planking up the bulwarks
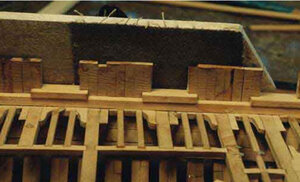
After setting the frames up there will be slight variations in the alignment of the top of the frames. Glue a piece of sandpaper to a flat piece of wood to use for sanding flat the outside of the bulwarks. The bottom of the wood piece is used to ride along the top edge of the wales to give an even sanding from top to bottom of the bulwark. The inside is not possible to sand in this manor so I left it as built except where a frame or filler piece stuck out to far. In this case I used a disk sander on the Dremel tool to bring it into alignment. Should any frame or filler piece fall short because its to thin this is really of no big concern. The planking will cover any hollows and glue will fill in the gap between the plank and the frame surface.
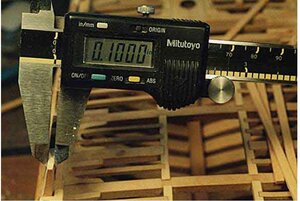
Sand down the bulwarks until they are between .090 and .100 the actual thickness is 4 to 5 inches on the real ship. You don't have to be dead on for the top of the frames because nothing will actually show. Planking covers the sides and the cap rail covers the top.
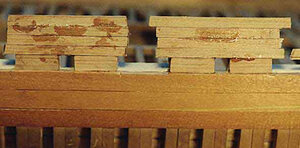
The first plank above the wale is wider than the rest of the planking. This was done to match the top of the plank to the top of the row port. Otherwise a notch would have to be cut into the bottom of the next plank. Each plank edge is cut with a slight bevel to insure a tight fit to the one next to it. At this stage of planking as you can see there is no concern to neatness, the planks were allowed to run beyond the edge of the gun port and glue from clamping ended up on the surface of the planks. The glue used on the model is epoxy and it cleans off the surface without a trace. However some glue will leave a stain or residue showing up after a finish is applied to the wood.
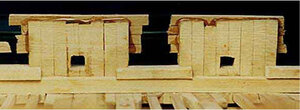
Looking from the inside of the bulwarks you can see the run over of the planking into the gun ports. By using the side of the ports as a guide, a razor saw is used to cut the planking even with the port sides. Then a little touch with sand paper or file evens everything out. Due not cut the top plank down to the frame tops. A sheer will be sanded later when the cap rail is installed.
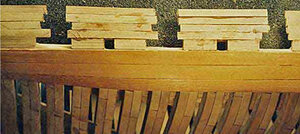
Each bulwark section is planked in the rough; once they all have been planked they are then trimmed and cleaned up.
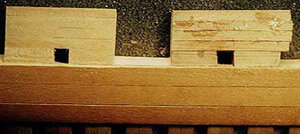
Here we see a comparison between a roughed in section and a finished one. All the surface glue is cleaned off and the planking trimmed to the edge of the gun port. By creating the row port with the planking itself, it creates a clean square port. This works out better than trying to cut them into the planking.
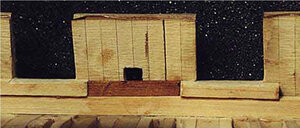
All the bulwark sections are trimmed on the sides and we are ready to plank the inside. To even out the frames, if needed, a sanding disk was used on a Dremel tool and the inside was given a light once over sanding. Here you can see a little unevenness of the frame tops. This is best left as it is, once the inside and outside planking is on, an overall sanding of the tops will be done later to even things out.
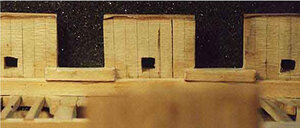
On the outside of the bulwark we started with a wider plank to match up with the top of the row port. Not so on the inside, because the waterway is slightly higher than the top of the wale. Start the inside with one of the narrower planks and cut it to fit between the sills. The sill thickness and the planking are very close to the same size, if not, you can sand down the sill to match up with the top of the plank. You want the top of the plank and the sill to match up or you will be notching the next plank to fit.
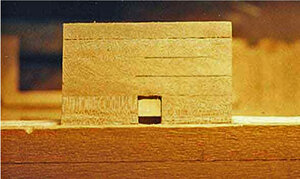
Look very close at the row port opening, looking through it you can see the first plank inside the bulwark. The plank will match up with the top of the sill, but it is slightly too high for the row port. You will need to get in there with a sharp pointed knife and cut the plank down even with the bottom of the opening.
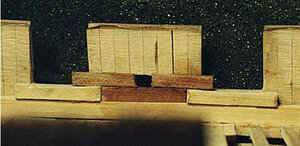
The next plank will take a little fiddling with to get it to rest square and even with the port sill and the plank below it. The end of the plank is set even with the row port and let to overhang the edge of the gun port.
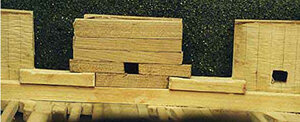
Planking on the inside, is done the same way as it's done on the outside. The top plank is the widest plank. In other words the inside is planked opposite of the outside, with the wider plank on the top, inside the bulwark, while on the outside it is at the bottom. It's a little tricky giving the inside a final sanding because you have to work around the gun port sill. Once all the planks are in place they are cut and sanded to the side of the gun ports. Again notice the unevenness at the top where the inside and outside don't quite match up. No problem, a sheer is sanded along the top before the cap rail is installed.