Gratings consist of longitudinal and transverse rails, reinforced in the frame. They were used on sailing ships for ventilation and lighting of the lower decks and could be in the form of removable hatch covers or fragments of the deck flooring. Also, by the type of gratings, platforms of mars, latrines, transitional bridges, and fish boats were made, so the modeler often has to deal with the manufacture of gratings for his models.
Greetings folks. Just as other features of models were simplified, so was the manufacturer of gratings. There are more than several methods of making your gratings for the model. Until well into the eighteenth century, with very few exceptions, the gratings were simulated by piercing squared holes in solid wood. The methods chosen by the modeler depend on many factors. I would say the common are the scale and equipment you own. In many years of my modeling life, I have adapted a method using a table saw and achieved very good results. However, I always wanted to try other methods to find out the benefits there. Since I recently modify my Proxxon MF70 a decision was made to try out the method of utilizing the mill. BTW, this method is not new and don't develop by me. SOS has several posts, by many of our members, describing this method in great detail. I encourage you to check them out.
Using the table saw is a great method of simulating gratings for larger-scale models. Making grating for smaller scales requires slot-saw smaller thicknesses which is hard to find. Today, I will make two sample gratings, they are not specific to any of my models or scales. The first one will be 0.90mm x 0.90mm cell, another one 1.50mm x 1.50mm cell. I used some of my scrap wood suitable for this purpose and strips stock I milled for treenails a way back. To mill the grooves I have used 0.9mm and 1.5mm endmills purchased on AliExpress, by company BB (highly recommend this brand and their endmills)
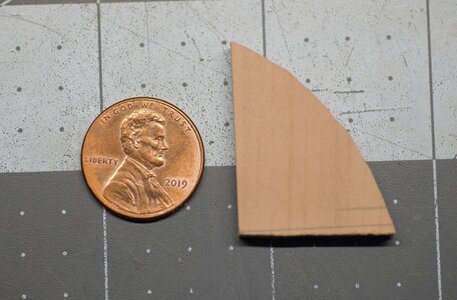
The first step is to even the surface. Here comes in handy my newest ER11 system. I use a 7.0mm endmill, Yea... fewer moves. Once the surface is even, I use a 0.9mm endmill to cut the 'Y' axis groves. Make a note, that those groves should be as twice deep as the 'X-axis groves. This will ensure the 'hollow' appearance of the cell.
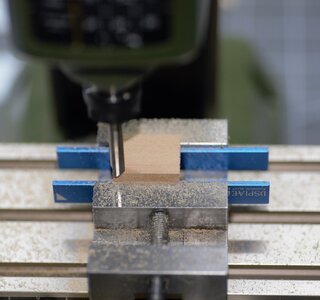
The 'Y-axis groves were milled first, using 0.9mm and 1.5mm for each grating blank. I use the full deep required and a single path for each grove.
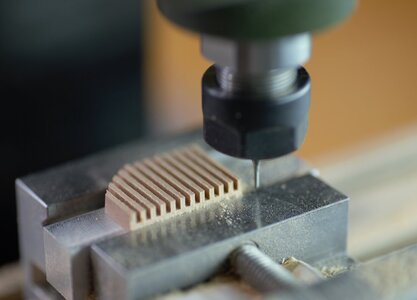

The X-axis groves next. Don't plunge the mill to the entire deep of the required grove, you are risky to nock the next cell out. I suggest using two or three passes (per grove) gradually moving the Z-axis until you reached the desired depth.
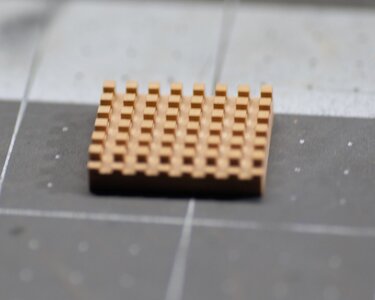
I just realize that didn't take photos of the process of gluing the X-axis planks. This shouldn't be too difficult and requires just a drop of PVA glue (in each cell) and firmly pressing down the planks. Once dried, you have similar to this.

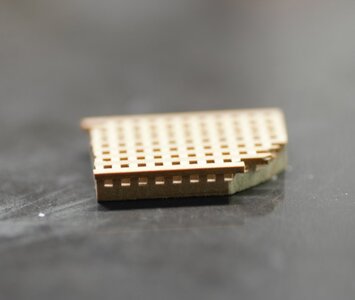
Using the large size mill, I made the surface even.
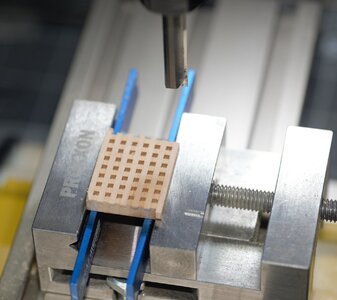
Bolts imitating by drilling holes using 0.2mm. I think, it is a bit oversized but I don't have a 0.1mm drill bit
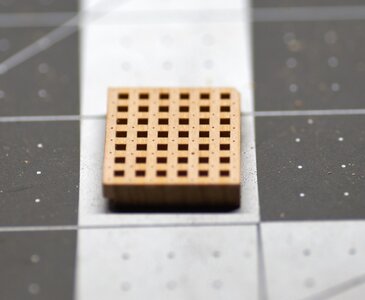
One coat of Tung oil finished both examples. Just for the sake of relative size, I use the figure of a 1:72 scale. The first images are gratings 1.5mm x 1.5mm cell

Here are the images of the grating sample with cell 0.9mm x 0.9mm
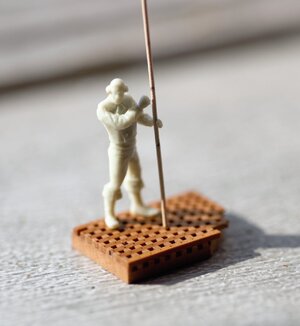

I am really pleased with both examples and will definitely use the mill method in my future builds. How about you? Do you like it?
Greetings folks. Just as other features of models were simplified, so was the manufacturer of gratings. There are more than several methods of making your gratings for the model. Until well into the eighteenth century, with very few exceptions, the gratings were simulated by piercing squared holes in solid wood. The methods chosen by the modeler depend on many factors. I would say the common are the scale and equipment you own. In many years of my modeling life, I have adapted a method using a table saw and achieved very good results. However, I always wanted to try other methods to find out the benefits there. Since I recently modify my Proxxon MF70 a decision was made to try out the method of utilizing the mill. BTW, this method is not new and don't develop by me. SOS has several posts, by many of our members, describing this method in great detail. I encourage you to check them out.
Using the table saw is a great method of simulating gratings for larger-scale models. Making grating for smaller scales requires slot-saw smaller thicknesses which is hard to find. Today, I will make two sample gratings, they are not specific to any of my models or scales. The first one will be 0.90mm x 0.90mm cell, another one 1.50mm x 1.50mm cell. I used some of my scrap wood suitable for this purpose and strips stock I milled for treenails a way back. To mill the grooves I have used 0.9mm and 1.5mm endmills purchased on AliExpress, by company BB (highly recommend this brand and their endmills)
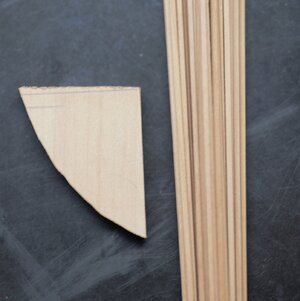
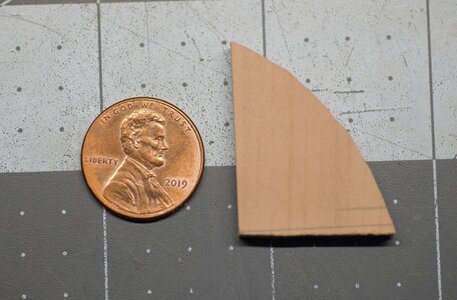
The first step is to even the surface. Here comes in handy my newest ER11 system. I use a 7.0mm endmill, Yea... fewer moves. Once the surface is even, I use a 0.9mm endmill to cut the 'Y' axis groves. Make a note, that those groves should be as twice deep as the 'X-axis groves. This will ensure the 'hollow' appearance of the cell.
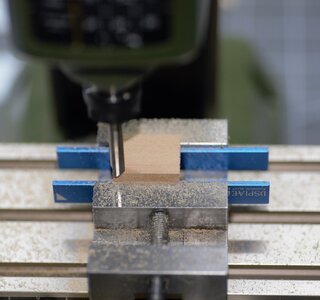
The 'Y-axis groves were milled first, using 0.9mm and 1.5mm for each grating blank. I use the full deep required and a single path for each grove.
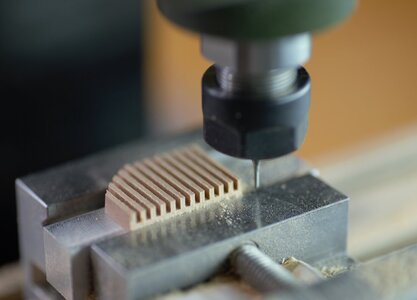

The X-axis groves next. Don't plunge the mill to the entire deep of the required grove, you are risky to nock the next cell out. I suggest using two or three passes (per grove) gradually moving the Z-axis until you reached the desired depth.
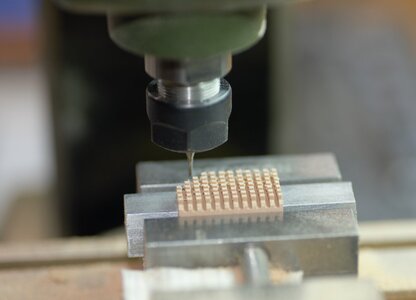
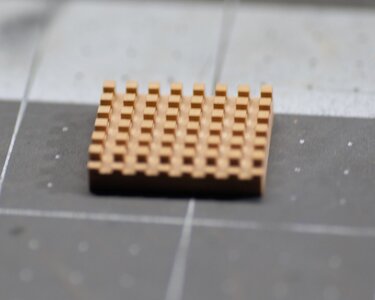
I just realize that didn't take photos of the process of gluing the X-axis planks. This shouldn't be too difficult and requires just a drop of PVA glue (in each cell) and firmly pressing down the planks. Once dried, you have similar to this.

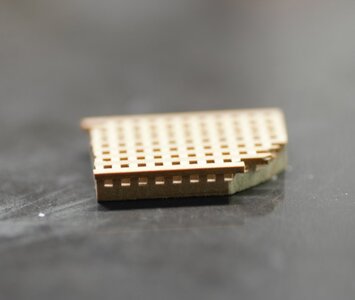
Using the large size mill, I made the surface even.
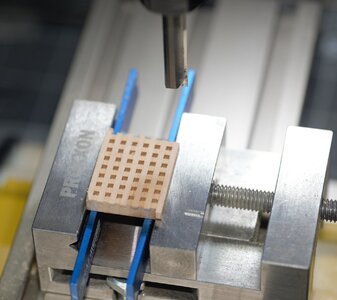
Bolts imitating by drilling holes using 0.2mm. I think, it is a bit oversized but I don't have a 0.1mm drill bit

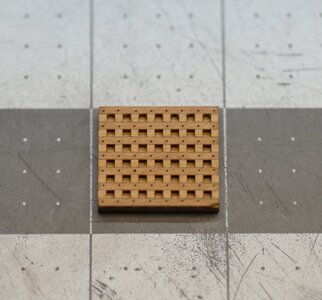
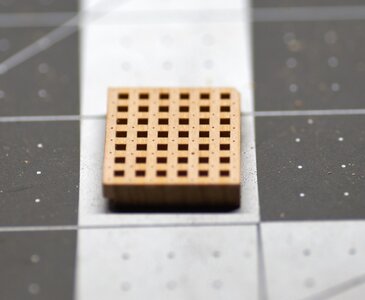
One coat of Tung oil finished both examples. Just for the sake of relative size, I use the figure of a 1:72 scale. The first images are gratings 1.5mm x 1.5mm cell
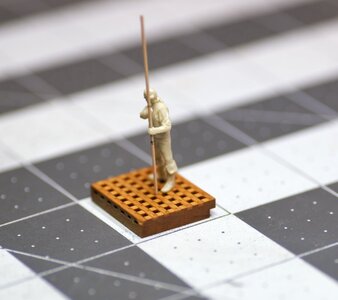

Here are the images of the grating sample with cell 0.9mm x 0.9mm
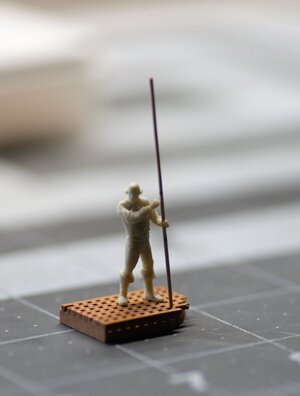
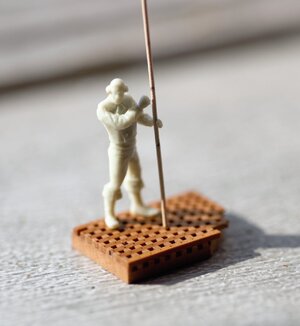

I am really pleased with both examples and will definitely use the mill method in my future builds. How about you? Do you like it?