- Joined
- Feb 18, 2019
- Messages
- 712
- Points
- 353
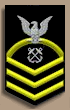
This canoe will be the one listed as the 17" model.
It will be built from milled Pear wood supplied by bibigon (Sergey)as mentioned here: https://shipsofscale.com/sosforums/...to-purchase-plans-materials.5302/#post-107811
Lumber alternative B in the lumber options available for this project .
Everything will be done following the construction guide and I will opt for the couple of upgrades: simulated fastenings and woven seats. Fastening is detailed in the manual: it is quite tedious but will get through it.
G
It will be built from milled Pear wood supplied by bibigon (Sergey)as mentioned here: https://shipsofscale.com/sosforums/...to-purchase-plans-materials.5302/#post-107811
Lumber alternative B in the lumber options available for this project .
Everything will be done following the construction guide and I will opt for the couple of upgrades: simulated fastenings and woven seats. Fastening is detailed in the manual: it is quite tedious but will get through it.
G