I ran into another problem with the supplied parts. The directions call for straight rods to make several parts but they give you a coil of wire. There is no way I can draw out 2mm wire into a straight rod. Just to heavy. If anyone is contemplating this kit I would order some 1mm, 1.5mm, and 2mm rod as I just did. The best I could do is the blackened rod in the center of the photo. Will wait until my order gets here to continue.
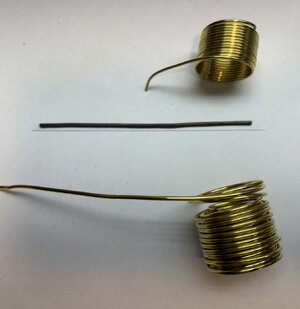
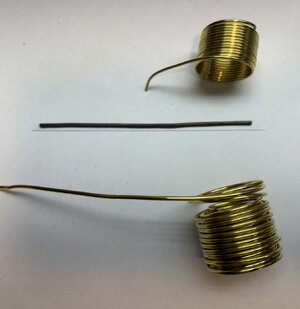