- Joined
- Dec 3, 2018
- Messages
- 2,449
- Points
- 538
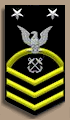
Hello again friends.
I need to change the blades on my DH40.
I'm afraid of making mistakes so that the planks get different thicknesses on each side.
How to do this correctly.
Do any of you have any tips on this topic, please show pictures or video.
Regards Knut-
I need to change the blades on my DH40.
I'm afraid of making mistakes so that the planks get different thicknesses on each side.
How to do this correctly.
Do any of you have any tips on this topic, please show pictures or video.
Regards Knut-