- Joined
- Jun 29, 2024
- Messages
- 1,021
- Points
- 393
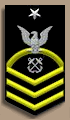
The Sherline Lathe/ Mill headstock works exactly as you describe; threaded hole in the end of the tapered stock and a threaded spindle for mounting larger chucks.
Sandekus: I was criticized on another website by a knowledgeable machinist for imposing side loads on a Jacob’s Chuck; just what we are discussing. A reason for participating on this forum is to learn from others with more expertise and experience. This is particularly true of power tools where many modelers (myself included) tend to buy that next “must have tool” to solve all of our problems and then wind up abusing it. Perhaps it’s just us Yankees, but we never read the instructions!!
Roger
Sandekus: I was criticized on another website by a knowledgeable machinist for imposing side loads on a Jacob’s Chuck; just what we are discussing. A reason for participating on this forum is to learn from others with more expertise and experience. This is particularly true of power tools where many modelers (myself included) tend to buy that next “must have tool” to solve all of our problems and then wind up abusing it. Perhaps it’s just us Yankees, but we never read the instructions!!
Roger