- Joined
- Apr 12, 2025
- Messages
- 262
- Points
- 158
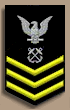
I'm now working on the frames. To simulate the look of hand hewed framing timbers I'm laminating 9 pieces of 1/32" Basswood together and bending the frame components to a rough shape. I start by bundling 9 pieces of 1/32" strips together and soaking them in hot water for 15 minutes.
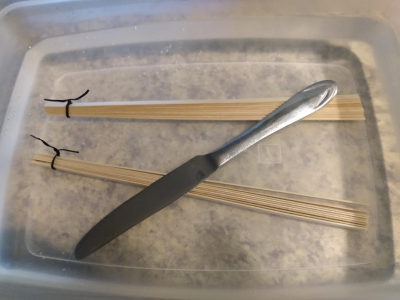
I then remove the wire ties and lay the strips atop my form, centering them via eyeball. The strips are well oversized so there is room for error when centering. The fixture will hold two sets of frames at one time. No glue has been added to the strips. That comes later. I'm bending nothing but loose, wet wood.
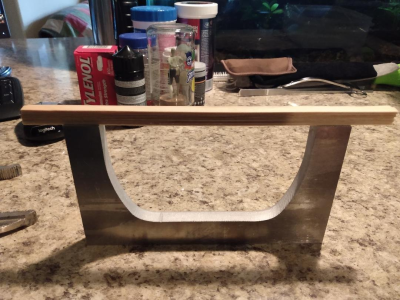
I then add the follower atop the strip bundles and center it up via eyeball. With everything centered, I start working the follower down by hand until I can't move it any further... then I use a vise grip to finish the job and compress the strips tightly between the two forms.
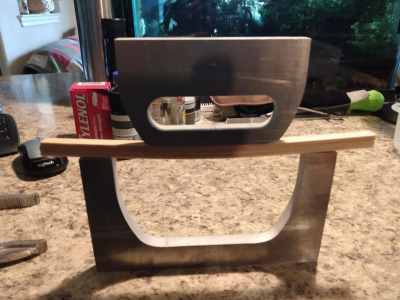
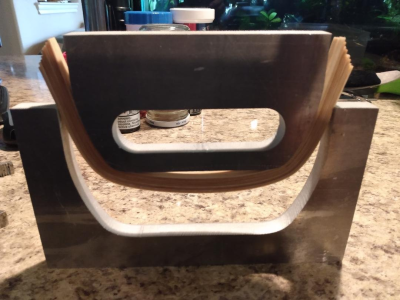
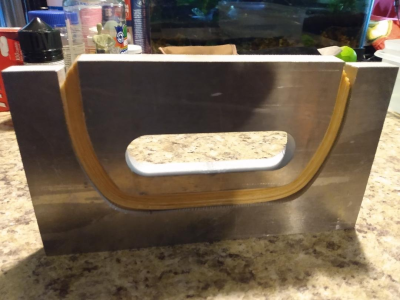
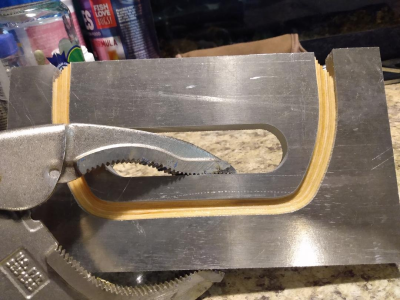
I then bake the form and wood in the oven @ 210 degrees for a while, until mostly dry, then let everything come down to room temperature.
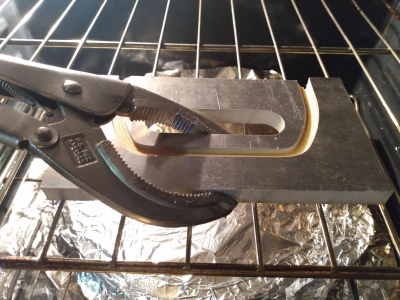
When cool, this is what I have. I tape the bundles together and put them aside. I won't do anything else to them until I have all of the boat's mid-sections of 18 sets of frames bent. I'll then return these bent frames to the form and start gluing them up.
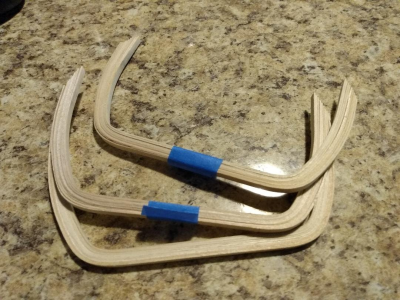
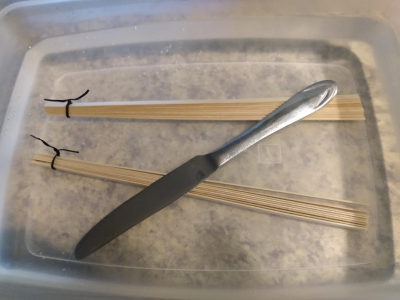
I then remove the wire ties and lay the strips atop my form, centering them via eyeball. The strips are well oversized so there is room for error when centering. The fixture will hold two sets of frames at one time. No glue has been added to the strips. That comes later. I'm bending nothing but loose, wet wood.
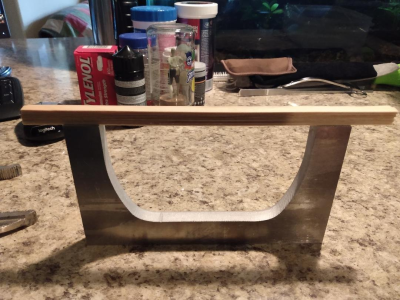
I then add the follower atop the strip bundles and center it up via eyeball. With everything centered, I start working the follower down by hand until I can't move it any further... then I use a vise grip to finish the job and compress the strips tightly between the two forms.
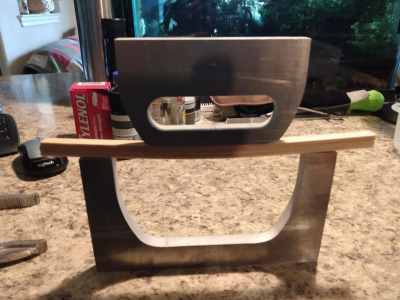
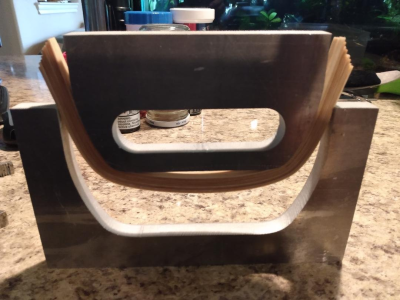
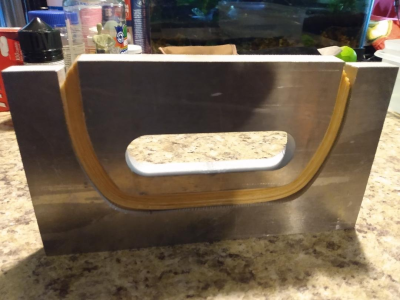
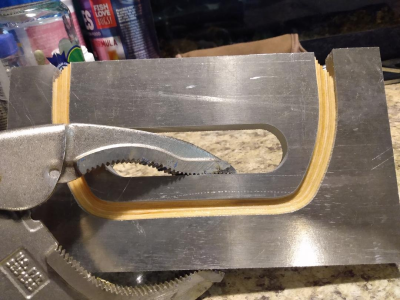
I then bake the form and wood in the oven @ 210 degrees for a while, until mostly dry, then let everything come down to room temperature.
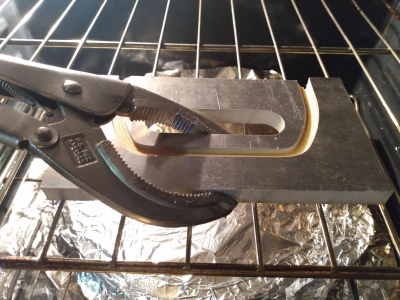
When cool, this is what I have. I tape the bundles together and put them aside. I won't do anything else to them until I have all of the boat's mid-sections of 18 sets of frames bent. I'll then return these bent frames to the form and start gluing them up.
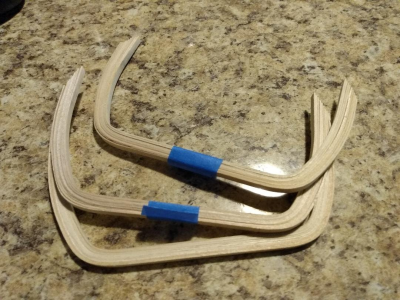