Salve a tutti i modellisti!
Continuo ad illustrare le fasi di montaggio.
Ho proceduto da autodidatta ma ho seguito molti consigli utili.
In alcuni casi, la soluzione che ho adotatto, per uno specifico problema, non era forse la migliore.
Non abbiate timore di commentare negativamente alcune scelte.
Se, però, qualche scelta tecnica, un pò fuori standard, potrà essere utile agli altri sarò veramente contento.
Dunque, dopo aver aperto gli spazi interni dello scafo, bisognava introdurre con criterio: motore, servomeccanismi, ricevente, variatore di tensione e batterie.
Già nel progetto, la loro collocazione era più in basso possibile.
Tuttavia prima di questo ho pensato alla trasmissione motore - elica.
Ci sono in commercio astucci per assi dell'elica già completi in acciaio, ma io ho preferito farlo da solo perchè non erano della lunghezza giusta.
In queste immagini allegate, potete vedere alcune fasi di assemblaggio.
L'asse è un tondino pieno di ottone che ho filettato io. Il suo diametro è 4 mm.
I microcuscinetti hanno un diametro interno di 4 mm e un diametro esterno di 8 mm.
L'astuccio esterno è costituito da un cilindro di alluminio del diametro interno di 8 mm e di diametro esterno di 10 mm.
I distanziatori interni, che separano i cuscinetti, sono tubi di ottone del diametro esterno di 8 mm.
Il tubo di alluminio ha dei tubicini per l'inserimento dall'esterno del grasso.
Tutto pieno di grasso siliconico, è molto difficile che l'acqua arrivi ai cuscinetti, tanto meno all'interno della stiva.
Ad differenza di quasi tutti gli altri elementi, il tubo di trasmissione non è amovibile, esso è saldamente bloccato sul fondo dello scafo, immerso nella resina.
E' perfettamente in asse con il motore ed è ad esso collegato con un giunto normale (non un giunto cardanico). Inoltre, è parallelo al deck e alla chiglia. In questo modo tutta la spinta è utile e non ci sono componenti verticali che vanno sprecate, come nel caso di un asse leggermente obbliquo.
Hello all modelers!
I continue to illustrate the assembly phases.
I proceeded as a self-taught but I followed many useful tips.
In some cases, the solution I adopted for a specific problem was perhaps not the best.
Don't be afraid to comment negatively on some choices.
If, however, some technical choices, a little out of standard, can be useful to others I will be really happy.
Therefore, after having opened the internal spaces of the hull, it was necessary to carefully introduce: engine, servomechanisms, receiver, voltage variator and batteries.
Already in the project, their placement was as low as possible.
However, before this I thought about the engine-propeller transmission.
There are already complete steel propeller shaft cases on the market, but I preferred to do it myself because they weren't the right length.
In these attached images, you can see some assembly phases.
The axis is a solid brass rod that I threaded. Its diameter is 4 mm.
The micro bearings have an internal diameter of 4 mm and an external diameter of 8 mm.
The external case is made up of an aluminum cylinder with an internal diameter of 8 mm and an external diameter of 10 mm.
The internal spacers, which separate the bearings, are brass tubes with an external diameter of 8 mm.
The aluminum tube has small tubes for inserting grease from the outside.
All full of silicone grease, it is very difficult for water to reach the bearings, much less inside the hold.
Unlike almost all other elements, the transmission tube is not removable, it is firmly stuck to the bottom of the hull, immersed in resin.
It is perfectly aligned with the engine and is connected to it with a normal joint (not a universal joint). Furthermore, it is parallel to the deck and keel. In this way all the thrust is useful and there are no vertical components that are wasted, as in the case of a slightly oblique axis.
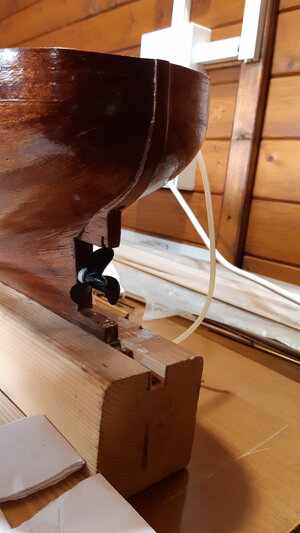