- Joined
- May 1, 2023
- Messages
- 115
- Points
- 113
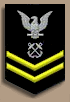
While your block design is good, are you sure it's accurate to the period for your Santa Maria? They look more modern to me.
In the instructions to my Ragusian Carrack are many illustrations used by MarisStella for their Santa Maria model, and their model ship school, which builds the Santa Maria. I won't compare your wonderful build work and design with any kit, but the illustration below shows block designs intended for their Santa Maria model and, I think, possibly more appropriate design for yours as well:
View attachment 391509
The 14th century design would appear both more accurate (to me) and easier to manufacture for you.
Well, @Signet ,no worries!

I've established this thread specifically for sharing ideas, proposals, and criticism. While I may not currently possess the knowledge on how to create blocks, my "don't know" translates to "won't give up." Instead, it means "I'll figure out how." As a result, I'm open to any suggestions or thoughts you might have on this matter!
Maybe you are right.
And thank you for sharing this Marisstella paper. I think it may be useful.
In my "researches" so far I referred to Zu Mondfeld and X. Pastor.
I share them here - maybe it will be useful for someone.
here is what Zu Mondfeld proposes in his book about Santa Maria:
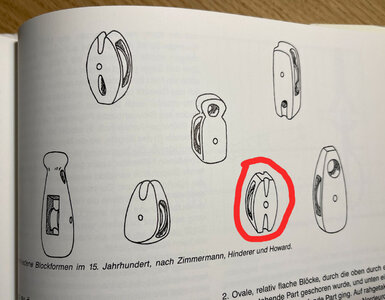
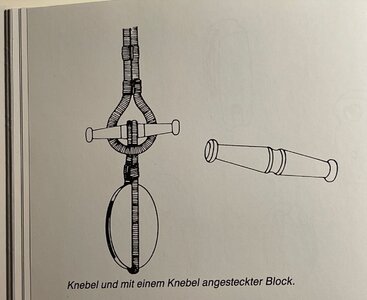
In red is something, I try to come close to in my experiments now...
And here is what Pastor offers:
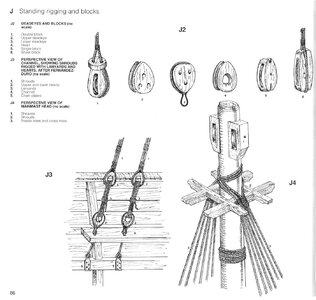
Here position 5 is close to what I plan to make.
And with regard to historical realism, I recommend everyone to watch the latest video of Dr. Kroum Batchvarov (it's just about Olga's and MarisStella's Carrack and S. Maria)

Last edited: