Hi Brett,Hi,
Like you I bought some end mills that are too large for the proxxon collet and am now looking at either an adaptor or the USOVO kit to replace the shaft. You mention here that using the correct sized collet reduces the run-off to acceptable levels but in a later post, after you installed the replacement shaft, you seem to say that even using the adaptor you are still getting run-offs of about 20 hundredths of a mm. Would you mind confirming the run off you get using the adaptor please.
I'm planning on using a 0.5mm end mill to make some gratings so a 0.2mm run off would not be good enough for the job and i would need the replacement shaft.
ALso did you find a way to identify the MF70 serial number, i've checked mine and can't find anything that would help me decide which of the shaft kits to buy.
Many Thanks
Brett
The serial number can be found on the front of the milling head (this is where I have my number).
If you have a budget and can afford to buy a USOVO replacement shaft, this is the way I highly recommend it. However, the adapter Phil shows above is a decent workaround. I've seen members buy a smaller diameter adapter and threaded it to M8. This way, you just use the existing thread on the factory shaft. The deviation is very minimum and can definitely suit modeling purposes. On my USOVO shaft, I use mills 1.00mm on a 4.00mm shaft to mill a flint bore on the gun barrel.
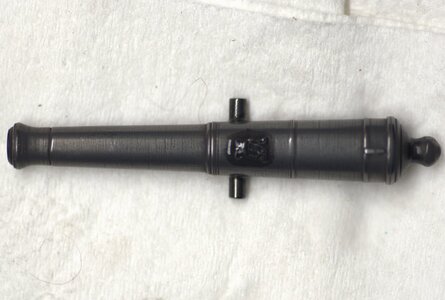
My MF70 becomes my desctop tool, I mean I don't move it in a safe place. I use it alsmost everyday and keep experementing.