Hello. My name is Henry (aka Zzyzx01) and welcome to my build log of the Polaris by Occre. This is my first build log as well as my first attempt to build a plank-on-bulkhead (POB) model so bear with me on both accounts. Please note that I am not a fast builder as I have other obligations as I am sure many of you do as well. My goal for this build is to learn and improve my skill sets and techniques which I can apply to future builds. At this time, I'm not interested in historical accuracy, per se. Perhaps as I refine my skills, I can put more attention to accuracy. In the mean time, I welcome all suggestions, recommendations, and critiques throughout this build.
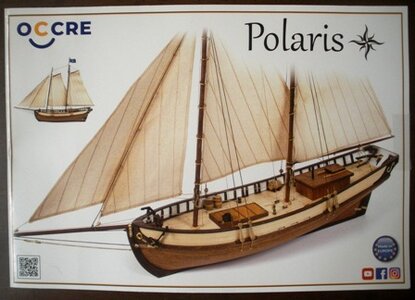
When I began building the Polaris, I was not planning on creating a log; therefore, I do not have photos of the unboxing of the kit (but such is available in other Polaris build logs found here on the SoS website). The kit was inventoried and found to be complete. Small parts were contained in a plastic compartment box. The lumber materials were grouped into sizes. The laser cut pieces were identified and marked according to their part numbers. The write-up for the plans is somewhat limited, but the pictorial images of the build process are very thorough. There is a companion You Tube video that takes the builder through the assembly process. All in all, I felt very comfortable engaging in the project.
I also do not have photos showing the bulkhead to keel assembly, nor the process of the deck planking and bulwarks installation. The following couple of installments will be a narrative without photos. Subsequent log postings will have photos.
Bulkheads -
After labeling each of the 11 bulkheads, the assembly to the keel was fairly straight forward just making sure that they were perpendicular to the keel. Once the bulkheads were glued in with white PVA, I went back with a syringe filled with glue (PVA) to strengthen all the joints.
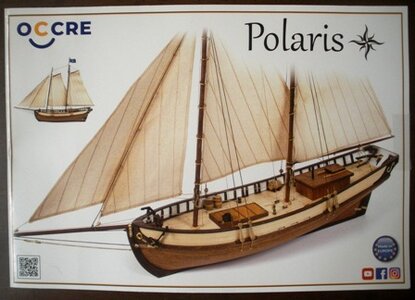
When I began building the Polaris, I was not planning on creating a log; therefore, I do not have photos of the unboxing of the kit (but such is available in other Polaris build logs found here on the SoS website). The kit was inventoried and found to be complete. Small parts were contained in a plastic compartment box. The lumber materials were grouped into sizes. The laser cut pieces were identified and marked according to their part numbers. The write-up for the plans is somewhat limited, but the pictorial images of the build process are very thorough. There is a companion You Tube video that takes the builder through the assembly process. All in all, I felt very comfortable engaging in the project.
I also do not have photos showing the bulkhead to keel assembly, nor the process of the deck planking and bulwarks installation. The following couple of installments will be a narrative without photos. Subsequent log postings will have photos.
Bulkheads -
After labeling each of the 11 bulkheads, the assembly to the keel was fairly straight forward just making sure that they were perpendicular to the keel. Once the bulkheads were glued in with white PVA, I went back with a syringe filled with glue (PVA) to strengthen all the joints.
Last edited: