- Joined
- Sep 8, 2024
- Messages
- 140
- Points
- 78
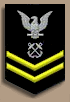
I don't want to sound picky, but I regard using filler as a failure on my part somewhere along the production line. Epoxy is the filling material of choice these days for 1:1 work - and uses inert materials in the liquid 'glue' to produce something like a putty that is both adhesive and gap filling. It is an age old cabinetmakers recipe to mix the sawdust of the groundwork with glue to produce an 'invisible' repair, and a technique I have used many times on restoration work. I even keep a tin of fine ebony dust and another of a general purpose mahogany dust for the purpose.
The point is that on new work, you should aim for accuracy in the fit and run of planks - there are plenty of treatises on how to fit planks, and how to check that the frames (bulkheads) are aligned to avoid bumps and hollows. If you follow full size practice, it becomes easier, with correctly spaced frames, to ensure a good line, and if an undersized frame has to be discarded, why, it just makes you a bit more careful on the next, and adds to your store of 'experience'. Ditto if you dry fit a plank and make it undersize in width, or bodge the joint at stem or stern. Bear in mind that full size work was intended to be self correcting as you fit each plank, so even an unexpected stealer can be justified.
If you want to create a real 'model' then I always suggest a read of Harold Underhill's books. All the way from making built up frames as per original, to applying planks, and then fittings and rigging. Never been beaten in my humble opinion.
But back to the question, now I've done with some preaching.
I would avoid using any filler which is harder than the timber I am applying it to. It will be near impossible to abrade it back to a fair surface aligned with the run of the model. Then consider what appearance you need. If you intend to leave naked timber exposed then your only choice really would be to take a scalpel, cut out the mistake, and insert new timber in the fashion of a 'repair'. Ships were repaired all the time, sometimes whilst in remote places, beached and new timbers fashioned from whatever was to hand, or even, in extremis, patched up at sea - what a job that must have been.
A new plank, or two, even inserted to a weathered, painted hull, makes a conversation piece and could draw the eye away from some area you would rather the viewer didn't spend too much time on.
If the repair is going under paint, or in so many of these kits, into the false skin of dummy planks, then old fashioned linseed oil putty can be useful. Malleable, takes a good surface, dries slowly, retains a small measure of elasticity to move with the wood. Or you can produce your own filler from sawdust - use shellac if you want something quick drying, yet controllable, and reversible. Others have already gone into PVA glues as binders for sawdust. You can also use paint and plaster. Same colour paint as you are using of course, mix way more plaster than you think it can hold, and you get a filler which is inert, and tightly bound to the paint you are using. (useful round the house too)
And finally - the restorer's friend - pumice powder. Used for grain filling under French polish (shellac) it starts life as a grey dust, but becomes almost invisible when rubbed into a crack or split or badly made joint as a part of the polishing process. Use a shellac fad reserved for the task, and rub the pumice into the split. The polish on the fad will keep it there, and after the area has dried, you can remove any surplus left around the repair with French polish in the usual manner. Good for varnished hulls.
Jim
The point is that on new work, you should aim for accuracy in the fit and run of planks - there are plenty of treatises on how to fit planks, and how to check that the frames (bulkheads) are aligned to avoid bumps and hollows. If you follow full size practice, it becomes easier, with correctly spaced frames, to ensure a good line, and if an undersized frame has to be discarded, why, it just makes you a bit more careful on the next, and adds to your store of 'experience'. Ditto if you dry fit a plank and make it undersize in width, or bodge the joint at stem or stern. Bear in mind that full size work was intended to be self correcting as you fit each plank, so even an unexpected stealer can be justified.
If you want to create a real 'model' then I always suggest a read of Harold Underhill's books. All the way from making built up frames as per original, to applying planks, and then fittings and rigging. Never been beaten in my humble opinion.
But back to the question, now I've done with some preaching.
I would avoid using any filler which is harder than the timber I am applying it to. It will be near impossible to abrade it back to a fair surface aligned with the run of the model. Then consider what appearance you need. If you intend to leave naked timber exposed then your only choice really would be to take a scalpel, cut out the mistake, and insert new timber in the fashion of a 'repair'. Ships were repaired all the time, sometimes whilst in remote places, beached and new timbers fashioned from whatever was to hand, or even, in extremis, patched up at sea - what a job that must have been.
A new plank, or two, even inserted to a weathered, painted hull, makes a conversation piece and could draw the eye away from some area you would rather the viewer didn't spend too much time on.
If the repair is going under paint, or in so many of these kits, into the false skin of dummy planks, then old fashioned linseed oil putty can be useful. Malleable, takes a good surface, dries slowly, retains a small measure of elasticity to move with the wood. Or you can produce your own filler from sawdust - use shellac if you want something quick drying, yet controllable, and reversible. Others have already gone into PVA glues as binders for sawdust. You can also use paint and plaster. Same colour paint as you are using of course, mix way more plaster than you think it can hold, and you get a filler which is inert, and tightly bound to the paint you are using. (useful round the house too)
And finally - the restorer's friend - pumice powder. Used for grain filling under French polish (shellac) it starts life as a grey dust, but becomes almost invisible when rubbed into a crack or split or badly made joint as a part of the polishing process. Use a shellac fad reserved for the task, and rub the pumice into the split. The polish on the fad will keep it there, and after the area has dried, you can remove any surplus left around the repair with French polish in the usual manner. Good for varnished hulls.
Jim