- Joined
- Dec 17, 2024
- Messages
- 52
- Points
- 78

This will be a build log for a scratch build of a live-steam driven R/C model of the steel tugboat Edna G, commisioned by the Duluth & Iron Range railroad for service at their ore docks in Two Harbors, MN.
Starting from lines and drawings from the builder, Cleveland Shipbuilding, from 1895-1896 but aided by measurements and historic/current photos- she still floats in Two Harbors as a museum ship!
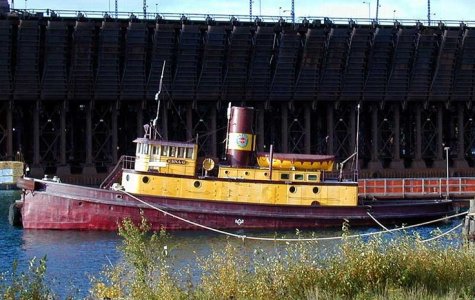

Starting from lines and drawings from the builder, Cleveland Shipbuilding, from 1895-1896 but aided by measurements and historic/current photos- she still floats in Two Harbors as a museum ship!
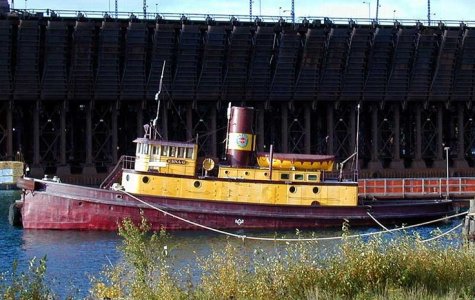
