- Joined
- Apr 10, 2020
- Messages
- 651
- Points
- 353
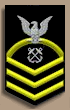
the weapons are not good but if you know a bit of modeling is doable
Daniel
Daniel
**VIEW THREAD HERE** |
I sliced it in Bambu Studio (the app I use to print with my Bambu Lab A1), and this is what the file looks like when I import the .stl and then rotate it to fit on the build plate:the stl file
If you have an .stl file that you can share of the captain you want your friend to print, I'd like to print it out myself to see how it turns out... and then I can post the image here so you can see the results. I'd just need to know the height in mm that you would want the final figure to be.... and I can scale it accordingly. Because of the small size, it would only be a few grams of filament and very fast to print... even at high quality.Hello Dan ,I waiting for a friend to get back from holiday and I will print my captain for my model
Daniel
Looks pretty good in Bambu Studio (3D slicer)... I've just kicked off a sixteen hour print, but as soon as it wraps up, I'll give this a shot with white PLA filament, and post the results here.Here's what I came up with in a quick mess around. Can't try printing until I get home in a few days. It's supposed to be Russel Crowe as Jack Aubry.
Here's the image it's based upon.
View attachment 532029
And below is the STL for anyone interested.
Cheers,
Todd
To remove the bench, you can import your .stl into www.tinkercad.com. Use the rectangular void (hole) shape, and fit it in to replace the bench... then merge the two objects and you'll be left with just the model of the lady... sans bench. You can then export that as an .stl for 3D printing again. I've just done that for you, so you can check out the attached .stl file. The only issue with the model is that her left hand sits flat on the bench and is a bit amputated... and when you remove the bench, the hand is still compromised. The rest of the model looks okay though.Hello ,
For my model I will make 3 figures , one helmsman one captain/admireal and a lady seated on a bench ( i have to remouve the bench from stl)
The helmsman
So what is the next step in making these.
I'll try to answer you question.So what is the next step in making these.
Is it just sanding