Finally, I have returned to composite (layered) wood CNC machining!
I have machined two side panels for my Santa Maria admiral's cabin.
After my first experiment, which was only partially successful, I made certain adjustments to the technology.
1) After several attempts, I realized that the accurate application of glue makes the material rather rigid, eliminating the necessity for a 3-layer sandwich. Two layers would work fine, and I even tried with just one layer!
Since these side panels will be applied on top of the final planking, I wanted the panel's thickness to be minimal. Additionally, I aimed to create an illusion that the arcs are empty, revealing the "original" cabin wall planks. To achieve this effect, I had to make precise cuts within the arcs, ensuring that the layer of walnut planks would be visible but not completely cut through.
Therefore, I have developed the following concept:
2. It became evident that the layers had to be completely flat and parallel to each other and to the surface of the wasteboard. Therefore, I spent more time flattening the surfaces. In fact, I flattened all of them
Here is the process:
1) I glued pearwood planks together. Unfortunately, I do not have a belt saw, so I am limited to the maximum width of planks I can make with my Byrnes saw - 20-21 mm (about 0.8 in) wide. Therefore, to have a wider board, I am forced to glue several planks together."
2) Then I flattened both sides of this board with CNC.
3) Then I added a layer of walnut planks. Additionally, since the two side panels are mirror symmetrical, I had to keep this in mind and maintain the respective angles of the plank layout on each half of the stock... And also flattened that layer with the CNC.
4) Of course, before undertaking all that, I designed the shape of a side panel in Fusion 360.
I aimed for a balance between simplicity and complexity. So, after some consideration, I arrived at this final design:
5) Now, onto the most intriguing part - the machining process. If all calculations have been done correctly, I should achieve the desired result. However, if any mistakes were made, half a day's worth of stock preparation will go to waste! With bated breath, I pressed the start button of the program, hoping for the best outcome.
And luck smiled upon me this time

:
And here is the result. The final maximum thickness of the detail is 1.29 mm (about 0.051 in)!
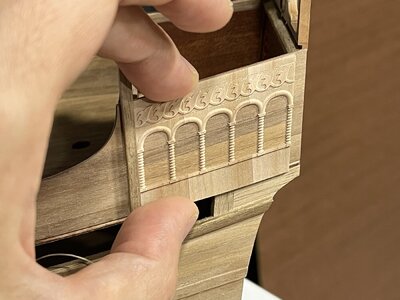