HATCH COAMINGS
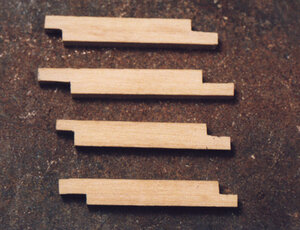
Hatch coamings, companion ways, skylights and other deck openings are all built the same way. The corners of the coamings are fitted together with a lap joint and not with a 45 degree angle like picture frames. The lap joint when fitted has a pin that runs through each coaming and into the beam below it. The lap can be cut at random; the extra length is trimmed after the coaming is assembled.
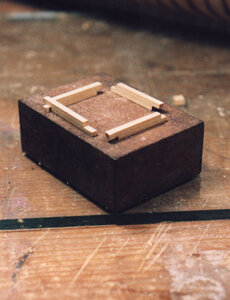
After the pieces are cut assembly is set up so each side has an under lap and an overlap.
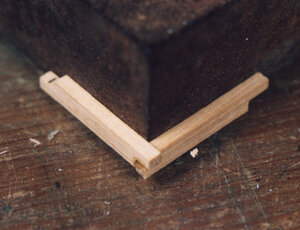
Two sides are glued by placing them against the corner of a square block. Another two sides are set up in the same way.
The two assembled corners are now glued together to form the coaming. The extra over lap at the corner is trimmed even.
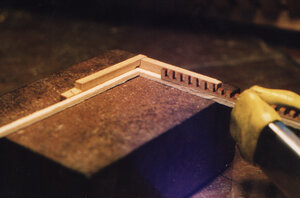
When gratings are used in the coaming a small ledge is added to the inside of the coaming. The added ledge is not all that necessary and the gratings can be glued directly to the inside of the coaming.
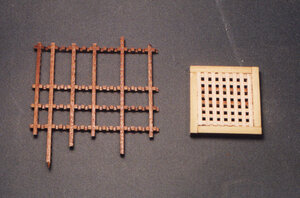
The gratings can be made on a small table saw by following a variety of published methods. When setting up the grating start with an outer square and add strips in both directions. It is easy to get the gratings out of square by starting in one direction. By building the gratings by skipping strips enables you to push on opposite corners to keep it square.
SKYLIGHT
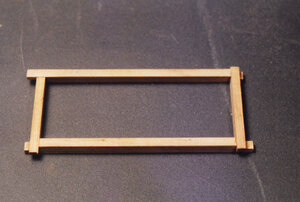
The skylight is set on a coaming. This is built the same way any of the hatch coamings are built. Once the coaming is assembled the corners will be trimmed even.
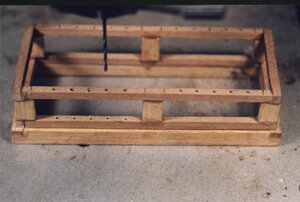
By using the same material used for the ledges a frame work is built on the coaming. A wider material is used for the short up rights. In actual building they would have been attached to the lower and upper frame with a mortise and tenion, on the model they are glued in place. Next an upper frame is set in place. Once the frame is built holes are drilled through the upper frame and into the lower. Protective bars are run into the holes. The bars themselves are made from .025 styrene plastic rod bought at a local hobby shop. The rods are white in color so they were painted black before being installed. No glue was used to set the bars in place.
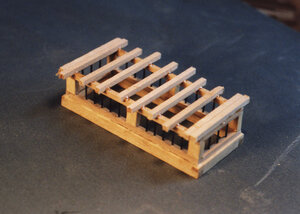
With the bars in place beams are set across the frame work. Doubles are set at each end so the ends of the roof planking will have something to nail to. I didn’t bother to cut the beams to exact lengths. I cut them close and glued them in place.
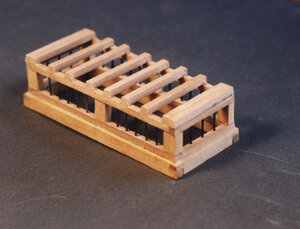
After the epoxy sets up the ends of the beams are sanded flush with the sides of the frame work.
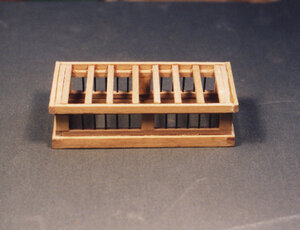
A molding is fixed to the side of the framework to box in the ends of the roof beams. This molding is the width of the roof beam plus half of the top frame. Once in place it will make the structure water tight.
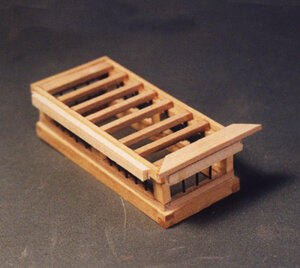
A scrap of wood is added to the side of the framework with two sided tape. This is used as a guild to set the over hang of the edging plank. The edge plank is ¼ wide and 1/16 thick. This is one of the rare areas where a 45 degree joint is used. The end grain of wood tends to absorb water faster than the rest of the plank. Before the joint is set, caulking is used on the face of the 45 degree edge.
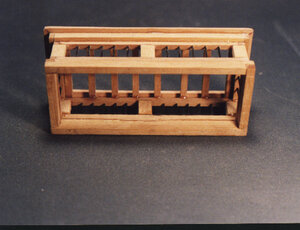
Here the skylight is tipped on its side so you can see the molding and the over hang of the edge plank. At this stage you can add glass to the windows, one suggestion is to use the clear plastic many products are packaged in.
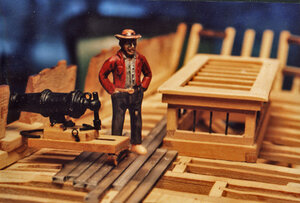
Here the skylight is in place on deck. The decking is an experiment in using a clear plastic planking. There is so much fine joinery in the deck structure I didn’t want to cover it. To put the carronades on the model some sort of decking is needed. Planks were cut from plastic and run through the sander to score the surface so it looked like a grain pattern. The edges were painted black to simulate caulking. The plastic was clear enough you could see the deck structure below it The entire skylight was built off the model. In reality the coaming would be set in place on the beams then iron pins run through the corners and into the beams. The coamings are also pinned to the carlings. Then the rest of the structure is built on the coaming.