Hi guys,
The transom is mostly finished. Only need to install the top timbers for the quarter galleries, and the filling frames below the stern. I'll probably install filling transoms after the ship is out of the build jig., and the friable top-timbers after Installing interior bands and clamps.
Overall, the stern timbers are installed where they are supposed to be, symmetrical, and true to plan. There are details and joinery that are not perfect, but were fixed with filing, and filling.
When I finish a section, I always think of mistakes made, and what should I have done differently.
My main mistake was to initially install Y-8 without its top-timber, and without Y-7 adjacent to keep perspective and flow. This made it very hard to get the correct orientation and angle of the Y-8 top timber, and to fix it correctly in place.
A second mistake was to trim the wing transom's bevels too tightly, and to cut the grooves for the curved stern pieces before the sternpost was attached. I had to re-cut the top and then repair the top of the wing transom. The later part off the wing transom was too thin, and I had to add pieces of wood to make the joint between the fashion piece and Y-8 top timber- probably the most complex and multi-faceted joint in the ship.
I'm sure that you guys already know this stuff, but I'm just letting everybody know FYI.
If I had to do it over again, I would do the following:
1) Make Y-7 and Y-8 fully and install Y-7 first, followed by Y-8. reinforce the last joint on Y-8 and top timber, (pinned). It is a very fragile part. I would NOT bevel the top timber at this point, but wait until all the stern pieces are installed.
2) Study and figure out how these stern pieces come together and relate to each other. INMO, The "anatomy" in this area is the most complicated in the ship, and the building process and illustrations are not very helpful.
The bottom (half-frame B) of Y-8 fits under stern frame # 4-Stern frames # 1,2, and 3 attach to the side of half frame A.
3) The wing transom should not be completely beveled, but finished later. Install the wing transom after both sides of Y-8 are attached to the stern frames.
Do not cut the notches on the the top-side until the exact location of the stern top-timbers on the transom has been marked with pencil. I taped the top timbers with adhesive tape to the build-jig's parts B17, A, B and C to establish and fix their location and how they land on the transom; and hatre-cut grooves, and later fill in.
Anyway, the stern is structurally correct and according to plan, but has some work-arounds in the joinery.
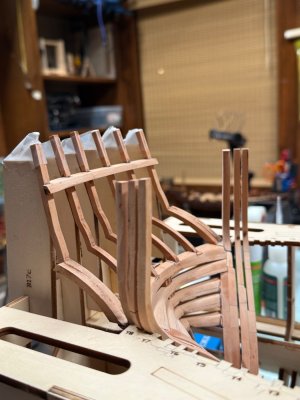
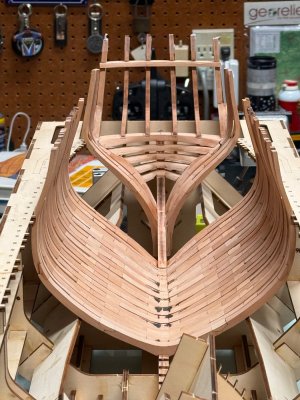
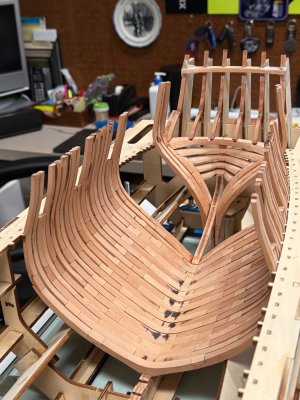
Thanks
Alex R