7. Wiring and lights.
After completing the planking, it was time to work on the wiring for the lights.
Even before purchasing the "Santa Maria", I had the idea of incorporating lighting into.
I had even created a lower-hold compartment to house a couple of light sources.
Although I would approach it differently now, I am still satisfied with how it looks.
For the power connection, I decided to try a special approach.
Instead of the common method of adding a "third" leg on the model stand with contact wires inside, I opted to use just two legs.
Since these legs already contained a metal rod, I thought, why not utilize them as electric current conductors?
Now, having completed all the lighting work (which I will share in future posts), I can confidently say that this was the right strategy.
Additionally, as I examined the finished hull, it became apparent that the holes I had previously made in the bulkheads were not suitable for conveniently running the wires. To address this, I simply cut pockets from the top of the bulkheads to accommodate the wires.
That is how I plugged the wires in:
Here is the result after connecting and placing all the main wires inside the hull:
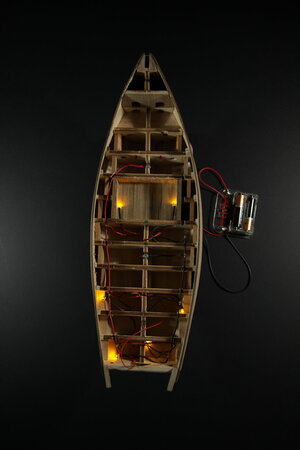
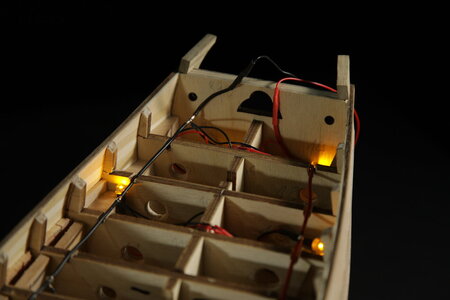
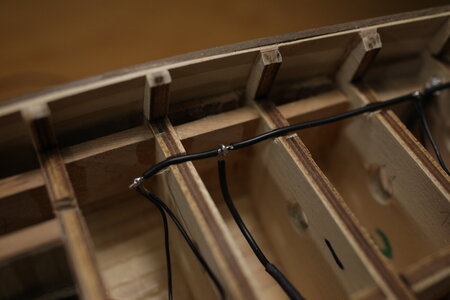
I also created a temporary stand for the model and experimented with a model nameplate, allowing myself to gather some inspiration for future designs.
8. Deck planking & Co
Now it's time to focus on the deck, internal bulwark planning, and top timbers.
The process was fairly straightforward. I began by installing a central plank and then proceeded to place the remaining planks symmetrically.
I've just cut the planks according to the deck curvature, with no complicated plank layouts. Kept it simple. Also, I did not darken plank edges (neither with pencil nor with thread or other traditional ways).
Again, I decided to be very simple there.
Instead of darkening the plank edges with a pencil or thread, I opted for a diluted brown oil paint to lightly darken the almost white deck wood.
The paint seeping into the plank joins created darker and well-defined lines, achieving the desired deck-planking appearance.
Here are my "secret weapons" for a good deck outlook

:
- I repeated the tinting procedure 3-4 times, wiping off the excess paint with a napkin and allowing the surface to dry each time.
- After tinting, I covered the deck with linseed oil. Once it absorbed sufficiently (usually the next day), I sanded the deck with 1000-grit sandpaper and after that once more repeated the process with 2000-grit sandpaper.
The result is a "semi-glossy", soft, and warm-to-touch deck with distinct planking and nailing structure.
You can see the end result in the pictures below and watch the corresponding video on my channel (
linked here).
Highlighted by own LEDs:
Then I installed top timbers, waterways and applied finishing planking in between.
It was nothing significant in the area of the waist.
However, I had to behave differently in the quarterdeck area.
According to Amati's instructions, all the decks are flat, which doesn't accurately reflect reality. Therefore, I decided to deviate from this and aim for a more realistic representation. I wanted to introduce curved beams under the quarterdeck, which meant I needed suitable top timbers to support them.
Additionally, I noticed that the height of the quarterdeck above the waist, as suggested by Amati, was unacceptably low. To address this, I raised the height by at least 4 mm for a more accurate portrayal.
Furthermore, I had to address the challenge of concealing the wires inside the rear top timbers. This posed a potential issue as it could compromise their rigidity. I had to find a solution to ensure both the functionality and appearance of the top timbers.
I came to this shape of supports under the quarterdeck. It's a kind of hybrid of top timber and knee...

Sorry for the red color
After installing all these components in their respective positions, I achieved the following result:
9. Guns
Guns... They have been the first candidate for replacement. Upon initial inspection, I was dissatisfied with their color, precision, and metallic carriages.
Here's how the gun looked straight out of the box:
I thought I would at least put barrels on my lathe.
At first, I considered putting the gun barrels on my lathe for some modifications. However, after careful consideration, I decided to keep the barrels as they were with just a few adjustments:
- I drilled the cannon bores to a depth of at least 8-10mm. Initially, they were only 1-1.5mm deep!
- I cleaned the barrels, removing the strange "brownish" and "copperish" color, revealing the white alloy underneath. Then, I blackened them using Brass Black.
As for the metallic carriages, I decided to completely replace them. I proceeded to cut wooden carriages as replacements.
The idea was to be closer to lombard cannons of this type:
However, since these guns would eventually be hidden under the quarterdeck, I didn't see the need to invest too much time in their modifications.
Here is the comparative result of my experiments:
10. Forecastle
Having in mind some deeper modifications of that area, I decided to refuse of using the forecastle base, proposed by the kit.
Furthermore, I realized that the "tilla" (the space under the forecastle) should not look the way Amati proposed. Unfortunately, it was already too late to correct this as I had not yet received my books about the Santa Maria, which would have provided the necessary information.
In hindsight, the wall of the "tilla" should not exist at all, and this is something that should have been addressed from the very beginning.
This is what we have in available reconstructions (X. Pastor's book):
And here is what Amati designed:
After considering of modifications possible in this situation, I came to this mockup:
I initially created a cardboard version to quickly assess its fit. Additionally, I decided to conduct a small experiment. The planks you see in the above picture were all cut by myself from a piece of pearwood. I did not use any planks from the kit for this detail.
For the first time in this model, I chose to use the "pre-glued" method for planking. This involved gluing the planks together before cutting the detail.
And this is how the detail looks after cutting. Correct centering on the CNC table gave me almost perfect symmetry of planks.
The assembled Forecastle looks like this:
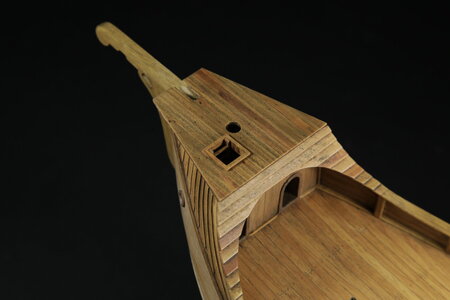