- Joined
- Apr 20, 2020
- Messages
- 5,650
- Points
- 738
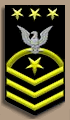
Dear Friends
I would like to share with you a project that ended today and I worked on it with a good friend of mine who is an expert in machines:
a self-made drum sander for fine sanding of wood to thin thicknesses. The need for such a sander has risen in the last year due to Proxxon's thicknesser DH 40, which isn't suitable for fine sanding of wood with small thicknesses of 2-0.5 mm (leaves marks on the wood).
In the last year, some of you shared here the self-production of sanders and I also saw a sander that our friend stuglo made in his home.
These sanders inspired the sander we produced.
In fact, I took a lathe that I bought about two years ago and which did not meet my expectations and based on it we built the sanding machine. We left the motor, added a standard sanding drum that is sold on many websites.
we made the inclined/angled base, on which the wooden board rests and which moves on a pivot base back and forth. The dimensions of the machine are 46 cm long, 8 cm wide and 16 cm mandatory.
Today I did my first significant job with the sander past the Alert model, and I am satisfied with the results.
I will attach photos and a video for you.
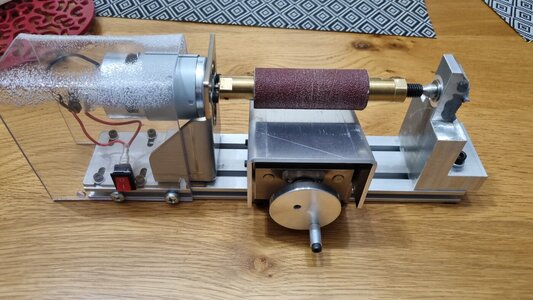
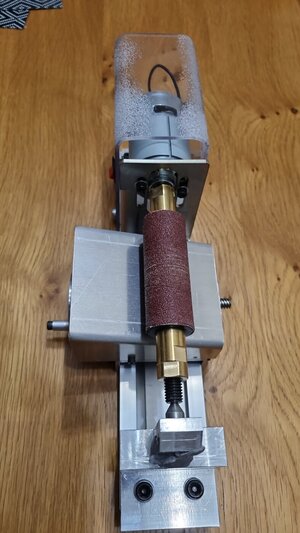
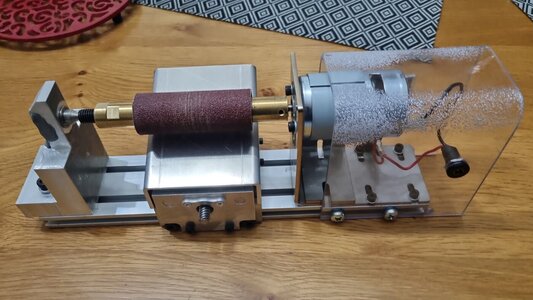
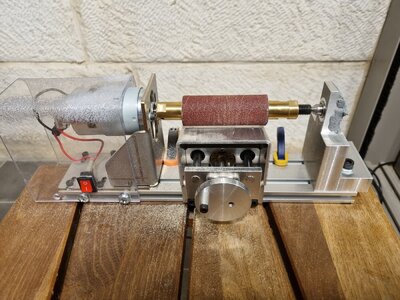
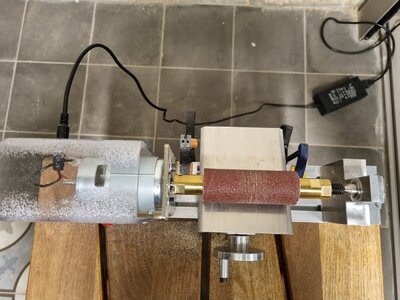
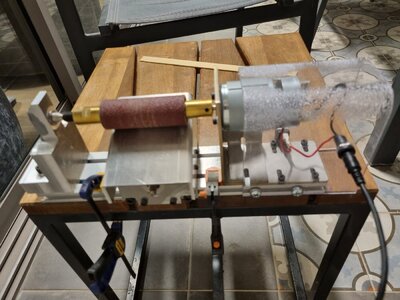
View attachment 20221113_204451.mp4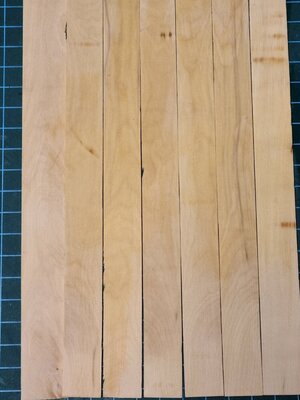
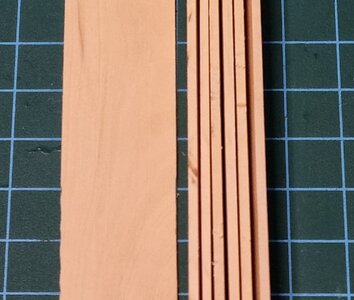
I would like to share with you a project that ended today and I worked on it with a good friend of mine who is an expert in machines:
a self-made drum sander for fine sanding of wood to thin thicknesses. The need for such a sander has risen in the last year due to Proxxon's thicknesser DH 40, which isn't suitable for fine sanding of wood with small thicknesses of 2-0.5 mm (leaves marks on the wood).
In the last year, some of you shared here the self-production of sanders and I also saw a sander that our friend stuglo made in his home.
These sanders inspired the sander we produced.
In fact, I took a lathe that I bought about two years ago and which did not meet my expectations and based on it we built the sanding machine. We left the motor, added a standard sanding drum that is sold on many websites.
we made the inclined/angled base, on which the wooden board rests and which moves on a pivot base back and forth. The dimensions of the machine are 46 cm long, 8 cm wide and 16 cm mandatory.
Today I did my first significant job with the sander past the Alert model, and I am satisfied with the results.
I will attach photos and a video for you.
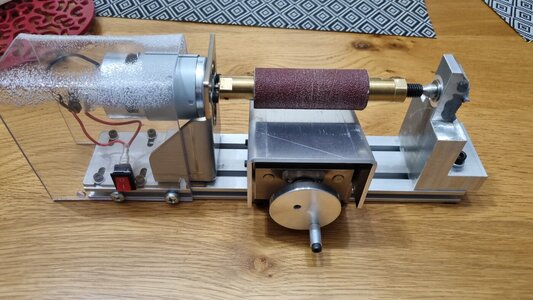
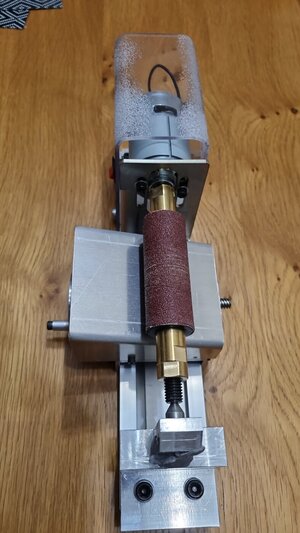
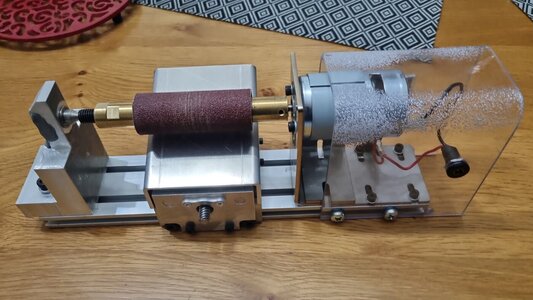
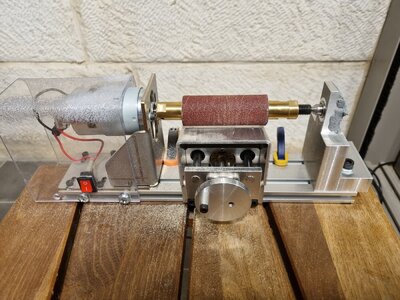
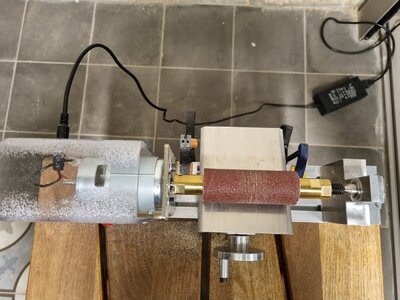
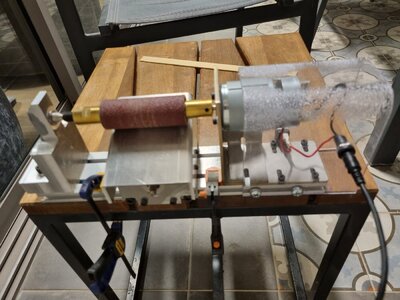
View attachment 20221113_204451.mp4
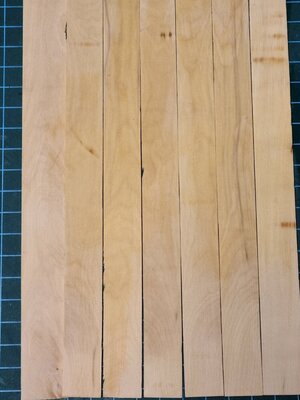
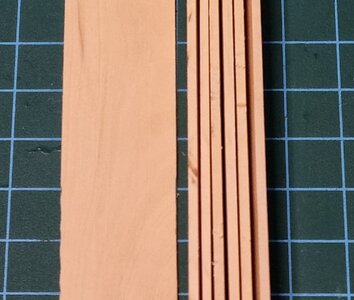