After years of my Dad telling me that I should, I finally cracked open Master and Commander and started reading. I of course got hooked immediately, and in addition to now having bought and read the first nine books of O'Brien's magnum opus, I determined that I had to build a model ship of the era. Now as the title says, this is something I've never done before, but I wouldn't count myself a complete novice, as I've done 1:1 scale woodworking my whole life (furniture and cabinetry mostly), and have been pretty obsesses with plastic models of airplanes these last six years. But still I figured I ought to find something reasonably straightforward and of manageable size to start with. The Vanguard Models products get great reviews, and one can peruse their extensive and detailed instruction manuals on-line. So despite that fact that they are definitely at the upper end of the price range, I figured this one, one of their simpler kits, would be a fine place to start.
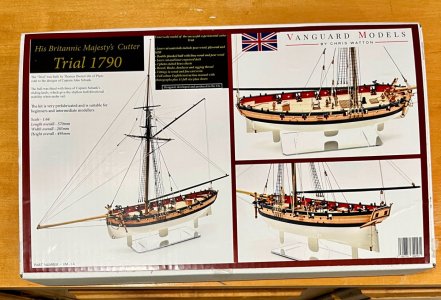
In addition to the deluxe full-color, spiral bound manual, there's a full set of to-scale plans included. The assembly process is quite straightforward, with the laser-cut MDF parts needing barely any sanding to fit perfectly. As easy to do as a high-quality plastic kit. So I ended up getting sucked in and neglecting to take any process photos until the point where I already had the keel, bulkheads, lower deck, and various bracing members joined up:
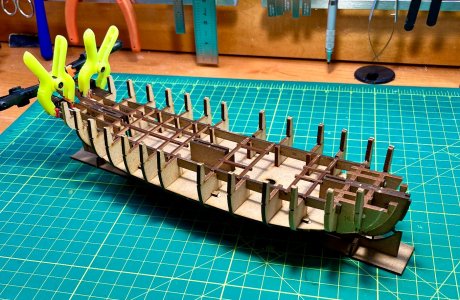
From there it was a matter of adding the upper deck underlayment:
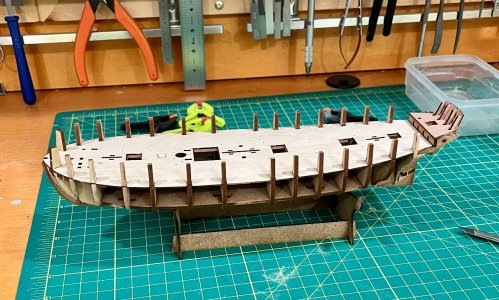
And the fairing the bulkheads, first one side...
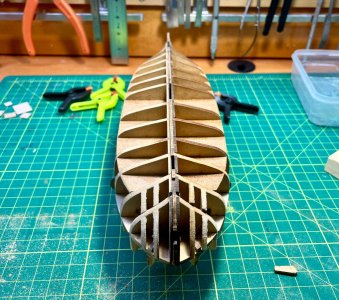
And then the other.
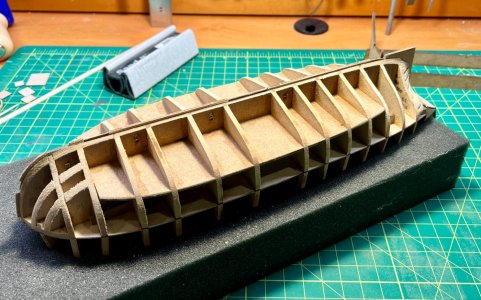
I think I slightly overdid it on the stern filler pieces right at the top by the transom, but it's not so much that I won't be able to compensate with some filler post-hoc.
I added the first planking strip next to the keel, per the instructions.
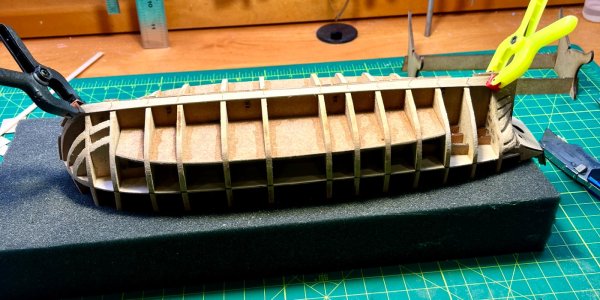
And then the first layer of ultimately three that will make up the bulwarks.
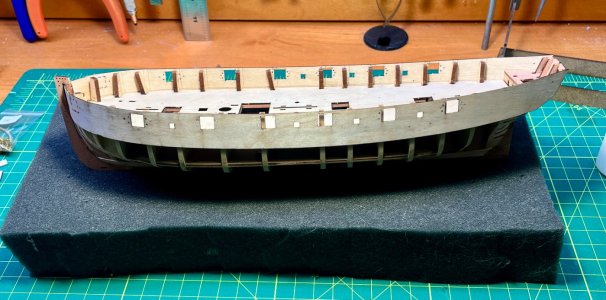
I need to fair that up to the transom a bit and then I will be ready to start planking! So far this has been easier than I had been imagining it might be, thanks mostly to the great kit engineering and clear instructions. But I also have a sense that I'm doing the easy parts now, and that it may get more challenging as I move on to rigging a bit later.
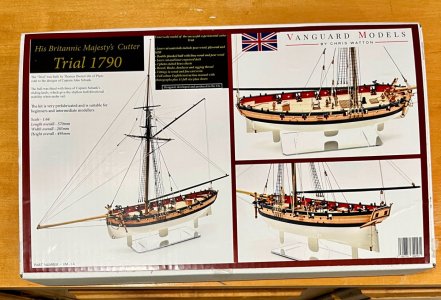
In addition to the deluxe full-color, spiral bound manual, there's a full set of to-scale plans included. The assembly process is quite straightforward, with the laser-cut MDF parts needing barely any sanding to fit perfectly. As easy to do as a high-quality plastic kit. So I ended up getting sucked in and neglecting to take any process photos until the point where I already had the keel, bulkheads, lower deck, and various bracing members joined up:
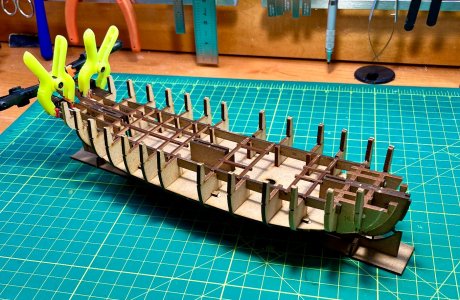
From there it was a matter of adding the upper deck underlayment:
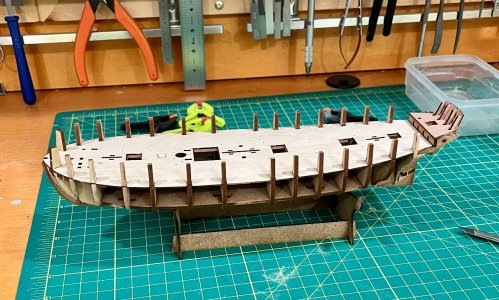
And the fairing the bulkheads, first one side...
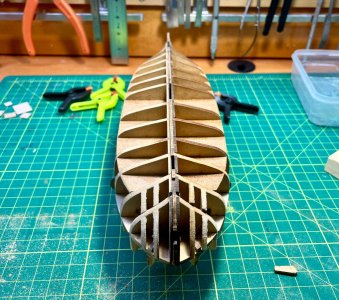
And then the other.
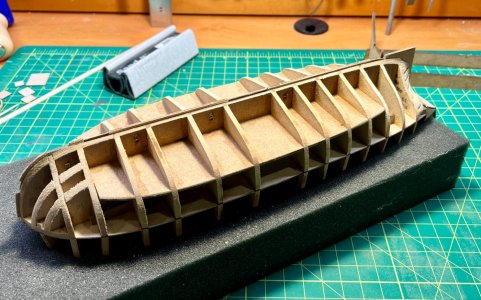
I think I slightly overdid it on the stern filler pieces right at the top by the transom, but it's not so much that I won't be able to compensate with some filler post-hoc.
I added the first planking strip next to the keel, per the instructions.
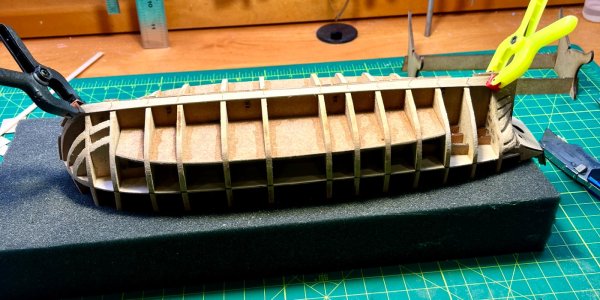
And then the first layer of ultimately three that will make up the bulwarks.
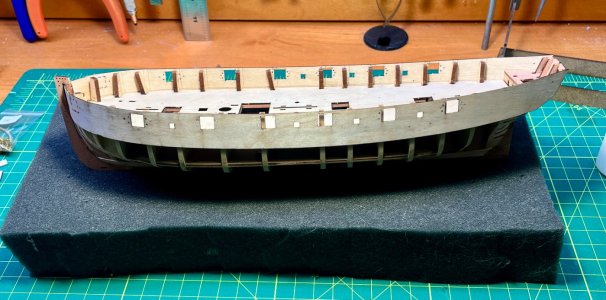
I need to fair that up to the transom a bit and then I will be ready to start planking! So far this has been easier than I had been imagining it might be, thanks mostly to the great kit engineering and clear instructions. But I also have a sense that I'm doing the easy parts now, and that it may get more challenging as I move on to rigging a bit later.