- Joined
- Oct 9, 2020
- Messages
- 2,076
- Points
- 488
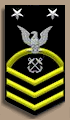
I
Congratulations on your success. I never thought of using plexiglass. Rather I used an acetate sheetWell, today my story took an interesting turn.
It's no longer about wooden composite materials; now it's about plastic, specifically plexiglass. But in order not to produce a lot of threads, I decided to write here.
We all know that plexiglass melts easily and has low thermal conductivity, making it challenging to work with.
Despite the difficulties, I decided to give it a try using a 30° engraver with a thin end measuring only 0.1 mm.
Due to the scale of the details I'm currently working with, using a larger tool was not an option.
For the Lantern glass, I used plexiglass 0.2 mm thick, and for cabin windows - 0.4 mm.
To prevent excessive melting, I needed a cooling solution for both the tool and the material. Simply using air proved to be insufficient based on my previous experience. I thought that using some liquid might be a viable idea. However, using water alone was not ideal due to its poor adhesion to organic materials, and it could potentially damage my MDF wasteboard. Fortunately, during the COVID times, I happened to have a small spray bottle containing a mixture of water and alcohol. To enhance the cooling effect, I added more alcohol to the mix and sprayed it onto the plexiglass while machining.
The spindle speed was 12000 RPM.
I must say, the results were quite satisfactory. Although the cutter didn't cut all the way through due to some melting, both the tool itself and the cutting lines remained clean. They were clean enough to meet my expectations. You can see the results in the pictures below.
View attachment 379616
View attachment 379617
The tool remained absolutely clean!!!
View attachment 379618
Although it is not completely cut through, now I have clear lines to cut. I used small scissors to finish
View attachment 379619
View attachment 379620
Do you have a similar experience? How do you cut plexiglass when necessary?
Definitely, for this thickness, the usual knife is always an option. But in this case, I wanted more preciseness, especially for the Lantern.
Have a nice time of the day,
Max