- Joined
- Apr 15, 2020
- Messages
- 446
- Points
- 278
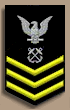
Hi Ted,A very nice project - love the detail and the effort that has gone in to the ship!
Would love to build her, but sadly, SABLE rears it's ugly head and I probably don't have enough years left!
(SABLE: Stash Accumulation Beyond Life Expectancy)
Will follow with great interest - you never know?...............
Ted
Your POF (or fully framed model) Kingfisher left a deep impression on me, which is the ancestor kit I know.
Although I can't understand the meaning of all the sentences you said accurately, you mentioned time. There may not be enough time.
Indeed, time is a big factor in my consideration.Maybe every developer has his own ideas, which will accompany his products. A very important consideration is to save time. I hope most modelers can reduce the 'pain' of milling, but some people think that milling is a kind of happiness, whether it is pain or pleasure, milling is indeed time-consuming and there is a lot of dust. My idea is to reduce the milling time as much as possible, so that modelers can enjoy the pleasure of completing a model and the assembly process, in which they have a deeper understanding of the structure of the ship model.
Therefore, the simpler, more efficient and practical design concept is always with me. Through Brian's post, I also learned a lot of different needs and feedback. The balance between price and quality is the consideration of many modelers.
Making these anchor chocks by hand is very tedious, tedious and time-consuming, but everyone knows this structure, and it is very simple. Isn't good to leave this low-level work to CNC? This kind of processing may only take 1 hour to process all the anchor chocks required by stern sections, and it is quite accurate. This can save modelers a lot of time.
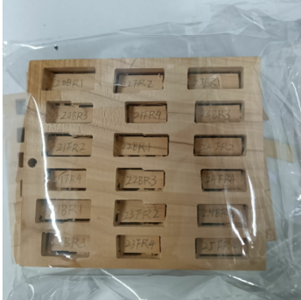
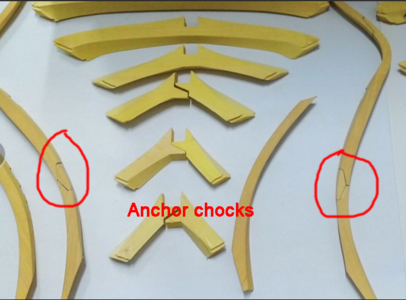
In the past, because the kit of POF was too complex, it was difficult to popularize, and it could not solve the complex splicing, especially the 'real' frames
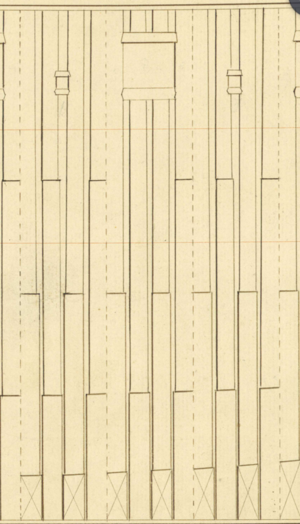
Since the sided of frame is different from the bottom up, almost no one can solve this problem before, so it (frames) can only be simplified greatly. But this is very simple for me, so the 5th rate is the smallest ship I will develop. Assembly plates and gaskets of different thickness can solve this problem, and the cost is only $10-20.
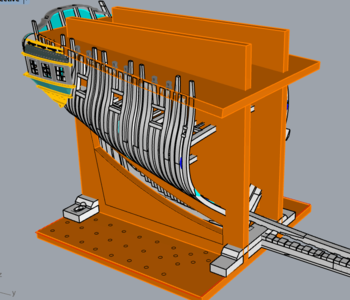
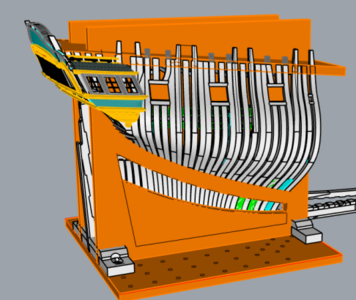
Due to the price factor, I redesigned the frame jig, and I almost gave up the original complex jigs, in which the assembly board can be used for the base of jig one more time, saving costs and improving utilization. It is simple and efficient, and will not interfere with the planking on main wale.But it still needs to be tested and optimized.
Said too much,...Ha,
Thank you!
Dahai
Last edited: