I'm going to make my first scratch project after months of research. Not sure if this should be posted here as i won't use plans exactly but a model. The problem is that the model is on paper so must be copied on wood. But it won't be a wooden model either as most probably other materials will be used.
Cap San Diego was a hybrid cargo and liner launched in 1961. The "white swan" as was nicknamed is a 159 m, 10000 dwt ship which ran a regular schedule between Germany and South America, completing 120 round trips until 1981. After being sold and running under different names and under Spanish flag and also flags of convenience as a tramp trader, the run-down ship was scheduled for scrapping in 1986, when She was bought by the city of Hamburg
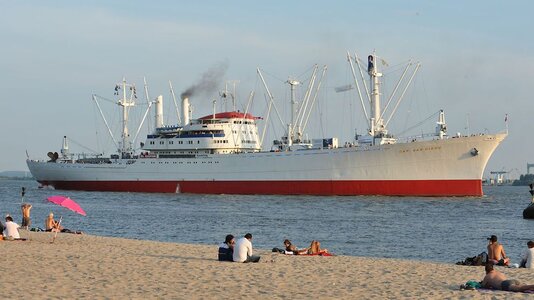
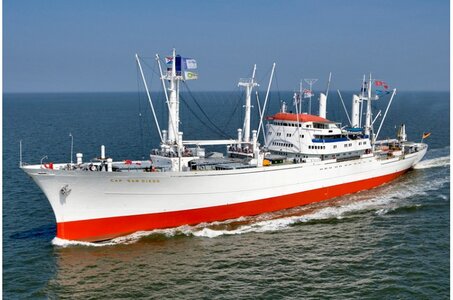
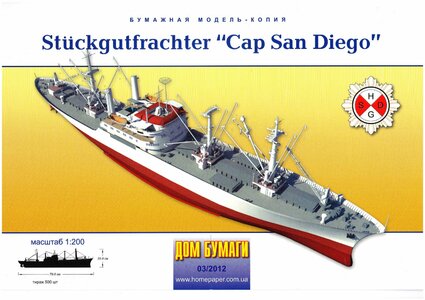
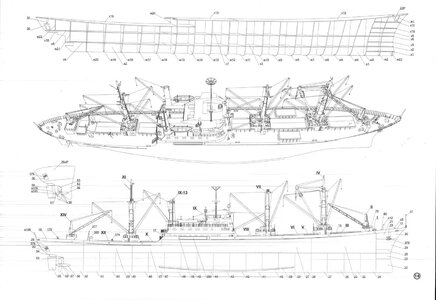
Cap San Diego was a hybrid cargo and liner launched in 1961. The "white swan" as was nicknamed is a 159 m, 10000 dwt ship which ran a regular schedule between Germany and South America, completing 120 round trips until 1981. After being sold and running under different names and under Spanish flag and also flags of convenience as a tramp trader, the run-down ship was scheduled for scrapping in 1986, when She was bought by the city of Hamburg
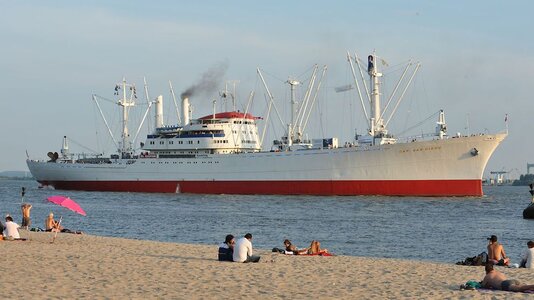
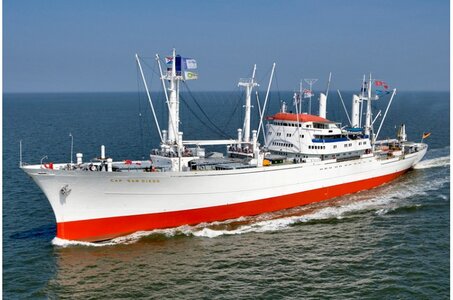
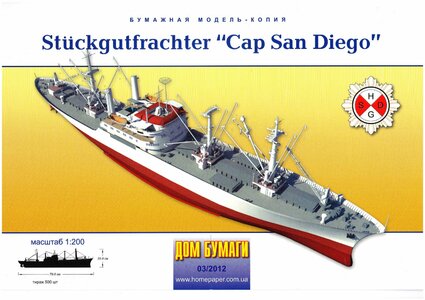
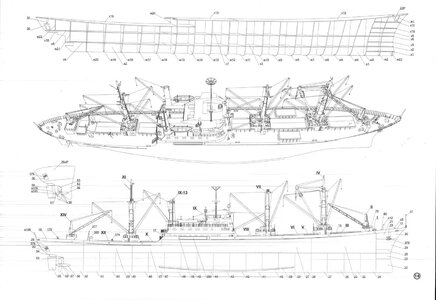