6 and 21 working days.
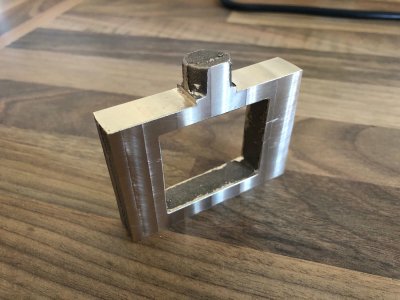
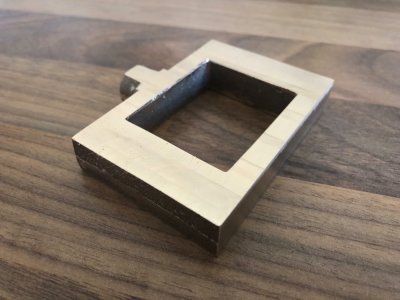
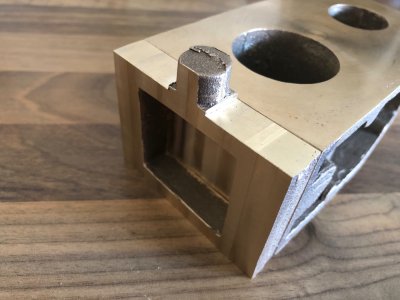
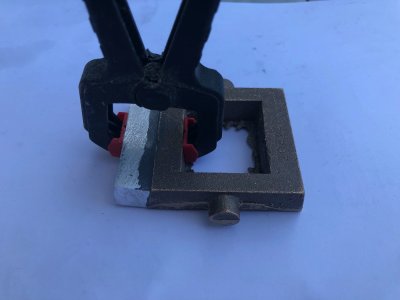