For my future project I am collecting timber. Recently I was already able to buy some pear, boxwood and also old ebony piano keys, all via internet.
Last weekend I got in contact with somebody who harvested a part of his pear orchard where he removed 200 trees and he sold the logs of 220 cm x 15 -20 cm for only €3,- per log. You understand my hobby hart could not refuse this so I bought 11 pieces. Unfortunately my small trailer could not take more.
These are the 11 logs harvested last winter.
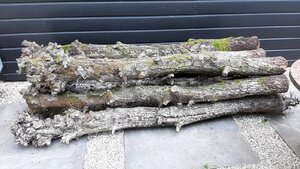
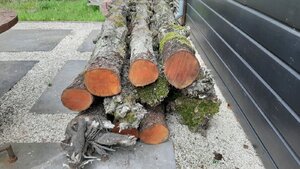
In this blog I will transfer my log step by steep to usable timer. I am certainly not a timber expert but we all learn by just doing it. More to come.
Last weekend I got in contact with somebody who harvested a part of his pear orchard where he removed 200 trees and he sold the logs of 220 cm x 15 -20 cm for only €3,- per log. You understand my hobby hart could not refuse this so I bought 11 pieces. Unfortunately my small trailer could not take more.
These are the 11 logs harvested last winter.
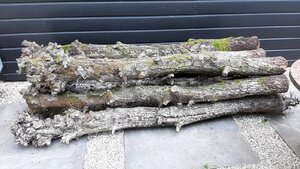
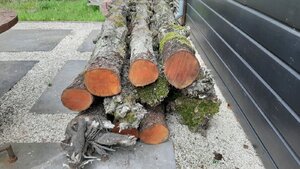
In this blog I will transfer my log step by steep to usable timer. I am certainly not a timber expert but we all learn by just doing it. More to come.
Last edited: