As you probably notice, these ships had transom either in bow as in stern. The stern one we already described, was used not just to increase capacity, also to received the back piece that was used as a “mechanism” to operate the rudder..... The internal layer, received also the first planks layer and the second (rudder mechanism) received the second planks layer.....
Well.... here some pictures in the “real life”....
YESSS !!!! I have started the planking with all its difficulties.....
FIRST..... let’s remember that it need to build PLANKING FIRST FRAMES AFTER. This is pretty much the same that Vikings and Egyptians. Also let’s remember it has 2-3 planking layers
It is a “kind” of clinker with e very specific distribution. The first layer, is rabbeted as you can see. And let me tell you.... I did it.
It really helps a lot to fix the planks.
Let’s try a little harder to see how the clinker looks like....
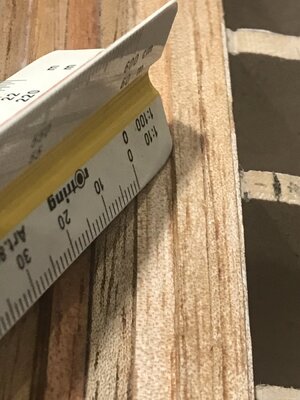
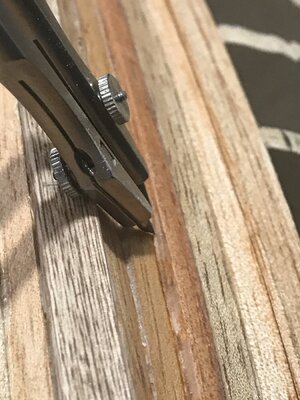
We will continue with the planking up to the bulkheads level.... Then we will install the “team” bulkhead-Frame” to complete afterward the planking. Do not forget this is just the first planking layer.
Before going to the second layer we will need to figure out how to proceed with the brackets....