Hello @Bluebeard. I looked but it seems I did not take a picture. But it's not tricky. I simply wrapped the brass around the pin that I was using as the pintel. I then grabbed the brass strip (still wrapped on the pin) with a tweezers with very thin blades and bent out the brass arms to the left and right. I could then bend those arms to the rudder or the sternpost.
Several thoughts: the masters all solder these hinges but I have not tried that and was concerned I would make a mess of it at this scale. What you see in my log is the result after many failed attempts. What eventually won the day for me was finding/using brass that was thin enough that I could bend it with precision yet thick enough to hold its shape once I had bent it the way I wanted it. I ended up using 0.005 brass shim stock. I could cut it with a utility knife and it met these criteria. Once I started using this material the magic happened: nice tidy hinges with no soldering.
Hope this helps. I could recreate the process and take pictures if that would be better...
Hello @Bluebeard. I looked but it seems I did not take a picture. But it's not tricky. I simply wrapped the brass around the pin that I was using as the pintel. I then grabbed the brass strip (still wrapped on the pin) with a tweezers with very thin blades and bent out the brass arms to the left and right. I could then bend those arms to the rudder or the sternpost.
Several thoughts: the masters all solder these hinges but I have not tried that and was concerned I would make a mess of it at this scale. What you see in my log is the result after many failed attempts. What eventually won the day for me was finding/using brass that was thin enough that I could bend it with precision yet thick enough to hold its shape once I had bent it the way I wanted it. I ended up using 0.005 brass shim stock. I could cut it with a utility knife and it met these criteria. Once I started using this material the magic happened: nice tidy hinges with no soldering.
Hope this helps. I could recreate the process and take pictures if that would be better...
Thank You Dockattner for the input.
Today I went out and bought a soldering gun and tried again and just like you said....it was a mess.
So I will give your method a try. I do have the thin brass.
Now I have a light at the end of the tunnel.
Thanks buddy.
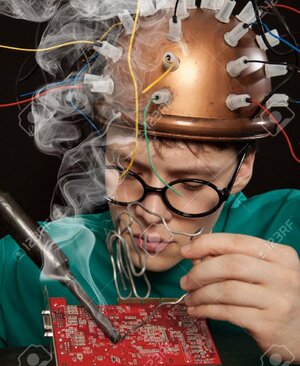